Contact beetween soft deformable bodies
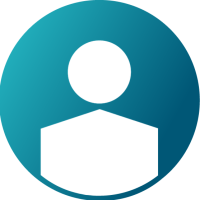

Hi everybody.
I've been experiencing big problems with contacts in Radioss using tetra mesh.
Especially when simulating soft materials (poliurethanic rubber).
I've already tried interface type 7 and type 3 but the elements get instably ruined and the analysis always stops with 'zero or negative volume error'.
I've tried tetra4, tetraDG and tetra10 but it doesn't help.
Anybody can suggest any alternative or any control parameter (on both the interface or the tetra elements property definitions) to manage the problem and get more stable contacts with tetras?
Thank you very much
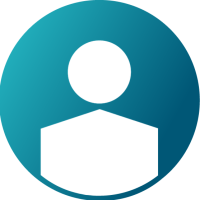

Hi everybody.
I've been experiencing big problems with contacts in Radioss using tetra mesh.
Especially when simulating soft materials (poliurethanic rubber).
I've already tried interface type 7 and type 3 but the elements get instably ruined and the analysis always stops with 'zero or negative volume error'.
I've tried tetra4, tetraDG and tetra10 but it doesn't help.
Anybody can suggest any alternative or any control parameter (on both the interface or the tetra elements property definitions) to manage the problem and get more stable contacts with tetras?
Thank you very much
Try using a 0.001mm surface over your parts (node to node) with a linear elastic material (some arbitrary material nearly no effect onto the system). So you can prevent the unwanted shape distortion and negative volume error.
Second solution is to change the element formulation, check the radioss benchmark model taurus or neon maybe, check the foam material and part and failure model on it. It's nearly the same.
Hi, I am not an expert in RADIOSS block, since I am using NASTRAN as my solver, however would it be possible for you to describe briefly what you are trying to do? Do you have two layers of shells elements and an interface with tetras between them, or something else? Rubber is a hyperelastic material so I suppose it that you have assigned to it the correct material properties, right?