ESLM: Strain Constraints
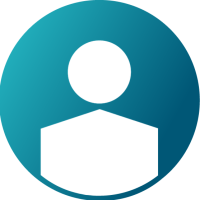

When I impose ply strain responses, which can be derived directly from displacement ESLs of the same nonlinear loadcase, as design constraints for a nonlinear loadcase, there are differences between strain response values outputted in .out file and strain contour in .h3d file.
In theory, design responses from these two files should match each other but strain values in .out file (optimization values) tend to be larger than what is plotted in .h3d file (analysis values).
What could be the reason behind this? Any suggestion on how I can use .h3d strain output as design responses?
Answers
-
Hi,
The reason is that for non linear optimization we have an outer loop of Non linear analysis run in Radioss and an inner loop of ESLM based Optimization in Optistruct. The Equivalent Static Loads are generated from a reduced set of peak loads from the loading curve of the non linear analysis run. And hence after the final optimization run which showed a converged response value of let say 2.0, and a subsequent non linear analysis in Radioss it shows say1.88. So the results will never match, though we are looking at ways to get a workaround to this issue in the future release.
Regards
Rahul R
0 -
Hi,
Small deviation because of different solvers is acceptable, but the difference I am pointing out is more than 100% !
For instance, in the attached files, we look at strain response of the first outer loop iteration (initial design, no optimization yet):
NORMAL STRAIN XX, PLY 1, Time=1.0s or equivalent static Subcase 90008
Element ID 40477: RADIOSS value=-6.344E-04, DRESP value=-1.628E-03, Difference=157%
Element ID 40245: RADIOSS value=-6.388E-04, DRESP value=-1.587E-03, Difference=148%
Element ID 36632: RADIOSS value=-6.276E-04, DRESP value=-1.465E-03, Difference=133%
Regards,
0 -
Could you please forward this query to the development department?
Kind regards,
Tanut
0 -
Hi,
Since there is no ESL correction factor applied to composite strains, the strains from non-linear and static runs will not match.
This can be implemented in the near future.
0 -
Thank you! But why do we need the correction factor if we are still in the linear stress-strain relation? ESLs based on displacement should produce strains very close to the ones from (geometrical) nonlinear analysis with linear material property.
0