2D, 3D Element type problem in contact analysis
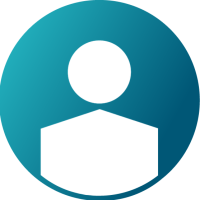

Hello,
I have got a frustrating problem about element type in contract analysis. I have a large aircraft wing model which I want to do analysis on, and I have decided to mesh the rib in 2d mid surface mesh and the Bar in 2d drag mesh (3D Hex). The reason for this is because if I mesh the full wing in 3D tetrahedral mesh in contract , I do not have enough computational power to run the analysis.
The model can be simplifier represent in the photo; a bar going though a hole in the rib.
since I have got a bar going through more than 170 ribs with contract , I cannot use 1d element for the bar. I have also tried to model the bar and ribs in 2d drag (3d hex), but still, the computational time and power is way too without my reach.
so I have sum up with possible solutions but I need someone to correct me if the solution will not work.
1) mesh the bar in 2d drag (3d hex) and the rib in 2d midsurface mesh. then apply contract. * Not sure how to apply contract in mid surface (hole) 2d contract to 3d.
2) mesh the bar and rib in 2d auto mesh (not midsurface, only on surface) then apply 2d contract * the problem for this is I dun think the result will be realistic since the mesh is only on surface
3) scale down the model when input into hypermesh and mesh it in 3d tetrahedral element * but im not sure would it reduce the required computational power, also what do I need to do about the load force when apply to a scale down model.
<?xml version="1.0" encoding="UTF-8"?>
<?xml version="1.0" encoding="UTF-8"?>
please help ...
Many thanks
--BL
Answers
-
Hi yatyeunglam,
The first approach may be helpful for you. You can create a node set with nodes of the holes related to ribs and make contact surfaces on 3D elements of the bar. Using these you can create contacts and run the analysis.
But, I think using 1D elements should be the correct approach in your case.
With contacts it may increase the computation time and the results may not be as expected.
0 -
Altair Forum User said:
Hi yatyeunglam,
The first approach may be helpful for you. You can create a node set with nodes of the holes related to ribs and make contact surfaces on 3D elements of the bar. Using these you can create contacts and run the analysis.
But, I think using 1D elements should be the correct approach in your case.
With contacts it may increase the computation time and the results may not be as expected.
thank you for the advice,
could u explain for me why 1d would work in my case; isn't it 1d only can model compress and tension? with contacts, isn't it the bar would experience shear force from those holes on the ribs? if 1d will work, should I mesh the bar in 1d and extract mid surface for the rib and mesh it in 2d shell mesh ? then apply contact ?
I have try use 3d hex mesh compare to 2d auto mesh and it have a massive different, however I expected the 2d mesh would have larger stress compare to 3d hex mesh, but it is not ....
<?xml version="1.0" encoding="UTF-8"?>
need more advice please
sorry for the long question, appreciate your help
thank you
--BL
0