Contact
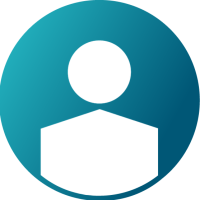

Hi,
I am trying to simulate contact for performing frontal crash analysis of a chassis having a tank. I have a tank which is wrapped by two brackets and supported by rubber. This bracket is welded to a chassis. I need to create contact for the following-
1) Between tank and bracket.
2) Between rubber and bracket.
3) Between rubber and tank.
It is attached to chassis as follows-
I know that I need to create Interface. Please tell me for each case which Type interface should be used and which should be selected as master and slave?
Thank you,
Datta
Answers
-
Hi Datta,
As a general remark Type 2 interface is a tied interface that kinematically connects a set of slave nodes to a master surface.and thus it will not allow relative motion between the parts. If user expects a relative or sliding motion between parts Type 7 interface should be used, which is a multi-usage impact interface, modeling contact between a master surface and a group of slave nodes.
And regarding selecting the master and slave surface, the coarser the mesh the stiffer the structure will be, provided the material and structural properties are same. Hence, the Master is typically meshed coarser so that the Slave does not penetrate into master. Choose less deformable or high stiffer structure as master (coarse mesh) and less stiff (fine mesh) as slave.
Based on the information I recommend you to try with Type 2 interface for the first case and other cases you can try with Type 7.
I suggest you to go through Example 14 - Truck with Flexible Body which will give you a fair idea on modeling.
0 -
Hi George,
Thank you for answering. I wanted to know how the load transfer works in the case of Type 2 and Type 7 interface. I could not find in the manual. In both the interfaces does the load transfer takes place from the slave surface to the master surface or the other way ?
Thanks,
Datta
0 -
Hi Datta,
The load transfer typically happens based on the simulation, that is based on the loading conditions and boundary conditions assigned by the user. In RADIOSS an interface is created by defining the master segment and slave set. The master segment can be parts, elements, contact surface, node sets and similarly for slave the selection can be parts and node sets. Once these master slave sets are identified the algorithm will check these locations for potential penetration of a slave node through a master segment, and this check is done in every time step.
0