thickness info
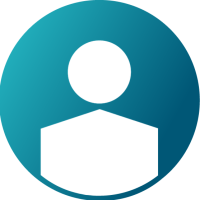

for sheetmetals analysis, most of the times for sol101 and 103 cases, we give uniform thickness
has anyone studied the effect of thinning effect of forming
does giving the actual thickness give lot of variation in results?
is it worth the effort to give actual thickness instead of standard uniform thickness?
any views on this
Answers
-
I don't know any answers to your question exept from the obvious: Different thicknesses in the same material will result in different stress levels. Much higher or lower than those found by doing the same analysis with a unifrom thickness, depends on the material type, loading etc.
I hope I understood your question correctly.
0 -
yes, you have understood it right, but i see that in automotive industry people give uniform thickness without considering forming/thinning effect for running an nastran structural analysis.
people dont take the pain of getting regional thickness from forming analysis and feeding them into the nastran model before running it
does anyone have any case study/example which illustrates whether this effort is useful or not
0 -
Not always true. In some cases, the effect of reduction of thinkness is considered. Besides, each company have their own guidelines to performe the analyses and defined processes. Those guidelines are written by experts and a lot of considerations.
0 -
The complexity of a model depends on many (logical) factors that I suppose most of you know to a certain extend. It all depends on what an analyst or a company considers 'correct' or to put it in another way 'acceptable' for a specific project. Different rules apply in the aerospace industry, compared to those applied in the automotive. To comment on your example, the global model of a car that will be studied in a virtual crash test analysis doesn't require that much of detail... So, it is logical for the automotive FE analysts not to spend too much time in defining all the thicknesses of their shell elements, to save modeling time and use the time in creating a more detailed model of a specific part of the car for a more detailed analysis if that is required.
A good way of working is first to ask yourself if what you want to model can be modelled with shells and second try to answer the question about the thickness variation by creating a simple model, solve it and compare the results with those manifasting from analytical calculations (i.e. Roark) and/or experimental data.
0 -
does HM have any option to read and assign the thickness info coming from a third party forming analysis software?
0 -
does HM have any option to read and assign the thickness info coming from a third party forming analysis software?
If only they had it implemented... Your are talking about property mapping into a FE model. I remember asking Altair a similar question regarding composite layup information taken from CATIA's composite module. Hypermesh doesn't have such a capability (as far as I know) but they said that hypershape (Altair's optimization module running inside CATIA) can do it.
I haven't tried it though...
0 -
hmm, I guess I will have to write a macro to do that for my automation project
0 -
hmm, I guess I will have to write a macro to do that for my automation project
If possible, please share your idea with the rest of us...
kind regards
mvass
0 -
will have to write a translator to read the format and then assign it to the elements
0 -
HyperMesh does have the ability to read, store, and export thickness values assigned to nodes or elements. One method is to use the HyperWorks Results Mapper Process Manager template in HyperView (see the Manufacturing Solutions help documentation) to project forming results onto the structural mesh and then generate a structural mesh model with the applied values. This can be imported into HM. There are also a number of tools that will translate results in the 'dynain' format that you can get from an incremental LS-DYNA simulation or a 1-step RADIOSS model. I have used one from Simulia for ABAQUS format, as well as a macro from Altair.
0 -
HyperMesh does have the ability to read, store, and export thickness values assigned to nodes or elements. One method is to use the HyperWorks Results Mapper Process Manager template in HyperView (see the Manufacturing Solutions help documentation) to project forming results onto the structural mesh and then generate a structural mesh model with the applied values. This can be imported into HM. There are also a number of tools that will translate results in the 'dynain' format that you can get from an incremental LS-DYNA simulation or a 1-step RADIOSS model. I have used one from Simulia for ABAQUS format, as well as a macro from Altair.
I knew this 'results mapper' looked promissing however i've never used... That's a very good piece of information there etg. Can you please provide us with more information about thickness mapping using the results mapper? If it is possible for you of course.
Thanks a lot!
0 -
@ETG:
just to have an idea: If we have composite ply layup from a CATIA model, can we map this information to our HM FE model using the results mapper?
It is very important to know if Results Mapper can perform something like that.
Thank you in advance!
0 -
hello,
i'm looking of export thickness values from PamStamp via M0 file, to convert my pamStamp model to Abaqus. I knew that it is possible by Hypercrash, but it's the first time i use hyperwoks and i don't know well how does it works. Can some one tell me how can i input my M0 file onto my model using Hypermesh or perhaps HyperWorks Results Mapper Process Manager template?
Thks
0 -
Hi
I have same problem with pamstamp software.
I would like to convert my pamstamp model, mesh and stress e thickness information, in to abaqus file.
Someone can help me ?
It is possibile this convert file ?
Thank you in advance
Adriano
0