Optimise ply orientation for minimum deflection
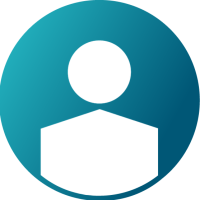

Hello,
I have a laminate with 3 plies. I want to optimise the orientation of these plies such that the deflection of the laminate is minimum under the applied load. I can only perform composite shuffle, but I'm not able to optimise the ply angles. Please advice as to how to proceed to solve this issue
Thanks,
Kushal.
Answers
-
Hi Kushal,
One way to know which ply angles are predominant is by running a Free size analysis for a set of plies (say from +/-(0/10/20/30/....)) and check the results.
Ply angles with maximum thickness are contributing more than others.
The other way is using Size optimization module with Orientation as design variable (see that attached image)
0 -
hello,
I have the same problem: I can change only the ply angles, so I´m using the size optimization and setting a orientation variable for each ply. however is applied the same orientation at all the plys of the laminate (the plys are changing all toghere at the same way). how can i solve this iussue?
0 -
Hi @giannip
Do you mean all plies have same orientation at the end of the optimization?
Is it possible for you to share the model file?
0 -
Hello,
I also want to perform ply orientation optimization for minimum deflection using one of the above mentioned methods (Free Size analysis or Size optimization)
Is there some documentation available for this?
I am not sure what to select for constraints, objectives and what to enter in the optimization fields.
Best regards,
Joep
0 -
-
Hi @Joep
Since you want to design for minimum deflection, you can choose displacement as a constraint with minimizing mass as the objective for example.
0 -
Hello,
I have also taken a look again at the tutorial for composite optimization but it seems you can apply orientations for each ply and then optimise for thickness, but not orientation (so that each ply will be directed into an optimal ply direction)
The picture underneath shows input for orientation I guess. But I cannot find it in the results.
Best,
Joep
0 -
You are looking at a where the thickness is the variable.
The section point 6 refers to balancing constraint where the - and + 45 degrees are balanced (meaning laminate will have the equal number of - and + 45-degree plies)
In size panel, you can select PLY as entity and theta as the variable.
0 -
Hello,
I think I am almost there, since ply angle/orientation thickness is in the optistruct result:
I applies moments in three direction so I think ply orientation should differ for minimum deflection.
Should I not also apply a minimum deflection objective?
I would like to find out the optimal ply direction per ply.
<?xml version="1.0" encoding="UTF-8"?>
Any suggestion?
Bes regards,
Joep
<?xml version="1.0" encoding="UTF-8"?>
0 -
Hello,
I have tried to fix the orientation optimization for minimum deflection. I have a few sets of plied for which I would like to optiimise their orientations based on minimum deflection and stess constraints.
I have shared the model. I think I am almost there, but I cannot visiualse the optimised ply orinetation.
I only get a degree:
<?xml version="1.0" encoding="UTF-8"?>
<?xml version="1.0" encoding="UTF-8"?>
Any suggestion on how to:
-obtain to optimise orientation for individual sets
-visiualise the optimised orientations
-simultaneously optimise for minimum stress
Thanks in advance,
Best regards,
Joep
0 -
-
Hi @Joep In your working directory you should see a file with a .prop extension.
This file has updated property.
Import this with FE overwrite option checked and review/visualize the plies
0 -
Altair Forum User said:
-simultaneously optimise for minimum stress
Use a Stress response.
0 -
Hello Prakash,
Thanks for the advice.
I imported the .prop and checked FE-overwrite but it seems the optimised orientation of all plies is equal.
To my understanding the plies should all have different optimal orientations.
Any idea how to achieve this?
I also tried to review/visulalise the plies in the optimised output file but I cannot find how.
best regards,
Joep
0 -
Hello,
I included a file in which I try to optimise the ply orientation based on deflection and stress using freesize.
I receive different orientations for different plies, but I think to my idea the orientations should differ more than small angle differences.
Is it correct I have to assign orientation design variables as well as thickness variables? And then assign lower and upper bound to it, as can be seen in the picture?
<?xml version="1.0" encoding="UTF-8"?>
<?xml version="1.0" encoding="UTF-8"?>
0 -
-
Can you try with a different orientation on a couple of plies?
0 -
Hello,
I am working on a ply orientation optimization and have the following questions:
-If I want to optimise ply orientation, should I separately assign all plies and separately assign thickness and orientation design variables, fro ALL individual plies?
-If I have a model which consists of over 100 plies, and I want to perform orienation optimization for all plies separately, is there a faster method than to assign everything to each single ply?
-To make this easier I want to organise all plies into components and assemblies, is this to be done manually for all surfaces? (when there are over 100 plies.
Thanks in advance,
Joep
0 -
HI Joep,
You can have a single DESVAR for all plies,
I will check if there is a way to optimize the creation of design variable
0 -
Hello Prakash,
Thanks for the reply. Is it correct if I have a single DESVAR for all plies after optimization all plies are oriented in 1 direction?
Is there an option to do this with the shuffle option?
I would like to select for example 100 surfaces (plies) and optimise for ply direction. I am looking for a way to do this easier tha to select all different plies and assign desvar, etc.
Thanks,
Joep
0 -
Hi @Joep
Altair Forum User said:Thanks for the reply. Is it correct if I have a single DESVAR for all plies after optimization all plies are oriented in 1 direction?
Not necessarily, If this happens in all case then there is something wrong.
Altair Forum User said: Is there an option to do this with the shuffle option?
No, it is not possible
Altair Forum User said:I would like to select for example 100 surfaces (plies) and optimise for ply direction. I am looking for a way to do this easier tha to select all different plies and assign desvar, etc.
I have looked up for scripts, but unfortunately, I didn't have any success.
0 -
Hello Prakash,
Thanks for the reply.
SO if I am correct, in case I have about 50 different surfaces I should apply each surface in a different SET, and then assign each SET to an individual ply.
After this I can assign a single DESVAR to all plies?
Best,
Joep
0 -
Hi Joep,
if the all plies use same elements, then you can create a single set and use it to create all 50 plies.
When you are creating plies, select sets instead of elements.
0 -
Hello Prakash,
I included a model in which I try to optimise ply orientation. The model consists out of a box and thus contains 6 surfaces.
This is a test, in my final model there will be 100 surfaces avaialable.
The goal is to optimise for ply orientations and ply thicknesses for all surfaces but after my optimization ply thickness and orientation for all surfaces is equal.
Would you please take a look at the model?
The goals is to have optimised ply orientation and thickness without having to select each surface individual and assign individual DESVAR, etc.
Thanks in advance
Best,
Joep
0 -
Hi,
thank you for sharing the file, I will get back to you soon,
0 -
HI,
The model looks fine, but the orientation after optimization for both the plies is same. Maybe coincidence. Further investigation is required to arrive at a conclusion
0 -
Hello,
I have the geometry underneath consisiting out of a lot of surfaces.
<?xml version="1.0" encoding="UTF-8"?>
What is the best way to optimise for optimal fibre direction and laminate thickness, so that each surface reveals it's own fibre orientation.
In my previous model I tried assigning all surfaces into a single set:
But after otimization, it seems all the fibre's are directed into the same orientation.
-I need a different orientation and thickness for each surface
Can you help me with this?
Best regards,
Joep
0 -
Hi @Joep
I would suggest either do an orientation or thickness. I am more inclined towards thickness optimization instead of orientation.
You can run a three phase optimization to reduce the weight.
0 -
Oh sorry I solved it off course. It was the spatials in between the name
0