Using MAT36
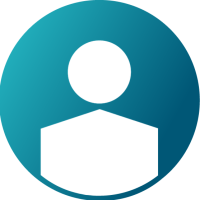

Hi Everyone,
I use Radioss for simulation a tensile test. I used LAW36 - Elastic Plastic Piecewise Linear Material -
I used the failure strain criteria. But the elements were failed before reach the enter failure strain value.
In the atached figure, the red curve is stress - Strain curve. This is the enter data. The blue curve is simulation result. You can see the gap of the end.
Would you show me, how to get the result with the simulation result curve follow enter data?
Thank you!
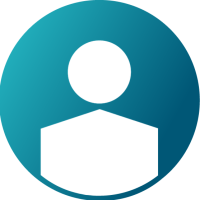

Hi NSKRTLUS and everyone,
I used 5 integration points, but the result is the same. Would you show me how to define 'ANIM/SHELL/EPSP/ALL', I didn't see this option in engine file.
Do you think the simulation speed is too high, or T_freq value (ANIM/DT/Tfreq) is too big?
The hardware testing was test at 4mm/min, totally testing time is 450 seconds. But I setup simulation time 10 seconds, its mean the simulation speed is higher 45 times. If I reduce simulation velocity - increase simulation time - I need to increase ANIM/DT/Tfreq value. Because the Radioss limits the total files (1000 files).
Thank you very much!
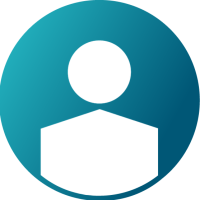

Hi,
if you are using strain rate effects, velocity is very important.
The failure law for this Mat (36) seems to be very simple. I don't use Radioss, but what i can see it is defined either for compression, tension or shear.
So you have to check which component failed (maybe tension) and if your experimental results also fits pure tension (maybe not, e.g. volumetrical failure).
Regards,
Mario
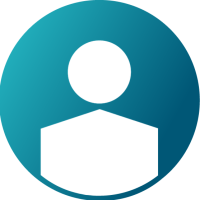

Hi,
if you are using strain rate effects, velocity is very important.
The failure law for this Mat (36) seems to be very simple. I don't use Radioss, but what i can see it is defined either for compression, tension or shear.
So you have to check which component failed (maybe tension) and if your experimental results also fits pure tension (maybe not, e.g. volumetrical failure).
Regards,
Mario
Hi Mario,
If I use LS-Dyna, which material models similar MAT36?
Thank!
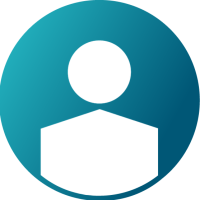

Hi,
in LSDyna it is:
*MAT_24
same as
*MAT_PIECEWISE_LINEAR_PLASTICITY
But it also support only simple failure. Better material is for such a case are *MAT_120 (*MAT_Gurson) or *MAT_120_JC, *MAT_120_RCDC or using the extra card *MAT_ADD_EROSION
Regards,
Mario
Hi Nghiemntut,
I am not sure but i think you would define 'ANIM/SHELL/EPSP/ALL' card in engine file instead of 'ANIM/ELEM/EPSP'.
It would also be helpful to use integration points more than one, for shell elements in /PROP/SHELL card (5 would be enough)