Explicit Dynamic Analysis for Equivalent Static Load Method
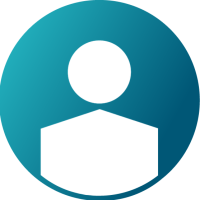

Hello!
I am trying to do Free Shape Optimization of Large Displacement Non-linear Mooney/ODGEN material using EXPDYN and ultimately ELSM for equaivalent static load method as shown using OPTISTRUCT solver. I have setup model for EXPDYN using MAT1 and MATX42 with XSTEP in Sec with TA0=0.0 and DTA = 0.005 and TTERM = 0.05. I have contact surface defines by FRICTION with nu = 0 & 0.3(case-2). But i am getting error of INITIAL PENETRATION. I have seen earlier answers and removed penetration but still error is there. I have tried with TIE contacts as well.(.OUT and .rad file attached), but it is running for hours and no output is generated till. I want to know where i have made wrong. and If you could tell me how ELSM in OPTISTRUCT works?
Could anyone please help me?
Thanks in advanse...!
Find more posts tagged with
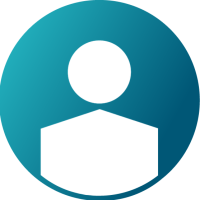

Hi Prakash,
Thanks for your answer. I understand what you have said. But Could you please tell where we can change timestep in OPTISTRUCT as in case of EXPDYN i have only XSTEP LC where i am giving time as described unless NLPARM for Implicit cases. I am confused where should i make change in XSTEP or NLOAD under time option? Will TTERM affect the speed of solution.(i reduced from 1 to 0.005 say).
Will EXPDYN also work with FRICTION CONTACT?
Thanks a lot...!
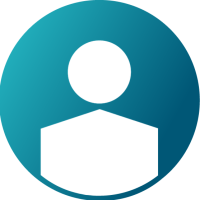

Hi,
Yes EXPDYN will work with friction. It basically runs RADIOSS in background and converts are all cards from OptiStruct to RADIOSS.
Coming to time step control you can do it with XSTEP. I am attaching a sample example picture:
<?xml version="1.0" encoding="UTF-8"?>
Since all parameter fields are not available through GUI you need to edit the deck to input the scale factor and time step.
For more information about the card please refer to OptiStruct help.
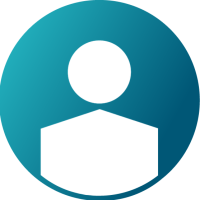

Thanks Prakash...
It's working fast now and got clear idea of time step control perticularly in case of non-linear hyperelastic materials. Thanks for reply.
It has worked now.
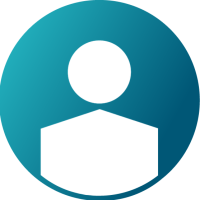

Thank you for the update.
But please make sure that mass error is below 3-5% if you are imposing time step else results may not be good.
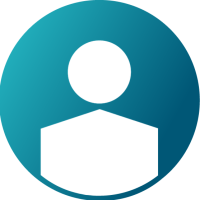

Hello Prakash,
I will make sure mass error is below 3-5%.It worked only with TIE contact, But it's not working when i use frictional conatct with 0.3 mu. I attach output file with error. Could you please check it?
Thanks.
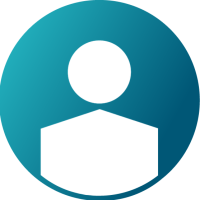

Hi @Dhruvil
Please set Inacti 1 on type20 interface and check if this works. If not try with Inacti 5...
If you still face the problem please share the updated model file.
Please use the dropbox link in my signature to share the model files.
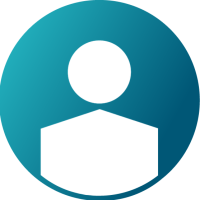

Hello Prakash,
Thanks for your reply. It's working with Inacti 1, but the master surface is penetrating inside the slave surface rather than move\slide with friction. it is not working with Inacti 5 however. I have droped model file, if you could check it? i am also trying to run ELSM in order to perform non-linear large displacement optimization using EXPDYN. I have set control cards for the same, but it is not working.
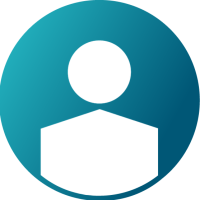

Hi,
Thank you for sharing the files. I will check and updste you soon.
You can also do optimization using RADIOSS
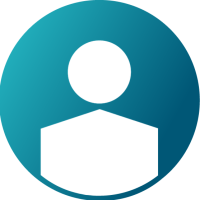

I’m working on a similiar case for my master thesis. I try to optimize the topology of a car door regarding the two crash loadcases „side impact“ and „side pole impact“.
In the first step I tried to simulate the side pole Impact using ESLM in Optrstruct.
I already designed a ridig cylinder with an initial velocity. The results oft the analysis looked quiet realistic, but the optimization runs for days without giving any results, although I set TTERM to 0.005 and changed XSTEP as recommended.
I don’t really know what is the problem… unfortunately I am a really beginner and just started working with HW so I am really thankful for every help I could get (also depending on other warnings / problems, e.g. the huge energy error and „WARNING ID : 312 ** INCOMPATIBLE KINEMATIC CONDITIONS IN MODEL).
I also have problems to define the self impact of the design space – whats the best way to create it?
I sent you the .fem- and the .out-files via dropbox.
Thanks a lot for your help!
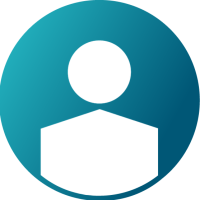

Hi @FBeck
You can model self-impact using CONTACT. The Master set can be blank or set to same as the slave to activate self-contact.
Can you share the entire .out file to check the warning and error messages?
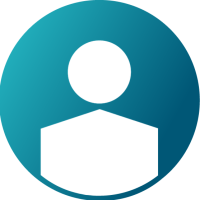

thanks for your Reply!
All files should be in your dropbox I think - aren't they? Nevertheless here is the latest .out-file.
I started optimization on friday afternoon and it is still running... is it because of a mistake or is it normal? Is there a way to Speed up?
I will try to adjust the contact as described, thanks.
I checked the loads and BCs also, but did not find the reason for this WARNING ID : 312 ** INCOMPATIBLE KINEMATIC CONDITIONS IN MODEL.
The rigid cylinder has a initial velocity and there are some Elements fixed as BCs. I don't have any other load steps right now.
Please let me know if you Need any other file to find the Problem.
Thanks again for your help!
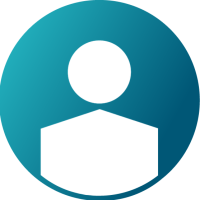

Hi,
thank you for sharing the files.
Let me check and get back to you.
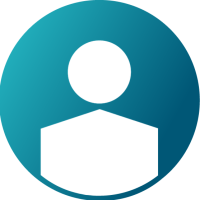

Hi,
is there a reason for using Stress response?
It is not recommended to use the global stress constraint along with a mass/volume constraint. The constrained mass/volume may not allow the stress constraint to be satisfied.
Can you try with compliance with mass or volume fraction instead?
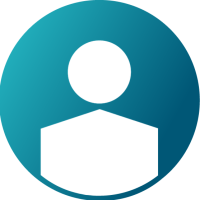

Hi!
Thanks for your quick Response.
The stress constraint was given by my Professor, but for a privious Thesis, in which they only simulate linear static loadcases.
I will talk to him and ask, if it's ok to replace it. I already started another optimization with minimize compliance as object and massfrac as constraint. Hopefully it's gonna work.
The other Thing is, that there's still the other warning shown:
STARTER WARNING:
WARNING ID : 312
** INCOMPATIBLE KINEMATIC CONDITIONS IN MODEL
DESCRIPTION :
48 INCOMPATIBLE KINEMATIC CONDITIONS IN MODEL
Any idea what leads to this one?
There's also still an warning because of the self contact.
It only appeares when starting the optimization. When I only do the Analysis it is not shown.
Attached you'll find my lastest .out-file.
Thanks a lot for your help!
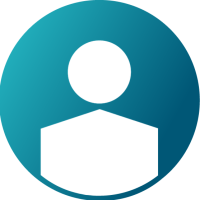

Hi,
I think that warning message is because of the rigid wall.
I have modified the model and waiting for the results. I will update you soon on this.
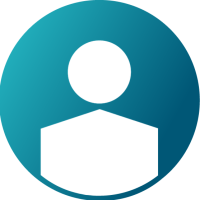

thanks a lot! What could be the effect INCOMPATIBLE KINEMATIC CONDITIONS? Sounds like the results will not be useful?
Good news: After changing the constraints as you recommended (deleted the stress constaint) it ran through!
Finally seeing the first results.
I'm looking Forward to your Feedback.
Best regards.
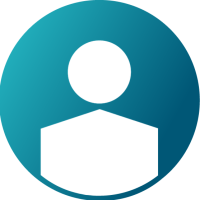

thanks a lot! What could be the effect INCOMPATIBLE KINEMATIC CONDITIONS? Sounds like the results will not be useful?
This could be because you have given a condition that rigid will hit the component and constrain at the same time may arise such a warning which will not harm the results.
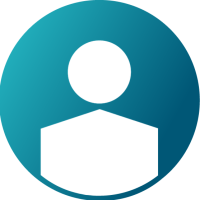

did you get any results from the model I sent you?
I wasn't really satisfied with the optimized structure and tried some changes to get a better one (e.g. reduced massfrac to 0.1, increased MINDIM).
I also fixed some more nodes in SBC to simulate the surroundings of the door, which would also absorb some energy.
All changes leaded to the same Warning:
*** WARNING # 4304
Please note that the final solution is not the converged solution, but
the best feasible solution found during the optimization process.
By refining the time steps for generating the equivalent static loads,
it may help to obtain a solution that is both converged and the best
feasible.
The first iterations look really good, but after it, the structure goes back to the whole design space with lower density.
Do you have any idea how to solve this Problem? Maybe the attached files will help you.
Thanks a lot!
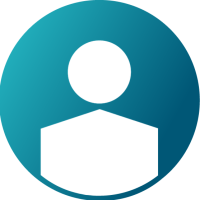

HI @FBeck
I think I shared the modified model with you.
I didn't run the analysis till the end.
Correct, in this case the best design is not from the last iteration and OS repeats the analysis on the best outer loop iteration. The results should also be available in the last generated h3d file.
Can you run the analysis with DOTPRM>>NESLNLGM>>0 and check if that helps?
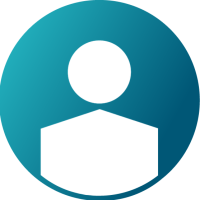

thanks for your quick reply again!
Unfortunately I did not get a modified model so far.. I'd be very interessted in it! Could you send it to me please?
I'm working on an explicit dynamic loadcase, so it might be DOPTPRM >> NESLEXPD instead, right?
Edit:
Just saw that Input of 0 is not allowed - should I try 1 instead? Is the result still realistic with it?
Edit2:
I tried now with NESLEXPD set to 1, 2 und 5 and each time optistruct collapsed. I did no other changes..
Do I have to create an ESLTIME control Card too, to stabilize the optimization?
I uploaded two .fem-files, maybe you can find anything?
Another question: The final goal is to add some static loadcases and also one more dynamic - is it possible to run all of them in one optimization?
I already tried with some static loadcases, but did not get any structure although the optimization ran through. The result is only the whole design space, but without the warning # 4304.
Thanks for your help.
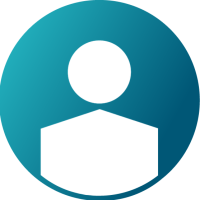

Hi,
In the second file (without warning) the set up is wrong.
You have mass fraction and compliance, but you are using only compliance as objective and constraint. Please check the same and do the changes required.
I need to run the file with warning.
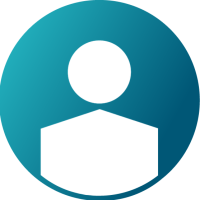

sorry, my mistake! I uploaded the corrected file.
I tried a lot of different Setups, but each time the 'best' structure is at the second Frame und then goes back to the whole design space.
Also the structure of the second Frame has no Connection to the SBC-Areas, which does not really make sense to me.
Do you have any tipps, what to Change to get better results?
I also tried to use minimze mass as object und Maximum static displacement as constraint, but it did not konverge.
Should it be possible theoretically?
Thanks for your help!
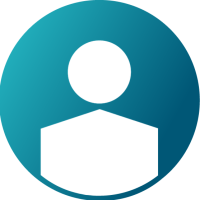

you had already tim to look up the files? Did you find anything?
Do you have any further tipps for me depending on a better structure?
Thanks a lot!!
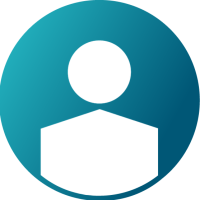

Hi @FBeck
We had a similar question from another user (regarding the warning message)
I am checking with the technical experts on the same.
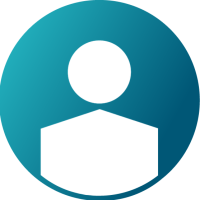

Hi @FBeck Due to known limitations, explicit dynamic analysis and optimization together, it is advisable to run the same using HyperStudy
Hi Dhruvil,
It is common to see the warning even after removing penetration.
Analysis takes too long to run because of time step. You can impose a time step to reduce the run time. You can start with say 5e-7 using DT/NODA/CST in RADIOSS.