Surfaces interaction
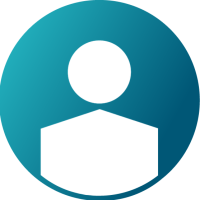

Hello everyone,
I have a problem with this simple landing gear. The shaft (orange) is fixed to the fuselage. The torsion springs (green) are inserted in the shaft end engage the two arms (yellow) that are connected to the wheel. At the same time the arms are bonded to the shaft.
<?xml version="1.0" encoding="UTF-8"?>
<?xml version="1.0" encoding="UTF-8"?>
<?xml version="1.0" encoding="UTF-8"?>
I need to create an interaction between the follow surfaces:
1 Spring tail/shaft (slip)
2 Spring tail/arm (slip)
3 Arm/shaft (slip)
4 Inner part of the spiral's spring/shaft (avoid compenetration)
I tried to create this interactions but i failed. I had an 'accetable' result only for 1 and 2 without slide but with freeze interaction.
Can you help me with this problem?
Thanks.
Answers
-
Hi giannibruno,
Can you share your model please? you can use File transfer link given below.
https://ftin.india.altair.com:8443/filedrop/~osKE8Q
Thank you
0 -
Hi giannibruno,
Please can you make it clear, first contact whether you want between spring and the shaft or spring tail and the shaft?
Thank you
0 -
The first contact is between the spring tail that goes in the shaft' hole.
0 -
0
-
I tried again creating the contacts like in you video. When i run Optistruct there are strange results with stresses.
It seems as if the contact blocks the two surfaces together.
Can you see this video and explain me why i have these results?
Thank you so much for you help.
0 -
Hi giannibruno,
Sorry for late reply.
Please can you share your model file with the loads? I'm not able to understand properly through the video.
You can use FT link below.
https://ftin.india.altair.com:8443/filedrop/~osKE8Q
Thank you
0 -
Hi giannibruno,
Please try to interchange the Master and Slave surfaces of the contact and check the results. (*Note: Slave surfaces takes loads from master surfaces)
Thank you
0 -
Hi @Premanand Suryavanshi. Sorry for my late reply.
I tried all the permutation of Master and Slave for each group (also considering the load flow) but there is no way for acceptable results.
For all the groups there aren't big differences if i switch master and slave. But the problem is for both contacts arm-shaft.
When i set the arm as Master and the shaft as Slave (should be the right load flow) i have the same results of the video (strange stress distribution)
If i swicth Master and Slave everything explodes.
There is a way to solve this problem?
Thank you
0 -
Can you please share the latest model.
Thank you
0 -
I shared the model with the usual link.
As always thank you for your help.
0 -
Hi giannibruno,
Please check these results. Is this is the result you are looking for?
<?xml version="1.0" encoding="UTF-8"?>
<?xml version="1.0" encoding="UTF-8"?>
<?xml version="1.0" encoding="UTF-8"?>
Thank you
0 -
Well ... I think that this stresses are more realistic than the previous ones.
However the springs should be stressed but seems that aren't stressed .
There are also areas with strange stress concentration on the shaft( but this is a minor problem).
Is really better than the mine but I don't think that this is the true stress distribution due the problem on the springs.
What was the problem with my model?
Thank you so much.
0 -
Hi
I have your same results now in my model but there is still the problem of stresses and load flow.
The problem is that the spring doesn't work properly. Seems that the two arms and the shaft are welded together.
The load flow has to go through the springs and not completely through the arms.
Thank you
0 -
Hi giannibruno,
It is because the spring is not making proper contact with any of the components. When you examine the model closely, you'll find distinct gap between the spring surface and other components. I think you need increase the diameter of the spring and try again.
Thank you
0 -
I will try to increase the diameter of the shaft because i can't change the spring.
Is it anyway necessary to add a contact surface between the inner part of the spring and the shaft with the new diameter?
I will try in this way but i have some doubt about the spring. Because this is a torsion spring that need to works following the same winding direction of the helix. When i load the spring in this way the inner diameter decreases a bit. So the spring can't work properly if i remove the gap between the spring and the shaft,.
Maybe it could be better if the shaft's diameter is smaller than the spring's one and the spring can slides on the shaft's surface in only one point.
Anyway now i will try to removing the gap between the spring and the shaft and see if the results are better.
Thank you
0 -
0
-
In this days i tried some solutions but all with the same results.
I can't apply your solution (Increase the diameter of the springs)
I tryed to increase the diameter of the shaft but there is a problem because the shaft's axis isn't the same of the spring. But I will try to change the axis of the shaft part that is inside the spring and increase its diameter in order to create a contact surface between the shaft and the inner part of the spring. I will update you about this.
I tryed also other configurations but without good results.
I will try changing the CAD (with one point of contact between the shaft and the inner part of the spring) and remesh. In this way what kind of contact will I have to add between shaft and the inner part of the spring?
Thank you.
0 -
Altair Forum User said:
I tryed to increase the diameter of the shaft but there is a problem because the shaft's axis isn't the same of the spring. But I will try to change the axis of the shaft part that is inside the spring and increase its diameter in order to create a contact surface between the shaft and the inner part of the spring. I will update you about this.
I think you need to decrease the inner dia of the shaft (middle part) in order to make contact with the spring.
Thank you
0 -
-
I tried to reduce the two diameters but i have the same results.
Is it possible that the landing gear still has some DOF that i didn't block?
I tought that there isn't a constraint in the x direction for the springs and the two arms. I tried to add this contsraints but still the same results.
Do you have other advice for my problem?
Thank you
0 -
Hi giannibruno,
After reducing the dia did you create contact surface between them? Please can you share the latest model.
Thank you
0 -
Yes of course. I created the slide contact for both diameters.
I shared the latest model on the usual filedrop link.
Thank you
0 -
Hi giannibruno,
I think we need to add some constraint to the spring. Because, when you animate the motion, you can see that spring is not doing actual work (Resisting work), it is simply behaving as a part of Arm and moving along with it. I'm trying to constraint the spring in different ways and checking the results. I'll share my findings once i'm done. Until then, please can you also try it.
Thank you
0 -
HI @giannibruno
Since you have slide contact, please use non-linear quasi-static analysis instead of linear static analysis.
0 -
I have never done this analysis so I don't know all the settings of non-linear quasi-static analysis.
I created a loadstep with card image NLPARM and I performed the analysis.
I have different results but not the ones I expect. The springs are still discharged.
I tried to follow tutorials about this but i didn't understend what i have to do. What else should I add for this type of analysis?Thank you.
0 -
OK,
I have the file with, let me check and get back to you.
0 -
Thank you for your help.
I checked your model and i started the analysis.
The stresses are different and more realistic but there is a problem with the displacement. The two arms increase in dimension with no reason. This souldn't happen.
Is there a way to solve this problem?
Thank you
0 -
HI,
Can you please share the animation file with us?
0 -
to my mind scaling of model becomes using linear analysis.
0