LAW2 gives different results according to failure property input? [SOLVED]
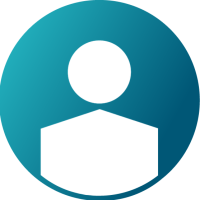

Hello,
I am using Johnson Cook model (LAW2) for drop test of my part, and am getting weird results.
1. If I input EPS_max (ultimate plastic strain), I get the following result: 0.2IN_JC_UTS_strain.avi
2. If instead I input SIG_max (ultimate tensile strength), I get the following result: 0.2IN_JC_UTS_stress.avi
3. If I do not enter any of these 2 parameters, I get the following result: 0.2IN_JC_UTS_no_fail.avi
Why is there so much difference in the results between the first two? They should be pretty close. Also for the first one, why are the dead elements not taking stress, while for the second they are taking stress?
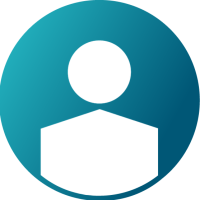

Attached is a video of the contact. The elements of the block are getting deleted. I want them to get disconnected from other elements, but stay there. When they are deleted, it creates a gap which causes more movement of the block downwards. Please suggest what I should do?
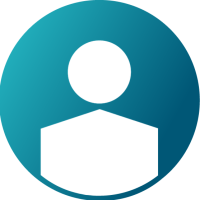

Bongirs,
We don't have any options to create material chipping off in either of these laws. Only we can delete the failed elements.
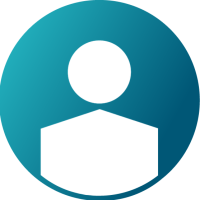

Is there any other way or law by which we can have the chipped off elements? ANSYS has this ability....
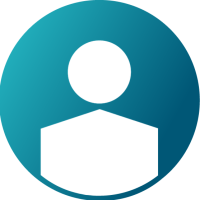

Hi Bongirs,
Can you add /FAIL/TAB with Ifal for solid set to 1?
This formulation is a strain based failure formulation. Try this and let me know if this worked or not.
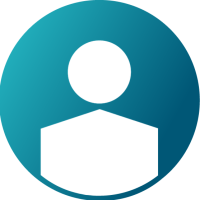

Prakash, I see that this failure model provides a lot of flexibility in deciding the plastic strain for which the element will fail. Although it is a great tool, that is not what I am currently looking for. It is fine with me even if the failure strain is a constant value. What I am looking for is that the element upon reaching the failure should 'pause' or vaguely speaking become rigid. For example, if you see the masked.avi video, the elements that are reaching failure strain get deleted. In real world scenario its like the elements got vapourised in the air. That is not true realistically. Even if the elements reach their failure strain, they should stop absorbing deforming (or stop absorbing energy) but they should 'stay' where they are even if they are disconnected from their parent component.
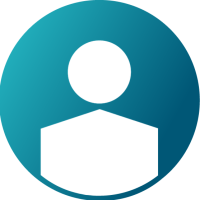

Bongirs,
Since the elements are failed there is no point in keeping it and so they are deleted. We don't have any options to create material chipping off, as you see in real world scenario.
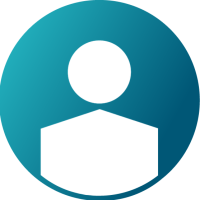

Alright Thank you very much for your help George and Prakash!
HI all,
I am looking for a failure model for simple tensile test. Please clarify few things which mentioned below.
a = yield strength
b= UTS
c= hardening exponent
EPS max is strain at Breaking point at the Stress-strain curve
SIG Max is the breaking strength
Is that correct ?
So my elements will start delete after the breaking point right ?
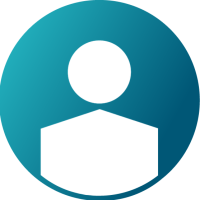

Hi,
Yes, when the plastic strain reaches EPS, shell elements gets deleted.
Firstly, I have a reference curve and another curve at a higher strain rate for the object material. So by calculating c, I can have strain rate effect using LAW2. But I cannot have strain rate effect with LAW36. As strain rate effect is playing a major role for my object, I will use LAW2 for the object and LAW36 for the block. The block is basically concrete and I only have one curve for it.
Secondly, I wanted to know whether it is possible to have elements separated from their original surrounding nodes but still active using either of the laws? The object is chipping off some of the concrete, but the concrete element is getting deleted immediately instead of getting chipped off. If it gets separated from the original block, it still should be in contact with the object to obstruct the displacement of the object.