Problems with type 7 contact, quasi static load
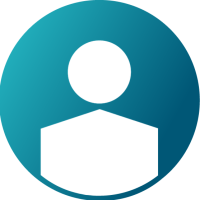

Hi all,
I'm working on a quasi static simulation of a FUP device for my thesis, however I keep having problems getting the contact energy/total energy in check. I've located the problem to the contact group and have been experimenting with it but, without real succes. I've been wondering if the possibility exists that I need a better defined material to get acceptable simulation results.
Included are my model file, rad file and T01 file.
Answers
-
Hi @Cekke_
the contact energy/total energy is not unusually high (7-12%), because friction increases contact energy. From Radioss Help:
Large contact energies relative to total energy can cause large negative Energy Errors because contact energy is not part of the Energy Error equation. If the simulation has frictionand a lot of sliding contact, then the large contact energy and resulting energy error can be considered acceptable.
I have made the following changes to speed up computation:
-defined mass scaling
-reduce the model in half due to symmetry in geometry and BCs
You have defined an impact problem because the force is ramped up in 0.01s. Quasi static simulations are usually done over a period of 0.3s.
You can simulate a static loading more computationally efficient by time scaling, which means applying the load more quickly than in the quasi-static experiment in order to reduce the simulation time. However, the kinetic energy should be low (5-10%) compared to the internal energy for most of the simulation, to minimize the inertial effects. You can check the energy fraction in Hypergraph by plotting both energies and using Vehicle safety tools (File-Load-Preference File) to divide curves (Math-Two Curves-Divide w/Zero).
0 -
Hi @Ivan,
Thank you for your quick response.
I came to the same conclusion with regards to the friction causing part of the higher contact energy. I still need to conduct the same simulation with a smaller element size, to check if this will have an influence. However I wanted to try and get as close to the acceptable limits given in 'Introduction to Explicit Analysis using RADIOSS – A Study Guide' as possible, before moving on to mesh refinement.
Regarding the load case, the way i see it i'm within limits with the Ek compared to the internal energy so ramping the load quickly is still OK in this case.0 -
I encountered another problem. I'm following a Unece Regulation R93 with regards to the load cases,... However they require the force to be applied on a infinitely stiff surface and transfered from this impactor surface onto the bumper. I assumed I could do this with just creating a rigid RBE2 or Rbody on the impactor shells and applying a concentrated load on the CoG of the rigid.
However I am not sure anymore if it will apply the force in the same way as it would in real life. What I mean is will it distribute the force over the impactor surface or will it just place my applied concentrated load to every node?I can't find how the load distribution is done with /RBE2 or /RBODY. Is there documentation available that gives an explanation.
Thanks in advance
Cedric
0 -
When you apply /CLOAD to the nodal group the force is applied to each node individually, so: total force = F(t) * number of nodes. However, when you apply to the independent node of the rigid body it will distribute the force evenly over all dependent nodes.
Note: the ICOG parameter defines how CoG is computed which can influence the load application point (check the attached document). See for example:
https://community.altair.com/community?id=community_question&sys_id=1e4600b61b2bd0908017dc61ec4bcb390 -
Could you tell me were you found this information about the load distribution? It would be nice to be able to reference a document in my thesis.
0 -
-
passives Could you tell me were you found this information about the load distribution? It would be nice to be able to reference a document in my thesis.
0 -
Altair Forum User said:
I encountered another problem. I'm following a Unece Regulation R93 with regards to the load cases,... However they require the force to be applied on a infinitely stiff surface and transfered from this impactor surface onto the bumper. I assumed I could do this with just creating a rigid RBE2 or Rbody on the impactor shells and applying a concentrated load on the CoG of the rigid.
However I am not sure anymore if it will apply the force in the same way as it would in real life. What I mean is will it distribute the force over the impactor surface or will it just place my applied concentrated load to every node?I can't find how the load distribution is done with /RBE2 or /RBODY. Is there documentation available that gives an explanation.
Thanks in advance
Cedric
Hi Cekke_
I checked your model. According to my understanding you need to simulate the impact between an impactor and bumber, so here a velocity in the direction of impact should be defined at the master node of the rigid impactor.
Secondly an interface must be defined between the impactor and bumber.
Is there any reason you have applied a concentrated load to the impactor?
Thanks
0 -
I need to simulate the crash test of a bumper, the Bumper needs to withstand the applied force for atleast 0.2 seconds and the forces need to be applied as rapidly as possible.
The regulation states that a force of max 80kN needs to be applied at a point P1. In real life testing this force application needs to be done as follows :<?xml version="1.0" encoding="UTF-8"?>
0 -
0
-
In case of the impactor, they don't specify anything, only the maximum size. This is why it's very hard to make a decent impactor assumption and why I went for a rigid.
Another aspect which I'm not sure about, do I need to add a self-contact when the bumper is only one part?
0 -
@Pranav Hari Are you able to give me any advice regarding my contact settings? I just want to know if the reason for not being able to get the contact energy in the 5% range is due to my contact or just due to the model itself.
0 -
Hi Cekke_
The energy error percentage is the parameter that checks the energy conservation during each numerical cycle and it is computed by RADIOSS is a percentage. If the energy error is negative it means that some energy has been dissipated.Normally the energy error should be less than 15% at the end of computation but if the model undergoes high plastic deformation the energy error can increase. As of now the energy error and contact looks fine in your model.
<?xml version="1.0" encoding="UTF-8"?>
Thanks
0 -
Hi Cekke_
I could reduce the contact energy when i ran the analysis without friction. So you can now conclude that this high contact energy in your model is due to friction.
Left side window of HyperGraph shows with friction of 0.15 defined and right side window shows with zero friction defined. You can see the drop of contact energy values from the below graph.
<?xml version="1.0" encoding="UTF-8"?>
Thanks
0 -
Hi @Pranav Hari,
Thank you for helping me with this. This confirms what I thought might be the cause, I also ran it without friction and got the same resulst. However It seems unrealistic to run the simulation without contact friction.
0 -
Hi,
Adding friction values to a contact makes the case more non linear and that's why you are getting high contact energy. In such cases you can safely discard this high contact energy.
If the contact energy is due to penetrations/intersections/contact definitions...etc then you will have to pay attention and need to reduce.
Best Regards,
.
0 -
Altair Forum User said:
In such cases you can safely discard this high contact energy
Yes that's true.
0 -
This may be a stupid question, but could you explain to me how this makes the case more non linear? I'm guessing this is due to the friction force changing over time and thus making the behaviour more non-linear? Or am i totally wrong with my assumption?
0 -
Hi,
When two bodies come in contact, the contact area is not known in advance. Thus, contact problems are highly non-linear due to the unknown surface
boundary conditions. In the meantime, the presence of friction adds another nonlinearity to the problem since it is irreversible and discontinuous. Moreover based on the friction law selected the solver will find the 'stick and slip' of master and slave in each cycle.Check online on contact algorithms to learn more about contact formulations in FEA softwares.
Best regards,
.
0