*** WARNING # 312 In static load case 1, the compliance is negative or large 4.04523e+010. Optimization/buckling analysis cannot be performed. due to possible rigid body mode. (Running minimum-core solution)
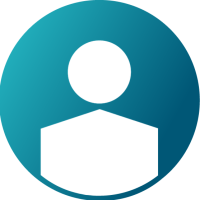

Hi guys
I have the following assembly and I want to do a linear static analysis. I have used both RBE2 and Freeze contact to connect the components in the assembly
<?xml version="1.0" encoding="UTF-8"?>
The following pics shows my RBE2 connections and I have defined FREEZE contact every other places where components touching each other
<?xml version="1.0" encoding="UTF-8"?>
<?xml version="1.0" encoding="UTF-8"?>
I can not get proper result the components fly in Hyperview. Here is the warning I have in my .out file
*** WARNING # 312
In static load case 1, the compliance is negative or large 4.04523e+010.
Optimization/buckling analysis cannot be performed.
due to possible rigid body mode.
(Running minimum-core solution)
I don't know where my mistake is
I appreciate your help
Answers
-
for such assembly i would recommend you to run free free run or modal analysis. which would help to know about connectivity.
I believe we have many post in forum with error 312.just search with error 312 or compliance is negative.. you would get similar topic on forum. please refer same and try.
0 -
Would you please explain more regarding why it is necessary to do modal analysis.
0 -
Free free run is kind of check for connectivity.In free free run dont apply any constraint just run with Eigrl card with some nd(no of modes) value. so if you get first six mode as rigid then that means your parts are properly connected. if you get first 12 as rigid mode then that means one part is not properly connected in assembly and you would find that part as flying and rigidly moving with no deformation.If you get first 18 modes as rigid then that means two parts are not connected.
same set up if you run with constraint it would be called as modal analysis and output would be frequency and mode shape.
0 -
Thanks a lot for your help Rahul
0