Free size optimization with multiple PSHELL-based design variables
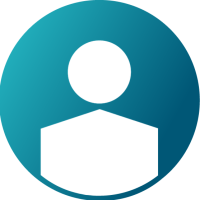

Hi,
I am working on a structural optimization of a model containing more then one PSHELL and PCOMPP properties.
I am experiencing some issues with the sized model generated after the free-size optimization (*_sizing.fem) as output requested by the FSTOSZ line (OUTPUT,FSTOSZ,YES,4).
I do not have any problem with the composite laminates but I have an unexpected behavior with the PSHELL components in the sized model generated.
I try to explain the issue below with an example in brackets.
If I have more then one PSHELL defined in the initial model (e.g., the PSHELL properties 2 and 3), I expect to have 4 times the number of PSHELL of the initial model in the new one (e.g, 2100, 2200, 2300, 2400, 3100, 3200, 3300, 3400) assigned to respective components (e.g., 2100->2400 assigned to components with initial property 2, and 3100->3400 assigned to components with initial property 3).
The problem is that, in the new sized model generated, only 4 of these PSHELLs (e.g., 2100->2400) are assigned to components of the model and all the others are defined but not assigned (e.g., 3100->3400). Furthermore, the 4 properties considered (e.g, 2100->2400) are assigned to the entire designable space, also to components where I would have expected different properties (e.g., PSHELLs 2100->2400 are also applied to components with property 3 in the initial model, where I expect the 3100->3400 to be).
This creates even more difficulties if the number of PSHELLs involved increases, because it becomes impossible to reproduce properly the optimized thickness distribution in the sized model with only 4 properties.
I hope the description of the problem is clear enough.
I am wondering if I miss something in the definition of the optimization problem or this is a known behavior for Optistruct.
I would greatly appreciate any suggestion/information concerning this problem.
Thank you in advance,
Alessandro
Find more posts tagged with
- I have four properties defined in the initial model (PSHELLs 1, 2, 3, and 4) and assigned to four different components.
- I created four different free-size design variables related to the four PSHELLs.
- I performed a free-size optimization with OUTPUT,FSTOSZ,YES,4 to obtained the sized model as output (*_sizing.fem).
- After the optimization, thirteen different properties are defined in the sized model:
- 1100->1400 related to the initial PSHELL 1
- 2100->2400 related to the initial PSHELL 2
- only 3100 related to the initial PSHELL 3 (because of the minor importance of property 3 in taking loads)
- 4100->4400 related to the initial PSHELL 4
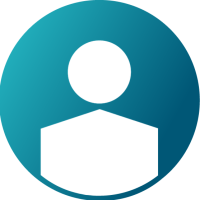

Hi Alessandro,
Are both properties part of design space?
Can you share the model file and .out file?
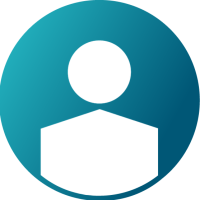

Hi @tinh,
Thank your for the quick reply.
All the properties are part of the design space and included in different design variables.
Anyway, I have created a simplified example with four different properties in the design space to highlight the issue. Please find attached the initial fem, the out and the sized fem files related to this model.
Thanks again.
Regards,
Alessandro
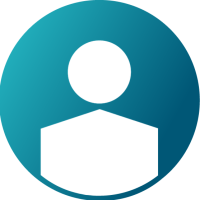

Hi Alessandro,
I think the property 3 is least participated in taking load, so because of the minimum thickness constraint (which is 2) all the material is removed and left with only 2 units of thickness.
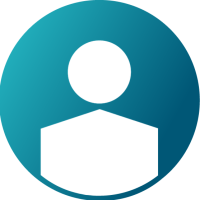

Hi Prakash Pagadala,
The minor importance of property 3 in taking loads can explain why I have only one property related to PSHELL 3 in the sized model (3100) instead of four (3100->3400), but this does not explain why most the properties generated are not assigned to the components and why the thickness distribution of the sized model is far from the optimal distribution found by Optistruct.
The example attached in the previous message explained in detail:
The problem is that only the last four (4100->4400) are assigned in the model, and they are assigned to all the components included in the design space, not only to the components related to the initial PSHELL 4. All the others properties (1100->1400, 2100->2400 and 3100) are defined but not assigned to any components.
The results is that the thickness distribution in the sized model (*_sizing.fem) is far from the thickness distribution obtained in the optimization (presented, for example, in the output files: *_.des.hrd, *.fsthick). This is because in the sized model (*_sizing.fem) only four properties (instead of the thirteen defined) are assigned in the design space to generate the model with the optimal thickness distribution.
In the example attached, the component with initial PSHELL 3 is, as you wrote, least participated in taking loads, and Optistruct assigned to it a uniform thickness close to the minimum one: 2.08mm. Consequently, the only PSHELL 3100 with thickness 2.08mm is generated, but this property is not assigned to the related elements. Instead, the property 4100 (with thickness 6.2mm) is assigned to the elements with initial PSHELL 3 and this spoils the results found by Optistruct.
I attached to this message also the*.des.hrd file.
Comparing the thickness distribution obtained by Optistruct in the*_.des.hrd file (with Hyperview) and the thickness distribution in the *_sizing.fem file (with Hyperview) you can quickly realize what I mean when I write that the sized model (*_sizing.fem) spoils the results found by Optistruct.
I hope I made the point clearer.
Please let me know for any further information/file needed.
Regards,
Alessandro
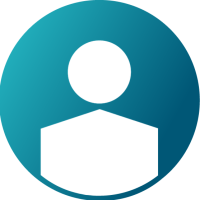

but this does not explain why most the properties generated are not assigned to the components and why the thickness distribution of the sized model is far from the optimal distribution found by Optistruct.
Hi Aleesandro,
I will check and update to you soon.
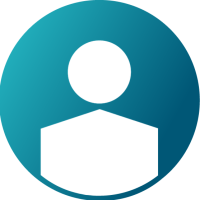

Hi @Alessandro
Reported the issue with development team.
You can try to adding all PSHELLs in singe DSIZE and adjust the number of bundles in OUTPUT,FSTOSZ.
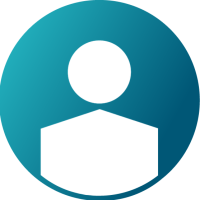

Thank you @Prakash Pagadala.
What you suggest can be a solution for a simple case.
If I have a more complex structure with many different PSHELLs to be optimized, I will need a high number of bundles in OUTPUT,FSTOSZ in order to properly replicate the optimal thickness distribution. In this condition, if I also have some composite laminates among the design variables, the OUTPUT,FSTOSZ request will be applied to them as well, resulting in an unwanted high number of plies in the optimized model generated.
Having the possibility to assign different OUTPUT,FSTOSZ requests to different design variables could really help in solving the issue.
Thank you again for your replies.
I hope we will have a solution from the development team soon.
Regards,
Alessandro
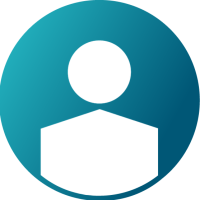

Thank you again for your replies.
I hope we will have a solution from the development team soon
Hi @Alessandro,
Thank you. I will update you soon once I have some solution.
Hi,
Please send us your *.fem file for better understand