CFD Analysis with AcuSolve
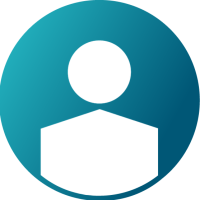

Hello everybody,
my name is Thomas from Germany and I am working on my Bachelor Thesis, which is about the topic CFD, at the moment.
I am at the beginning of my Thesis and at first i want to create a simple model validation.
My topic is about an easy Venturipipe, which gets passes through water.
So there are only two variables, which are important:
The pressure and the velocity, which i estimate with an analytical calculation, too.
The Venturipipe has got a rejuvenation.
And if you think about the Bernoulli´s equation, the velocity gets higher and the pressure goes down near the rejuvenation.
When the fluid leaves the rejuvenation, the values supposed to be retransform back to the input values.
And the model gets unrealistic at this point:
When the fluid leaves the rejuvenation, is does not get slower.
I create the model data with HyperMesh 13.0.
Unfortunately i am not able to find any mistake in the input file, which is computed with AcuSolve.
I hope that someone will hear my problem and is able to solve it. Probably there is only a little mistake, which destroys the complete model in the end.
Thank you for your support in advance!
Best regards,
Thomas
PS: There is a zip.file enclosed, which includes all the important data and some results, too.
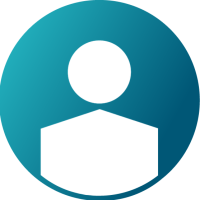

Hey acupro,
thank you for your big support!
It was very helpfully.
Sorry for the wrong topic, I will do it better for next time.
I create a new model today, which results look good at the first view.
But I think there is still some trouble wit the vortices.
Maybe you can take a look at my files once again, they are enclosed.
Have a nice weekend!
//Thomas
If you want to remove the viscous (friction) effects on the walls, you can set Simple BC type = slip instead of wall. I also suggest you use inflow type = average velocity of 1.0 at the inlet instead of velocity.
This yields a pressure difference of 2147 Pa from the inlet to the center of the throat, and average x-velocity of 2.30 m/s at the center of the throat. The values could change somewhat with a more refined mesh.
I would suggest you build a surface at the center of the throat, normal to the flow direction (parallel to inlet/outlet). Do not apply any boundary condition to this surface, but make sure Surface Output is active. Then you can use acuProbe to look at integrated values (pressure, velocity, etc) on this surface.
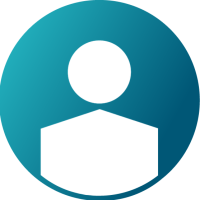

Hey acupro,
my model is running very good now.
I created a better CFD Mesh with a BL growth rate, which is higher than 1.0.
I think this was very important. This value is supposed to be always greater than 1.0 in every model.
Furthermore your advance to set the wall condition to slip was very helpfully.
I built up a another model with wall, which results are not so good compared to the slip results.
I think can be happy with my results, which you can check if you want.
At least I have to say thank you once again!
//Thomas
Please note there is a forum for AcuSolve / VWT where this topc would fit better.
The rapid expansion after the contraction will cause a large separation vortex towards the outer of the venturi. This is also apparent with the negative x-velocity shown in the scale for the results. If you extend your domain very far downstream, you'll see that eventually the vortices 'end' and all the flow is going in the positive x-direction again, with the expected decrease in velocity.
For lower inlet velocity, the separation vortex will be shorter - and longer for higher velocity.
Convergence and stability of solution is better if there is no reverse flow at the outlet - so a longer downstream domain will likely help in that regard as well.