initial velocity for rigid body
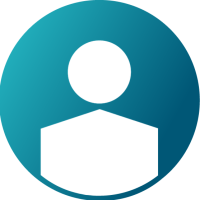

Hello !
I want to crush a rigid body with initial velocity into a wall but when I compute, there is no motion.
Is it the good way or the proedure is different ?
Should I use specific properties ?
Thank for your answer !
Answers
-
Hi,
Please ensure that the master node of the rigid body is also selected along with other nodes of the component while assigning the initial velocity and try running the analysis.
I recommend you to go through Modeling and Analysis of Honeycomb Impact Attenuator tutorial which is similar to your case. You can access the tutorial and models at http://www.altairuniversity.com/wp-content/uploads/2016/11/Crash_Box_1.pdf
0 -
Indeed, all the nodes of my rigid body are included in the initial velocity.
I think I have done all the tasks indicated on your tutorial but it was as if i have boundary conditions on my rigid body.
And my time step is very low ...0 -
Hi,
Can you please share your model file.
0 -
You can find my attached model.
Thank for your attention
0 -
Hi,
Please try with the file (model_0000.rad) attached.
Regarding time step, find what is causing for this time step drop.
First, check which object is responsible for the low time step in the listing file (Runname_0001.out) of RADIOSS Engine. It can be an element, a node or an interface.
•For an element, check the related material (especially its Young modulus and density in case of an elastic-plastic material; and its viscosity in case of a visco-elastic material). There must not be an error in the units system that this data is given in.
Check the size of the element, since elemental length is proportional to time step.
•For a node, check the characteristics of connected elements. If the node is on the master side or the slave side of an interface, this interface must be verified.
•For an interface, the gap of the interface must be verified if some failure happens on the master or the slave side of the interface.
Once this is cleared you can run the simulation without time step being dropped.
User can also impose a time step for the run using the keyword /DT/NODA/CST in the engine file. I suggest you to refer the video below for timestep control in Radioss Explicit: https://altair-2.wistia.com/medias/o0bfml9ah5
0