Radioss 140
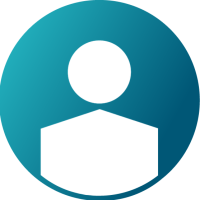

Hi all,
How unit system is to be followed in Radioss 140. Density, Elastic modulus , force , time etc.,
I follwed Density in tonne/mm3, Elastic modulus in MPa, Force in N & time in ms (milli second)
Output will be in MPa?
What if Density in kg/m3, Elastic modulus in Pa, Force in N & time in s (second)
Kindly help us in solving this propblem
Answers
-
Hi Naveen,
There is no fixed unit system in RADIOSS. User has to follow a unit consistency.
If you are following Tonnes and mm, time has to be in seconds. In that case stress output will be in MPa.
For kg,m and second, output will be in Pa.
Please find the normal unit consistency followed across industries with example values.
Hope this helps.
0 -
Hi johnson,
Thank you for your clarification. It will be very useful
Further adding to my query, How units to be followed for material selection in Radioss 140
Find the attached image for M42_OGDEN material where units were shown in kg/m3 ,pa & s
I followed tonn, mm & s for steel material definiton.
For M42_OGDEN Should I convert density in to tonn/mm3, M1,M2 etc., in MPa to follow unifrom unit system
Kindly clarify
0 -
Hi Naveen,
Yeah, convert to tonnes,mm,sec units and follow the same consistency throughout the model.
0 -
Hi johnson,
Thank you for the reply
Tried following same units
Tried with 2d elements, Getting error as 'Error in input consistency'
'Quad are not compatible with N2D3D=0'
Kindly clarify
0 -
Hi Naveen,
In Analysis>>Control Cards, disable the Analysis Flags card and try running again.
0 -
Hi Johnson,
Analysis flags not defined.
Attached radioss files for your reference
Refer the file and clarify my query pls
0 -
Hi Naveen,
From 2D panel>elem types, select the elements and update for 2D&3D elements option and try running.
0 -
Hi Johnson,
Tried with element type to quad4N. radioss file which i sent you is with quad4N element type
Error i am getting is
Error in input consistency'
'Quad are not compatible with N2D3D=0'
Kindly assist in solving this issue
0 -
Hi Naveen,
The updated files has been sent.
0 -
Hi johnson,
Thanks for the clarification
When giving pressure load in block 140 getting error as 'rupture of shell element'
How pressure load can be given in block 140 & how the error can be avoided?
0 -
Hi Naveen,
Create a surface set or contact surface and apply the pressure load over the same with a Pressure v/s Time function.
Is there any rupture/failure criteria in the model?.If not, check the interface and also check for any penetrations.
Please use the recommended contact parameters as below for interface Type 7, if you have Type 7 interface in your model.
Istf=4
Igap=2
Fscale_Gap=0.8
INACTI=6
Gap_min=
Fric = 0.1
Iform=2
0 -
Hi Mr.Johnson,
I have not defined any interface. I created equivalence between nodes.
Gave pressure by creating contact surface. Getting elenet rupture though sigma max is set @ 500 MPa.
why this occurs?
0 -
Hi Naveen,
Did you give any failure plastic strain (Eps_max) in the material card?.
0 -
-
Hi Naveen,
Can you share the model file and the out files (_0000.rad,_0000.out and _0001.out files).
0 -
Hi Mr.Johnson,
Sure file has been shared.
Control volume defined to introduce inflation pressure effect (Control volume created as 'SURF')
Pressure load given by creating contact surface
Getting error as 'Rupture of shell element'
0 -
Hi Naveen,
Received the model. For /MONVOL/GAS the volume must be closed but starter gives a warning EXTERNAL SURFACE IS NOT CLOSED. Please recheck the same.
The error is happening because of the extreme deformation happening in the model which leads to rupture of elements. Please check the material values for the tyre. I have just modified them and tried running. The same files has been sent to you.
0 -
Hi Johnson,
Thanks for clarification.
Will carry out analysis as per your suggestion and will revertt
0 -
Hi Johnson,
Thanks for the clarification provided
How imposed displacement can be given in RADIOSS
Is there any tutorial/example for giving imposed displacement
0 -
Hi Naveen,
From BCs Manager in Utility Menu you can apply the imposed load. A time vs displacement function has to provided.
Please go through https://altairuniversity.com/learning-library/7-guidelines-to-apply-quasi-static-load-in-explicit-simulation/ which provides the guidelines for applying the imposed loads in RADIOSS.
Please go through Example 16 in our Help Menu which is a similar case and the same files are attached along for your reference.
Hope this helps.
0 -
Hi Naveen,
The query has been moved to OptiStruct sub forum where our OptiStruct experts will help you in solving the same.
You can follow up the query at http://forum.altairhyperworks.com/index.php?/topic/21534-tyre-assembly-analysis/
0 -
Hi Mr.Johnson,
In the attached image, floor mass of 6ton is applied on the tire
Spring properties were given for tire, stiffness value calculated from load vs displacement curve
Imposed displacement of 212 mm applied to the floor
Analysis is done for no inflation. Stress is not being transformed from tire to disc
same done for tire inflated condition getting stress distribution from tire to rim (ex - 4barsi inflation pressure)
Is any changed required in tire stiffness property?
Floor to tyre contact is given type 7 contact
Should any change to be done for floor - tyre contact stiffness
Regards,
Naveen
0 -
Hi Naveen,
Altair Forum User said:Spring properties were given for tire,
Did you assign spring property to the tyre?. Can you be more clear on this?.
Ensure there is proper connectivity between the tyre and the disc. Run for a bit longer time and review whether stresses are developing on the disc.
For contact, follow the recommended parameters.
0