Linear static analysis of plastic injection mold assembley
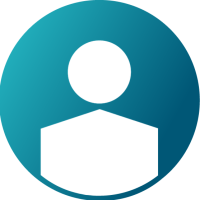

Hi Rahul
<?xml version="1.0" encoding="UTF-8"?>
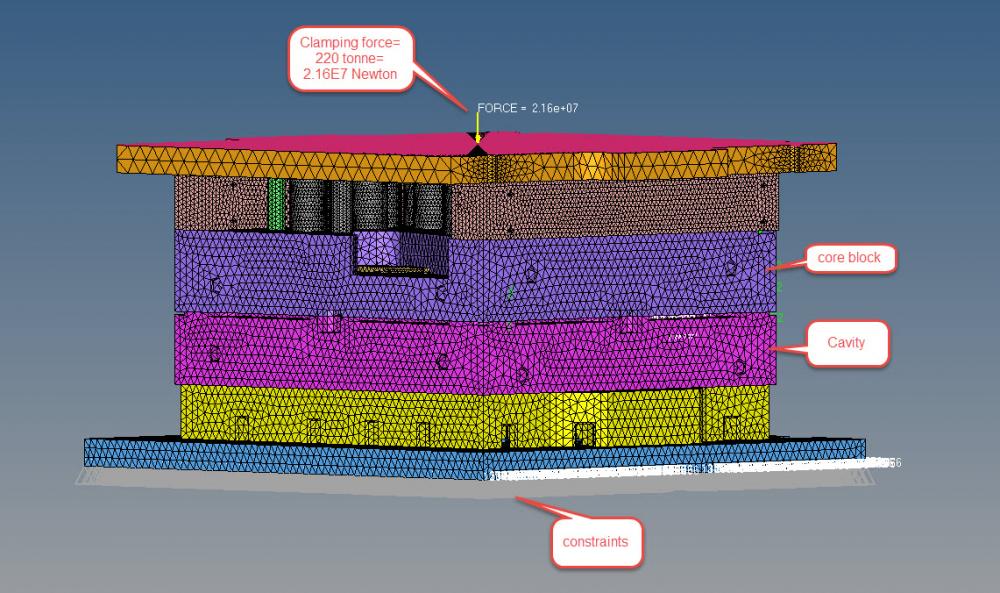
<?xml version="1.0" encoding="UTF-8"?>
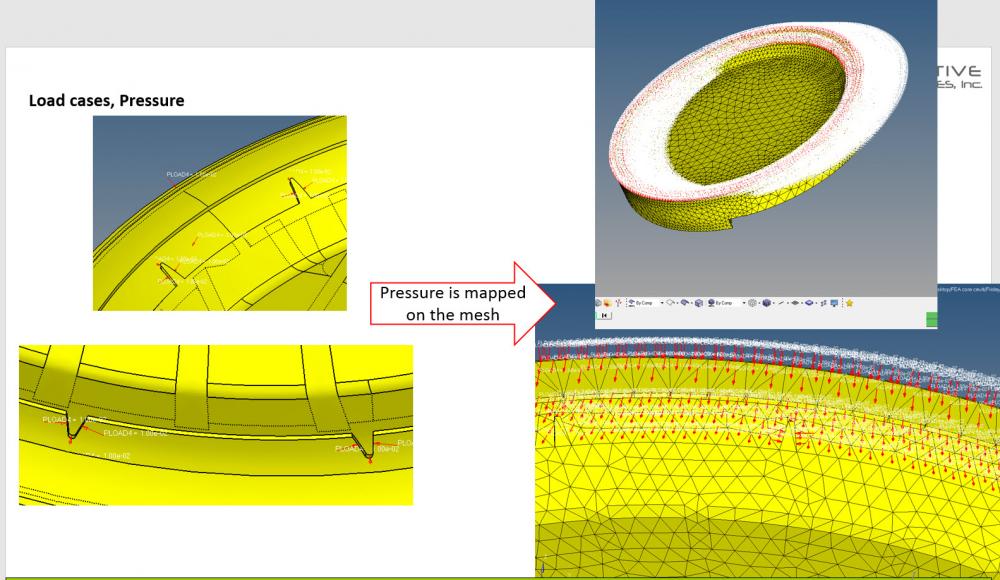
I don't know understand why I get this result. I have used bolt connection, RBE2 and also FREEZE contact to define connection between parts.
I sent you the model via your Dropbox link. I appreciate if you can spend some time and check my model and let me know what is the problem and why the maximum displacement I got is much more than the reality.Thanks a lot.
Answers
-
-
just downloaded file.Will check and update you.
0 -
what is overall weight of entire model?
0 -
Thanks alot
I have to contact our customer and ask that
0 -
It should be around 8336 kg
0 -
Is that realistic?I mean 8336 kg is too much.
0 -
Altair Forum User said:
It should be around 8336 kg
I think the weight should be fine for a injection mold machine.
Can you share the entire .out file here, please?
0 -
When I post process output in Hyperview i see part name Origin ins1 deform more.See attached screenshot.
When I try to check contact between cavity block & origin ins1 in Hypermesh while reviewing contact i found contact established in some other region.
See attached screenshot for same.Please update contact and run again.I believe that was causing unexpected max displacement.
<?xml version="1.0" encoding="UTF-8"?>
0 -
Hi guys
Thank you so much for your great help. You are right I missed that contact surface. I am going to create contact there and hopefully that would work.
0 -
I fixed the connections and now I have more realistic results
but there are still some issues. My model is almost symmetric but I don't understand why displacement distribution is not symmetric
<?xml version="1.0" encoding="UTF-8"?>
The second issue is that in the core block there are two regions that have lower thickness so it is expected that cavity pressure deforms those two regions more but the results are vice versa
<?xml version="1.0" encoding="UTF-8"?>
it is expected to have distribution of displacement something like the follwoing pic
In real case flashing (leakage of molten plastic) happens at these two domains and our customer thinks it is because the thickness is lower in these two region, the structure is weaker and deformation is more. but My last result shows opposite I appreciate if you can check my model and let me know the reason. I will upload the file via your drop box link.
0 -
Hi,
Is the load symmetric?
0 -
yes the load is symmetric too
0 -
Only Manifold plate is not symmetric
0 -
that could be one of the reasons.
what type of contacts have you used?
0 -
I have used Freeze contact every where since I am doing linear static analysis
0 -
Hi
I was wondering if you had time to check my model. I am waiting for your reply
0 -
Hi Bita,
I don't have access to your model. But maybe you can check your self.
Partition the components in to 4 symmetric parts and check their mass.
0 -
I dont feel you entire model is symmetric& toget symmetric results it is recommended to have symmetric mesh.For second query i will check and update you.
0 -
-
The ejection pin are cylinder pin which goes inside clamp plate' holes.They are used for alignment only.
0 -
Is this displacement contour correct for the rigid element? It is rigid but it has moved unevenly
0