Quasistatic analysis of metal honeycomb
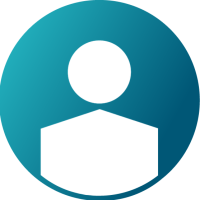

Hi Im doing a project on aluminum energy absorbers and i need to do a quasi static analysis on my designed aluminum honeycomb. Basically a compression test. Im trying to do it in RADIOSS but have a few doubts.
1. Since it is a metal that is aluminum what mat law to choose is it 36 or 1 or 28(for honeycomb but i dont have the required curves, it is for foam right?mine is metal<?xml version="1.0" encoding="UTF-8"?><?xml version="1.0" encoding="UTF-8"?>
<?xml version="1.0" encoding="UTF-8"?>
).
2. I have to give contact between the honeycomb and the two anvils that is top and bottom. What type of contact should i give?
3. I have created one rigid body body that is is the top anvil to give it imposed displacement. The bottom anvil i fixed.
4. And my total displacement is 23mm and the time taken was 46 mins at a rate of 0.5mm/min in the physical test in the utm.
5. Im trying to replicate this compression to get Force vs deflection graph and energy absorbed.
Im attaching the pictures of my model and also my hm file.
Answers
-
Hi,
1) For starting runs, you can use MAT LAW 36 itself . Also MAT 28 is compatible with solid element and you have shell element model. A you have modelled geometry as of he absorber, this should work
2) For contact you can use TYPE 7 or type 19 also
3) This seems to be ok
4) Radioss explict run will not be able to run for such long time due to time step limits. You can ramp up the imposed displacement of 23 mm in 0.3 sec and compare the results
5) On run you will get data required in point 5 in the form of time history graph (T01)
0 -
Hi Vaibhav,
1. /MAT/LAW28 describes a nonlinear elasto-plastic material, usually used to model honeycomb or foam material that is easily crushable material upon loading.
If you don't have all the parameters you can try with /MAT/LAW36 or /MAT/LAW2.
2.You can define these contacts using Type 7 interface in RADIOSS. You can also model rigid wall for bottom anvil.
Use the recommended contact parameters for interface Type 7 which are as shown below:
Istf=4
Igap=2
Fscale_Gap=0.8
INACTI=6
Gap_min=
Fric = 0.1
Iform=2.
Ensure no penetrations are present after contact is defined. Please go through this link (https://forum.altairhyperworks.com/index.php?/topic/20207-new-feature-in-hw-2017-–-collision-detection-tool/), which shows checking penetrations in interface and clearing those.
3.The approach is fine. As told above, you can also model a rigid wall instead of bottom anvil.
4.Explicit cases are high dynamic non linear analyses problems where the normal run time will be in milliseconds only. So, as Gopal mentioned above ramp up the load in a span of 300 milliseconds and run the analysis. For guidelines on load ramping in RADIOSS please go through https://altairuniversity.com/learning-library/7-guidelines-to-apply-quasi-static-load-in-explicit-simulation/
5.Create output blocks for time history file and using this you can create the curves (Cross plot option in HyperGraph: Attached document shows creating cross plot in HyperGraph)
Finally, we have a similar tutorial in our Learning Library which you can access at https://altairuniversity.com/learning-library/modeling-and-analysis-of-honeycomb-impact-attenuator/
Please go through the same so that you will get the modelling concepts easily.
0 -
@George P Johnson and @gopal_rathore Thanks for your suggestions. But im facing a bigger problem of intersections and penetrations and im unable to reduce or remove them. I also checked the link you gave above but that is disturbing the model even more. First i have to remove these intersections and penetrations and only then can i go mforward in my analysis. When im trying to run the analysis it is showing four errors. Already model i attached before now im attaching the out file.
1. error 286
2. error 534
3. error 60 4. Error 226.<?xml version="1.0" encoding="UTF-8"?>
0 -
HI ALL THE OTHER ERRORS ARE CLEARED. NOW ONLY PENETRATION ERROR 611 IS LEFT THERE ARE MANY PENETRATIONS NOT ABLE TO CLEAR THEM.
0 -
Hi,
Please share the model file so that we will try to fix these penetrations.
0 -
YA BY TRANSLATING THAEANVILS UP AND DOWN I CLEARED THE PENETRATIONS BETWEEN THE ANVIL AND THE HONEYCOMB. NOW THE PENTRATIONS IN THE HONEYCOMB EMAIN. ACTUALLY MY HONEYCOMB IS MADE OF TWO THICKNESS SO THERE ARE PENTRATIONS IIN THE THICK SHELL AND THE THIN SHELL. now agian i ran radioss iy showed no errors. But now the computation time is too large that is 10067892 secs. What to do. Im sharing the screenshot and model.
<?xml version="1.0" encoding="UTF-8"?>
0 -
-
Hi,
It seems you have given only displacement/velocity to the impactor. You also need to constraint in all directions except the direction of motion. Then this will not happen
0 -
Hi,
For the impactor fix the dof in all directions except in the direction of loading, ie in your case fix all the dof for the anvil except in X direction and try running.
0 -
hi. For imp displacement there are no directions to constrain. Only scale x and scale y . I tried by making scale y as 0. Now the anvil is not falling off but rather the load is being applied more to one side, Why is this. What can i do to rectify this. I have given mass to the anvil by sung admas option from 1D.
<?xml version="1.0" encoding="UTF-8"?>
0 -
Hi,
Try these steps:
- Make the impactor rigid.
- Create a boundary condition with all dof fixed except in X and assign the same to the master node of the above created rigid body.
- Now assign the imposed displacement to the rigid master node in X direction.
Keep the Scale X and Scale Y as 1. These scaling values will scale the function coordinates (X or Y) created for imposed load.
0 -
Case 1:
I gave spc condition to the impactor master node and constrained it in all dof except x. And I gave an “admass” to the impactor. The compression is happening but the impactor is also deforming like a cap. I gave MAT_2 for the impactor.
Case 2:
And when I am giving mass to the Rbody. The impactor is moving one side although I fixed all dof except X.
What to do.
0 -
Hi,
By making a component rigid we are making that part non deformable under any loading conditions and it seems like there's some modelling issue in your model. Please share the file so that we can review and can help you to solve this.
0 -
ok im sharing the file. Waiting for reply.
0 -
Hi,
The updated files has been sent to you.
0 -
@George P Johnson thank you very much for the model corrections. I ran the analysis it ran very nicely.
But there is one problem: In mesh quality, there are some failed elements and I think ( I may be wrong) because of which the compression is taking place very nicely for the whole structure except the edges. The edges are coming out like a loop. I'm attaching a screenshot.
I tried masking the elements but nearly qaurter of the elements dissapear when i mask the failed elements.
I'm getting the graph also almost correct but I guess because of this edges may be some limitation is occurring in forming the correct graph.
<?xml version="1.0" encoding="UTF-8"?>
0 -
Hi,
This seems like some connectivity issues between the thick and thin parts in the model.
Please try with the modified model which I have sent to you.
0 -
ya that mesh fail i checked for your model only the modified one. It is coming like that only at the edges the rest of the mesh is fine.
0 -
When I changed the material to mat 36 the compression is happening nicely. But in the force vs deflection graphthe force is very less in terms of 1000N. But when I used MAT 2 I got force in 15KN.
In my actual test I got close to 15KN.
But with mat 2 the deformation is not happening correctly. With mat 36 it is good but force very less
0 -
Hi,
These results depends on the material parameters used. Ensure the parameters are correct, especially the stress-strain curve
0 -
Hi
Case 1:
Previously I have given a stress strain curve starting from zero.
For this curve the deformation was uniform that is progressive folding occurred only problem was force.
Case 2:
Now I have given a curve from yield to plastic region three values. The force is comming OK but now the deformation is not uniform and the run time goes on increasing.
And yield stress function means this curve only that is second one or is it different.
0 -
Hi,
For /MAT/LAW36 you should provide post yield values in stress-strain curve, and the elastic portion of the material is defined by the Young modulus and Poisson’s ratio.
Please refer the image below and you can see the curve values.
Update your material card accordingly and run the analysis.
0 -
The stress strain values I have to take from the material right.
Or after compression of the structure experimentally I obtained stress strain values those should i take
My material is Al 3003
I have graph now of stress stain from literature howt to /can I take post yield from this.
Or I got general properties of Al 3003 from the net from that should I take.
<?xml version="1.0" encoding="UTF-8"?>
0 -
Hi,
You need to take material properties of material i.e a fresh sample . If you have reference graph of it mark the yield point and strain value on graph. Make this as your point on graph by making strain zero and keeping the yield value as it is
0 -
Altair Forum User said:
Hi,
You need to take material properties of material i.e a fresh sample . If you have reference graph of it mark the yield point and strain value on graph. Make this as your point on graph by making strain zero and keeping the yield value as it is
This part how to do with my curve i'm not getting can you help me. And should I define any strain rate for MAT 36. I donno the rate.
0 -
-
Hi
I created the curve and imported it to radioss. And the trend of the graph is important right? Or do units matter here?
Because for my graph stress is in mpa and strain in terms of 10^3.
0 -
Hi
The analysis which I'm doing is explicit radioss right? Is that correct for quasi static analysis?
Or should I use implicit card for radioss? If so how do I use implicit card.
0 -
Hi,
Unit consistency is very important during analysis. The material will behave as per the trend in the graph and unit consistency is required else all the results will jumble up.
I'm not sure about the strain values in your curve ie it shows 10^3. It's represented normally in %. Please cross check the same.
You can do this simulation with explicit approach. Since it involves high deformation and contacts it may be tougher for the implicit run to converge, and so please continue the explicit approach.
0 -
Hi i ran using MAT36 the intial compression is happening but after sometime the material is getting squeezed.
Earlier i tried with MAT2 but that loops came out from side. And MAT2 those parameters hardening parameters(b,c etc) im not getting in the net to define.
0