Crushable metal foam modeling - Element distortion
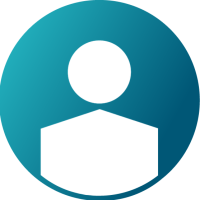

Hi,
I am trying to model Aluminium crushable foam (porosity 8%) in impact analysis problem using RADIOSS block120. I am using LAW 33 visco-elasto-plastic material model and P14_Solid property brick elements (ISOLID =12, ISMSTR = 2, ICPR=2).
I am however getting severe element distortion of foam elements, leading to reduced time step and ultimately resulting in 'Zero or negative volume error'. How can I resolve this. Am I using the correct material model and property? Please help me. This is very very critical for my analysis.
Also, I need help in the interface definition between the soft foam material and rigid aluminum solid part touching it. What parameters to use for defining such a contact?
Thanks.
Answers
-
Hi,
Please refer to below forum post:
0 -
To add,
LAW 33 is for low density foam materials.
Can you try with LAW36 elasto-plastic material instead?
You can use TYPE 7 general contact interface to model contact between two components.
0 -
Hi Prakash,
Thanks for your suggestion. The density of foam I am using is 239 Kg/m3, which is high compared to Polyurethane foams (Density: ~30 Kg/m3) but is much less compared to metals. Are you suggesting that LAW33 is useful only for very low densities like PU materials?
Also, I am not sure if I can use LAW36 to model the foam due to the following differences:
1. The stress-strain behavior in compression (Please find attached) for foam is very different from the mentioned behavior for LAW36.
2. No strain rate effect exhibited by the foam.
I would be grateful if you can suggest the appropriate material model for Al foam, the properties of which are given below:
- Isotropic, open cell foam
- Poisson's ratio = 0
- No strain rate effect
- Density of core material (Al 6061) = 2700 Kg/m3
- Relative density = 8.8%. Therefore, Density of foam = 239 Kg/m3
0 -
Hi Prakash,
I have used the TYPE 7 interface for contact between an Aluminum shell and foam. Since the foam is a soft material, I have defined two interfaces - one with foam=master, Al=slave and another with foam=slave and Al=master. The parameters for the foam are as given below:
For foam=master, Al = Slave:
Stfac = 382
Igap = 0
gapmin=1.0
For foam = slave, Al = master:
Stfac: Default value
Igap=0
gapmin = 1.0
I am getting the ZERO OR NEGATIVE SUB-VOLUME : DELETE 3D-ELEMENT error when I used LAW 36 property for the foam. For compression, should I define the plastic strain as negative in the stress-strain input curve for LAW36? Also, I am using a crushable foam with zero poisson's ratio, therefore true stress = engineering stress. I have defined the engineering stress-plastic strain as the input curve. Is it correct?
Please provide your views on the same.
Thanks and Regards,
Sai
0 -
Hi Sai,
Can you share the model with LAW 33 using the dropbox?
I will try with LAW 70 which is a tabulated visco elastic foam material model.
0