Topology optimization trivial result with active stamp draw direction constraint
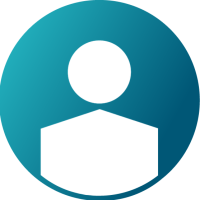

Hi!
I'm currently trying to show OptiStruct's capabilities regarding manufacturing constraints for a thesis.
Unfortunately, activating the 'draw direction'-subfeature 'stamp' results in trivial solutions (see attachment) that either fail or stop after 80 iterations. I already tried expanding the load cases and tuning the volumefraction constraint.
I don't want to misrepresent the feature, but in most of the tutorials this one feature has been left out. The only example I found is in the attachments. Is there any more information describing the tool's way of working and recommendations for the optimization setup? Or is it a 'work in progress'-feature like MAXIMUM MEMBER SIZE is?
I also added my own project as a .hm.
Thanks in advance and sincerely
Yussef Bassti
<?xml version="1.0" encoding="UTF-8"?>
Find more posts tagged with
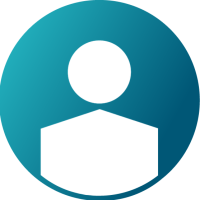

Have been through this section of OptiStruct help?
Draw Direction Constraints for Topology Optimization
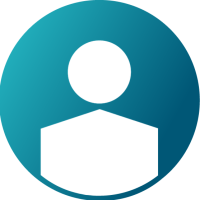

Thank you for taking the time, @Prakash Pagadala!
Yes, I've looked into that. That's why I adapted the there proposed optimization problem with volfrac constraint and multiple loadsteps minimizing weighted compliances. Sadly, with the same outcome.
Are there any examples other than the one in the help section you've mentioned (automotive bracket)?
Thanks
Sincerely
Yussef Bassti
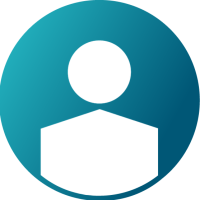

Hi,
I need to check if there are any examples. But if you can post your requirement, we will see how we can help you model accordingly.
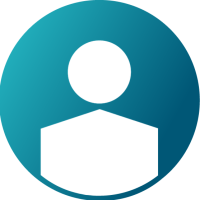

Hi and thanks again, it is heavily appreciated, @Prakash Pagadala!
There is no certain requirement for my model. I want to show the capabilities of the tool, so I'm trying to force the result into something less planar. But it seems as if the tool's progression is dependant upon the given design space.
I'm using a simple minimize total compliance problem restricted to 25 % volume fraction with 5 or 10 stamp thickness. I've been changing loads, directions, volume fraction, stamp thickness, hole and no hole constraint and changed from tetra to hexa mesh with the same outcome.
Thanks and regards
Yussef Bassti
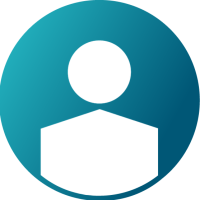

This is something needs some attention. Maybe by trying with different design and non-design areas, different manufacturing constraints, etc...
Hi @Yussef Bassti
I am loolong into this issue and will get back to you soon.