Connection between Shell and Solid elements without penetration
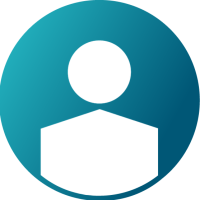

Hi,
I´m a new User of HyperWorks and want to use Optistruct for my graduation thesis. My major task is about topology optimization.
I need some support at the combination of shell and solid elements.
I have to optimize a valve. There are some tubes, which needs a minimum wall thickness (non-design space, for manufacturing). I want to use Shell-elements to represent the non-design space and combine them with solid elements as design-space. I have the (complex) surface of the tubes and I´m not sure how to define the shell elements correctly.
Normally the thickness is defined around the midsurface. I know that I can use the ZOFFS parameter at the definition of an Shell element to adjust that. Because I want to avoid penetration between the shell element and the solid element.
Unfortunately it is not possible to do an offset of the tube´s surface (it´s to complex)). That´s why I want to do some preinvestigation.
Is it possible to connect shell- and solid elements without penetration or a gap based on the tube´s surface?