Radioss solving time increasing
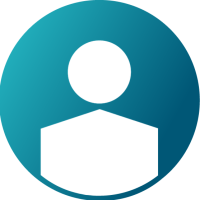

I have used a Type 7 contact in impact analysis as given in the hyperworks pipe-impact analysis, the example problem has run perfectly, but when I was running analysis for another model the solution time keeps on increasing, I have given volume tetramesh for model and the boundary conditions and control cards are same as the one in tutorial. User-Profile: Radioss Block 120.
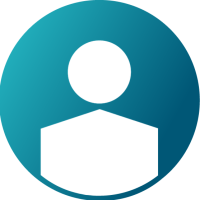

Hi George,
Thanks for your reply, i have gone through your suggestions but i was unable to solve the problem, could you look into the attached output file and suggest a way to solve it.
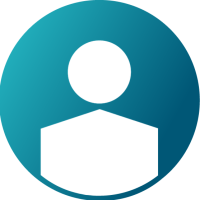

Hello Kamal,
NEGATIVE VOLUME is terminating the run. This NEGATIVE VOLUME error happens when solid elements are very deformed and their characteristic length goes to 0. For large strain formulation the time step of an element goes to 0 when the element is compressed. In RADIOSS Starter input file (Runname_0000.rad), use Ismstr =2 in the solid property and in RADIOSS Engine file (Runname_0001.rad) use the option/DT/BRICK/CST which will set the time step value Tmin at which the solid elements will switch to small strain.This means that the solid elements using Ismstr =2 will use large strain formulation while their time step remains greater than Tmin, and will then switch to small strain formulation.
(/DT/BRICK/CST option is used to control the time step of the analysis. The time step becomes constant after reaching Tmin specified by the user ).
Moreover, please check the interface in the model.
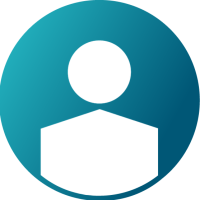

Hi George,
Thanks for the suggestions, I have applied them but the problem is still persisting, could you please look in to the hypermesh file i have attached and tell where the problem.
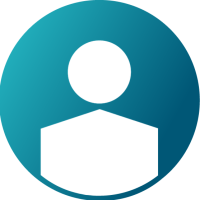

Hi Kamal,
Please try with the attached files. Material parameters were updated. Please cross check.
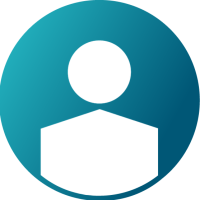

Hi George,
Thank you very much, the problem was rectified but the solution time is showing about 50000 seconds, my system configuration is Intel i3 processor, 8GB ram could you tell me how much time it has taken for you to solve.
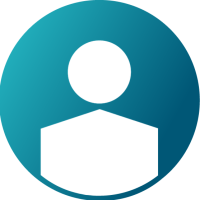

Hi Kamal,
I didn't complete the run in my system. I was only cross checking for any errors during the run. You can try with a better time step (/DT/NODA/CST) which will reduce the run time. But continuously monitor the mass error in _0001.out file.
Hello Kamal,
It is due to the time step drop the solution time keeps on increasing. Find what is causing for this time step drop.
First, check which object is responsible for the low time step in the listing file (Runname_nnnn.out) of RADIOSS Engine.
It can be an element, a node or an interface.
•For an element, check the related material (especially its Young modulus and density in case of an elastic-plastic material; and its viscosity in case of a visco-elastic material). There must not be an error in the units system that this data is given in.
Check the size of the element, since elemental length is proportional to time step.
•For a node, check the characteristics of connected elements. If the node is on the master side or the slave side of an interface, this interface must be verified.
•For an interface, the gap of the interface must be verified if some failure happens on the master or the slave side of the interface.
Once this is cleared you can run the simulation without time step being dropped.
Please refer the video below for timestep in Radioss Explicit:
https://altair-2.wistia.com/medias/o0bfml9ah5