Connection between Shell and Solid elements without penetration
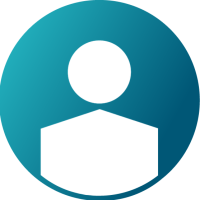

Hi,
I´m a new User of HyperWorks and want to use Optistruct for my graduation thesis. My major task is about topology optimization.
I need some support at the combination of shell and solid elements.
I have to optimize a valve. There are some tubes, which needs a minimum wall thickness (non-design space, for manufacturing). I want to use Shell-elements to represent the non-design space and combine them with solid elements as design-space. I have the (complex) surface of the tubes and I´m not sure how to define the shell elements correctly.
Normally the thickness is defined around the midsurface. I know that I can use the ZOFFS parameter at the definition of an Shell element to adjust that. Because I want to avoid penetration between the shell element and the solid element.
Unfortunately it is not possible to do an offset of the tube´s surface (it´s to complex)). That´s why I want to do some preinvestigation.
Is it possible to connect shell- and solid elements without penetration or a gap based on the tube´s surface?
Answers
-
Altair Forum User said:
I want to use Shell-elements to represent the non-design space and combine them with solid elements as design-space
Hi,
Can you explain what do you mean by combine? If you mean attaching, I think the best way is to use connectors or rigids.
Is it possible to share a picture of geometry?
0 -
Unfortunately I can´t share the detailed geometry with you. But I made a little sketch for you.
I have a tube with an inner surface (in real with komplex shape). Based on this surface the tube needs a non design space (minimal thickness). The residue of the tube is defined as design space for the topology optimization (including the outer surface). That means I can can only use the inner surface of the tube for modeling.
I want to use a shell element for the non design space. I know that I can adujst the thickness of the element and his direction. That means I can use the inner sruface of the tube to define the shell element.
Furthermore the design space contains solid elements. I want to connect the shell elements with the solid element (maybe rigid?). Therefore I can only use the same surface as I used for the shell elements.
I´m afraid about the penetration between the two elements. That´s why I asked how to connect shell- and solid elements without penetration or a gap-based on the same surface?
0 -
What is the thickness of non design and design region?You can try with fully solid tetrahedral elements for non design and design region.
0 -
The thickness of non design is 1mm. The design region is between approximately 3mm to 30-40mm (depents where in the model it is).
I think, if I use solid elements for non design, I would need a very small element size and that means I get a huge model which needs a large computing time. That´s why I want to reduce the number of elements.
0 -
You can try with shell solid approach by having same mesh on both side & connecting them with rigids.
0 -
I tried what you told me, but I think there is something wrong. The behavior is not that, what I expected respectively require.
I prepared two models. The first one (Solid_test.hm) contains only solid elements. The second model (Shell_Model.jpg, Shell_test.hm) contains shell elements, which are connected via RBE2 elements to the underlying solid elements. I set in both models the same boundary conditions. I know that I have a rough mesh in this example, but I think that this mesh can show me the main coherence.
I didn´t got the same displacement in both cases (Displacement_z_Solidtest_1.JPG and Displacement_z_Shelltest.JPG). The displcement of the shell elements is not as high as in the displacement of the solid elements in the other model. That means in my opinion I created a more rigid model, based on the rigid connection.
That is not really what I want. My purpose is to get the same behavior for the model with shell- and sold-elements as for the model with only sold-elements. Is it possible?
<?xml version="1.0" encoding="UTF-8"?>
<?xml version="1.0" encoding="UTF-8"?>
0 -
This is an intended behavior because they both are not same. Also shell elements does not behave same as solid in bending.
0 -
so which model is right?
0 -
Hi Ank,
Adding extra rigids will add extra stiffness to the model which may not give right results.
I hope this helps to pic the right model
/emoticons/default_smile.png' srcset='/emoticons/smile@2x.png 2x' title=':)' width='20'>
0