Connection between Shell and Solid elements without penetration
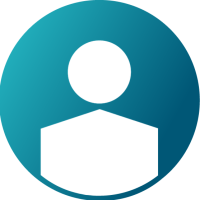

Hi,
I´m a new User of HyperWorks and want to use Optistruct for my graduation thesis. My major task is about topology optimization.
I need some support at the combination of shell and solid elements.
I have to optimize a valve. There are some tubes, which needs a minimum wall thickness (non-design space, for manufacturing). I want to use Shell-elements to represent the non-design space and combine them with solid elements as design-space. I have the (complex) surface of the tubes and I´m not sure how to define the shell elements correctly.
Normally the thickness is defined around the midsurface. I know that I can use the ZOFFS parameter at the definition of an Shell element to adjust that. Because I want to avoid penetration between the shell element and the solid element.
Unfortunately it is not possible to do an offset of the tube´s surface (it´s to complex)). That´s why I want to do some preinvestigation.
Is it possible to connect shell- and solid elements without penetration or a gap based on the tube´s surface?
Find more posts tagged with
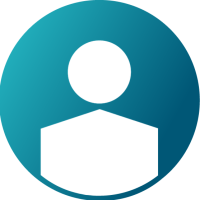

Unfortunately I can´t share the detailed geometry with you. But I made a little sketch for you.
I have a tube with an inner surface (in real with komplex shape). Based on this surface the tube needs a non design space (minimal thickness). The residue of the tube is defined as design space for the topology optimization (including the outer surface). That means I can can only use the inner surface of the tube for modeling.
I want to use a shell element for the non design space. I know that I can adujst the thickness of the element and his direction. That means I can use the inner sruface of the tube to define the shell element.
Furthermore the design space contains solid elements. I want to connect the shell elements with the solid element (maybe rigid?). Therefore I can only use the same surface as I used for the shell elements.
I´m afraid about the penetration between the two elements. That´s why I asked how to connect shell- and solid elements without penetration or a gap-based on the same surface?
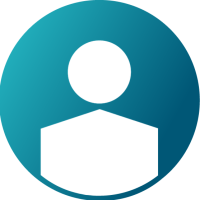
What is the thickness of non design and design region?You can try with fully solid tetrahedral elements for non design and design region.
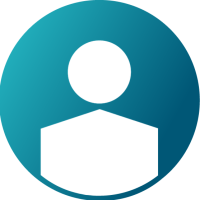

The thickness of non design is 1mm. The design region is between approximately 3mm to 30-40mm (depents where in the model it is).
I think, if I use solid elements for non design, I would need a very small element size and that means I get a huge model which needs a large computing time. That´s why I want to reduce the number of elements.
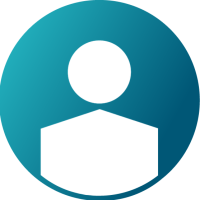
You can try with shell solid approach by having same mesh on both side & connecting them with rigids.
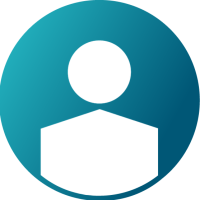

I tried what you told me, but I think there is something wrong. The behavior is not that, what I expected respectively require.
I prepared two models. The first one (Solid_test.hm) contains only solid elements. The second model (Shell_Model.jpg, Shell_test.hm) contains shell elements, which are connected via RBE2 elements to the underlying solid elements. I set in both models the same boundary conditions. I know that I have a rough mesh in this example, but I think that this mesh can show me the main coherence.
I didn´t got the same displacement in both cases (Displacement_z_Solidtest_1.JPG and Displacement_z_Shelltest.JPG). The displcement of the shell elements is not as high as in the displacement of the solid elements in the other model. That means in my opinion I created a more rigid model, based on the rigid connection.
That is not really what I want. My purpose is to get the same behavior for the model with shell- and sold-elements as for the model with only sold-elements. Is it possible?
<?xml version="1.0" encoding="UTF-8"?>
<?xml version="1.0" encoding="UTF-8"?>
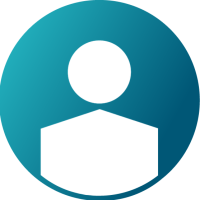

This is an intended behavior because they both are not same. Also shell elements does not behave same as solid in bending.
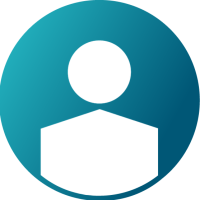

Hi Ank,
Adding extra rigids will add extra stiffness to the model which may not give right results.
I hope this helps to pic the right model /emoticons/default_smile.png' srcset='/emoticons/smile@2x.png 2x' title=':)' width='20'>
Hi,
Can you explain what do you mean by combine? If you mean attaching, I think the best way is to use connectors or rigids.
Is it possible to share a picture of geometry?