LAW2 gives different results according to failure property input? [SOLVED]
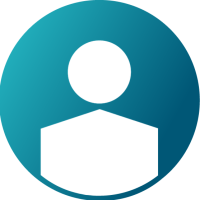

Hello,
I am using Johnson Cook model (LAW2) for drop test of my part, and am getting weird results.
1. If I input EPS_max (ultimate plastic strain), I get the following result: 0.2IN_JC_UTS_strain.avi
2. If instead I input SIG_max (ultimate tensile strength), I get the following result: 0.2IN_JC_UTS_stress.avi
3. If I do not enter any of these 2 parameters, I get the following result: 0.2IN_JC_UTS_no_fail.avi
Why is there so much difference in the results between the first two? They should be pretty close. Also for the first one, why are the dead elements not taking stress, while for the second they are taking stress?
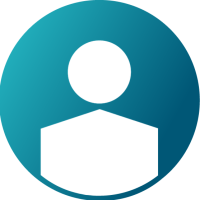

Hello Prakash,
Thank you for your reply!
1. What do you mean by elements get deleted? Do they become rigid elements or something else? Can you please explain this pertaining stress-strain or load-deformation?
2. So when the element stress reaches SIG_max value what happens to that element? Is it deleted or become rigid or does something else? I am not able to understand how this case is different from above case?
3. What is ICC or strain rate effect? Could not understand much from the guide. The constant C in Johnson Cook takes care of strain, then what is this new parameter? What does it do if it is 0 or 2?
4. When none of these failure conditions are applied, the model is behaving quite differently. So should I or should I not input the failure stress/strain values?
Regards,
Sumit
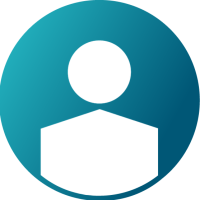

Plastic strain failure can be used to model ductile failure in materials. Failure initiation is based on the effective plastic strain in the material. The user inputs a maximum plastic strain value and when the material effective plastic strain is greater than the user defined maximum, failure initiation occurs and those elements will be deleted from the model.
Similarly when the stress reaches the SIG_max value failure is initiated and the material instantaneously fails.
When none of these values are provided a default value of 1030 is applied and there will be no failures in the model. The model will deform giving the maximum plastic strain. It will behave differently wrt the other two cases.
Johnson Cook material (/MAT/LAW2) material model represent the strength behavior of materials, typically metals, subjected to large strains and high strain rates. The rate of loading for a plastic material is a key component of how we perceive its performance. High strain rates tend to favor the elastic properties of materials
When ICC is set to 1,strain rate will effect on SIG_max and when ICC is set to 2 there will be no strain rate effect on SIG_max
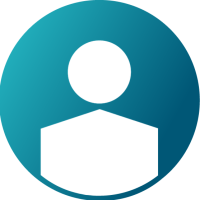

Hello George,
Thank you for your reply! It helped me clear some doubts. I have some further questions:
1. When you say that the elements get deleted on reaching the max plastic strain, I agree. The deleted elements have 0 stress and are broken apart from the object. That is what I am getting in my simulation. No problem here.
2. But for max stress, the elements are reaching the max value but not getting deleted, please see the video. Why is this so? The elements have the max stress as constant and stay connected to the object. ICC is 1.
3. Can the reference stress-strain curve be with any rate or is there some requirement for that? The value of c can be calculated according to the chosen reference curve. Correct me if I am wrong?
Your reply was quite elaborate and helpful! Thanks!
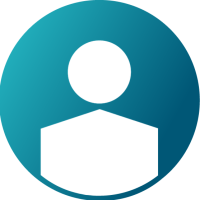

Normally when stress reaches the SIG_max value failure will be initiated and the material instantaneously fails. How much was the SIG_max value provided for this analysis?
Can you share this input deck?
Extract the main parameters from the true stress versus true strain curve, to define the material law (Johnson-Cook law and material coefficients) for /MAT/LAW2. There is no other requirement for the input parameters.
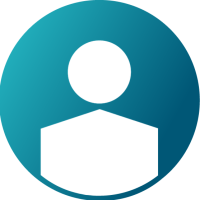

The elements are reaching the SIG_max value. Actually they won't go beyond that even though the elements continue to have more strain. See below the material and property card details.
What is going wrong with my animation? Are the red elements deleted? What do you mean by deleted - they become rigid elements/they are not used for creating assembled stiffness matrix or some other meaning for deleted?
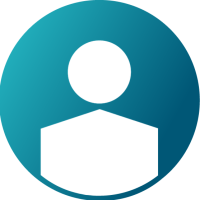

Hi,
Sorry Bongirs, there is a bit clarification for the above SIG_max answer. Only for maximum plastic strain value the elements will get deleted once the model reaches the same value.
But for SIG_max, the stress value of the model will not go beyond the value you provide. As the material reaches the plastic range it will continue to have more strain but since the user has provided a SIG_max value, the stress will not go beyond it.
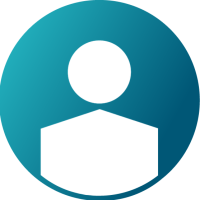

Now that is exactly what I was expecting from the beginning. Thanks for your confirmation!
1. Can you tell me what is meant by deleting the elements? I am asking because if you see the animation for strain failure, the elements that are 'deleted' continue to deform although they have 0 stress. How are the forces transferred to the 'alive' elements as only the 'deleted' elements are in contact with RWALL.
2. Also, for maintaining the SIG_max value, does HyperMesh change the stiffness matrix? As F=Kd is solved first to obtain strain, then stress is calculated. If stress and strain both are independent then material property has to be dependent on these 2 results. You cannot have all independent variables in this equation -> stress = Young's modulus * strain. Can you please clarify?
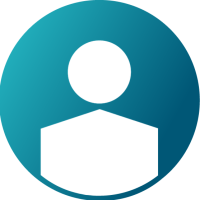

When the maximum stress is reached during computation, the stress remains constant and material undergoes deformation until the maximum plastic strain. Element rupture occurs if the plastic strain is larger than Plastic strain failure value and the ruptured element is deleted. By providing these failure criteria the user will be interested to know from where the rupture will be initiated. This is the process happening when we provide these maximum values for stress and plastic strain.
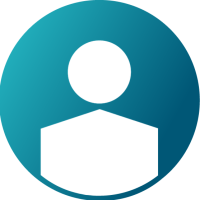

What do you mean by 'ruptured element gets deleted'? There is no crack development, nor separation of elements. Also, what do you mean by 'element gets deleted'? I have been asking this repeatedly but you have been dodging that one.
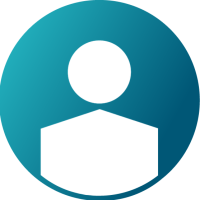

Element rupture occurs when the elements reach the maximum plastic strain value and those failed elements are deleted from the model.
Attached image shows a can crush simulation. When the eps_max reached the user defined value you can see that rupture occurred in the model. And those failed elements were deleted from the model..
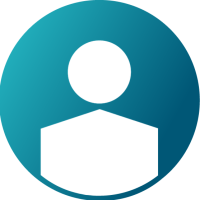

George, thank you for your reply.
I understand from your discussion that, when the element strain reaches EPS_MAX, the element is removed from existence. It appears similar on your image. But can you check the video that I uploaded in the question. The elements that are 'deleted' are still displayed in the model with 0 stress. Further you can observe that they are deforming. So according to your discussion, if these elements are deleted then they should not be displayed at all because they are deleted, right? I understand what you are saying but the results from HyperMesh are not in line with the logical result expected. Correct me if I am wrong.
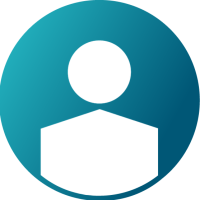

Bongirs,
This Eps_max failure criteria is applicable for shell elements only. Just noticed that you are using solid elements. For solids, the element will not get deleted as we see in shell elements.
If you want to define failure/rupture criteria for solid elements please use /FAIL/JOHNSON criteria. A tutorial (Example 26 - Ruptured Plate) is also available on this.
Please refer the tutorial.
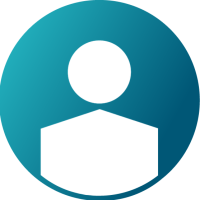

Thanks George, I will check the tutorial. Do you have the number like RD-5050?
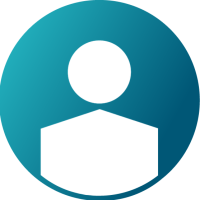

Can you give the title of that tutorial (RD 5050)?.
What is the tutorial number?
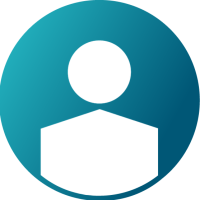

A tutorial (Example 26 - Ruptured Plate) is also available on this.
I was asking the tutorial number for the example you mentioned.
See below the numbers, 5050 was just an example of what I was asking.
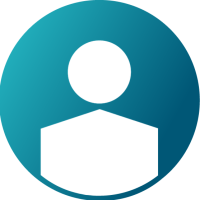
PFA pdf & model file of Rupture plate.This must be in Radioss examples.
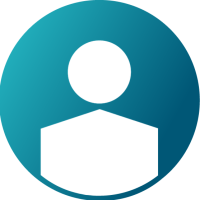

Rahul and George, the example does not show how to create the failure model in HyperMesh. Can you tell me how to create this failure model in HyperMesh? I have created LAW2 Johnson Cook already but cannot see the failure parameters. I want to use the Johnson failure model. Please help.
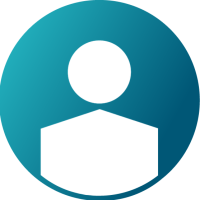

In properties, select type as Failure_Model and select card image as FAIL_JOHNSON.
The relationship (failure curve) is defined by three ductile failure parameters D1,D2 and D3.
D is defined as a damage variable which varies between 0 (material not damaged) and 1 (fully failed material). The failure criterion is based on the value of equivalent plastic strain at element integration points.
You can verify various papers published on determining the experimental failure parameters (D!, D2, D3 values) of Johnson-Cook material model.
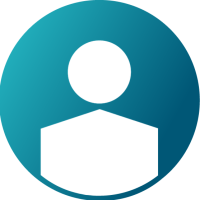

George, that was greatly helpful!! Surprised that the documentation does not mention how to create the failure model.
Now, I want to understand that this property is applied to a material and not a component, right? Like the material we select for mat_id gets this property.
Also, I already have a Type 14 (solid) property for my component. So I don't have to assign this failure property to any component?
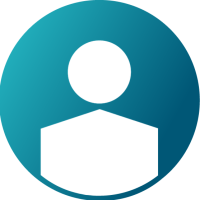

Yes, you are right. The failure criteria is assigned to the material.
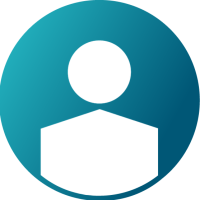

George, I am not quite sure why we should use this card? If you can help me clear my doubt that would be helpful.
We are already providing the failure strain in the LAW2 model, which is EPS_MAX.
So the failure model of Johnson, just allows us to have flexible failure strain, correct?
I did not understand the terms for sigma* which is sigma m divided by sigma nu m. What are these terms?
Now, in my case I already know the failure strain which is fixed. Should I then use the failure model still? In that case I will make D1 = EPS_MAX, D2=D3=D4=D5=0. So the epsilon f would always be D1=EPS_MAX from LAW2. Do you see what I am saying?
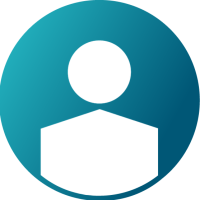

Bongirs,
As mentioned earlier Eps_Max failure criteria is applicable for shell elements only. Deletion of elements as soon as it reaches Eps_Max failure criteria will happen only for shell elements. And for solid elements using /MAT/LAW2 it will not get deleted. If you have the material curve (stress-strain) you can use /MAT/LAW36 and there if you provide Eps_max, the solid elements get deleted when Eps_max is reached
Structural impact involves events such as plastic flow at high strain rates, possible local increase of temperature, and material fracture. This characterization involves not only the stress-strain response at large strains, different strain rates and temperatures, but also the accumulation of damage and the mode of failure. When these factors are considered failure models are used.Such complex material behavior involving fracture is difficult to describe in analytical models.
Sigma *= sigma m/sigma nu m is the stress triaxiality ratio (where sigma m is the mean stress and sigma nu m is the product of factors representing strain hardening, strain rate and temperature)
D1 - D5 values has to be found using the equation provided.
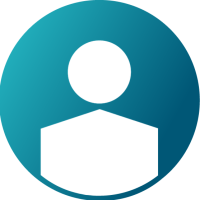

Yes I understand my mistake now, LAW2 element deletion only works for shell elements and not for tetra. So what exactly happens to these tetra elements?
Attached is the drop test of an object on a concrete block. If you slow the video, you will see that the concrete block reaches its EPS_MAX that I had set. These elements still continue to have contact interface with the object. I was expecting that the failed concrete elements will either fly away or get hidden. But now from your reply I understand that RADIOSS does not consider these as failed elements, but something else. How do you suggest I should make these failed elements either chip off from the block or hide so that they are not in contact with the object anymore?
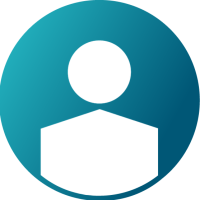

Depending on the material law, the solid elements are not deleted after the criteria Eps_max is reached. For Material Laws 2, only the deviatoric part of the stress tensor is set to zero, the internal pressure of the solid is still computed. But for Material Laws 36 the solid elements are deleted when Eps_max is reached.
You can try with Material Law 36 with the experimental stress-strain curve. Please refer Example 11- Tensile Test from RADIOSS help for more details on it.
Hi Bongris,
I think this is intended. Since you are giving a condition for strain the elements gets deleted when the maximum strain reaches to furnished plastic strain.
When it comes to stress, the maximum stress is calculated based on the SIG_Max 0, if the ICC (strain rate effect is set to default). You can set it to zero or no strain rate effect by changing ICC to 2.