Creating a 3D Hex Mesh whose surface elements can be extruded out to another component. ALE Application
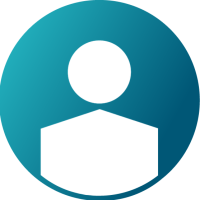

Currently I am facing problem where one ALE group “leaks” into another. I am almost positive that the leaking from the inner ALE group occurs because the inner mesh is a tetrahedral mesh while the outer mesh is comprised of hex elements. I think that even though nodal positions are shared between the tetrahedral and hexahedral elements, the fact that the tetrahedral elements are essentially half the size of their neighboring hex elements is the cause for extreme leakage when simulations are performed. I have a few questions about some meshing techniques that I feel could resolve my current troubles.
Below is a brief description of what it is I want to accomplish, but cannot yet figure out.
I need to find a way to create a 3D hex mesh for the inner ALE component that can have the surface elements be extruded out from the inner ALE component to the outer ALE component. I realize that the “shrinkwrap” option can create a 3D hex mesh, but the surface elements in this option cannot be extruded outward. In looking at the tetramesh panel, it would seem to me that there should be an option to perform this same method of meshing, but create a 3D mesh that matches surface the hex elements. I have not yet found a way to do this. Is there a way to do this?
Below is a step by step description of my current methodology for meshing my model. The concerns are restated at the end of this section.
1.) I create a 2D QUAD mesh through the 2D automatic panel on the surface of the inner most component
2.) I extrude this 2D surface mesh to the outer ALE component through the 3D --> Solid Map --> Ends Only Panel, by selecting “source geom - surf” (inner, surface mesh elements) and “dest geom - surf”. When these new 3D elements are created, a new “component” is also made.
3.) I repeat this extrusion step for all of the surfaces that need to be meshed.
4.) I then inspect all regions where these newly extruded meshes come together. Often the case is that the nodes of these elements do not line up. It is absolutely paramount that these nodes line up or else models will not run.
5.) When elements are found that do not have adjoining nodes, I delete the layers of elements that need to be edited (through the Tools -->Delete panel) and then create new elements that fit perfectly by accessing the 3D --> Edit Element -->Create Element via Node List.
a. This is a tedious process, especially when there are a lot of elements to adjust but it is the only way I have found that works, and that I know how to do.
6.) Once the outer ALE mesh is set, I try to create the 3D mesh for the inner ALE group.
a. THIS IS REALLY WHERE MY CURRENT PROBLEM OCCURS
**** I have not yet found a way other than the tetramesh option to create this 3D mesh. None of the solidmeshing techniques seem to fit my needs. It seems that there should be a similar option to the tetramesh panel in which I could say “take this surface mesh, match it, and create only hex elements” but as of now I know of no such option.
**** Also I have looked into the “shrinkwrap” meshing option which will generate a 3D hex mesh, but the elements created in the shrinkwrap option cannot be extruded using the solid meshing option I outlined above.
I have noticed that there are options in Hypermesh where one can create partitions/divisions that make a solid part “mappable”. I am not very familiar with these options, but they seem like maybe they would be useful in creating a 3D hex mesh. If this is a viable option, please let me know how I can accomplish my aims through creating partitions/divisions.
Yours,
Bradley Zentgraf
zentgrafbw@gmail.com
Answers
-
Image of Model that Needs Meshing
I should probably add that the geometry that is trying to be meshed is not a simple geometry. It is not a simple cylinder or rectangle. The geometry is comprised of 2 cylinders, one which branches off of the other. A picture has been included for clarity.
http://imageshack.us/photo/my-images/191/branchi.jpg/
Uploaded with ImageShack.us
0 -
Image of Model that Needs Meshing
I should probably add that the geometry that is trying to be meshed is not a simple geometry. It is not a simple cylinder or rectangle. The geometry is comprised of 2 cylinders, one which branches off of the other. A picture has been included for clarity.
http://imageshack.us/photo/my-images/191/branchi.jpg/
Uploaded with ImageShack.us
is it possible for you to upload your geometry, so i could try something ?
0