Midsurfacing with thin layers
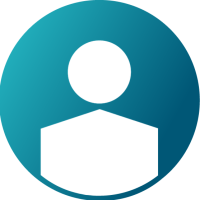

Hi all,
I want to run a Radioss analysis of a layered structure under impact. As my layers are too thin to be modeled with 3D elements, I want to use midsurfacing tool. Relative to that, I have 2 questions:
1. One thing I ask myself since the beginning of using midsurface is : should I translate the components relatively to the new midsurface ? ie. if a ball impacts a table, should I translate the midsurface of the table up, to make contact at the right time ? I would say you do not have to translate it as you indicate the thickness, but in my simulations, contact does not begin (vonMises stress = 0 ) before I can visually detect it. So I always translate my components, though it seems weird to me...
2. As I said, I want to model a structure comprised of different sheets of materials, which I would like to model as 2D elements.
Problem : - At first, my 3D components are in contact (if it had been a 3D mesh, I would have liked to have a continuous mesh)
- When I do the midsurface for each sheet, they have a gap; which is normal but which I wonder about : I suppose I should not translate my midsurfaces, however contact is not detected and I would like to use continuous meshing instead of interface option.
Hope that was clear enough. If you can give me some answers to my questions, it would be very helpful.
Thank you in advance,
Alice
Answers
-
1.To my knowledge mid surface should be at mid & solver must have some option to activate contact at certain distance.I request you share result & model files under Radioss forum for detailed information on this issue.
2.Would be nice if you could share screenshot of your model with type of analysis you are performing at your end.
0 -
Altair Forum User said:
As I said, I want to model a structure comprised of different sheets of materials, which I would like to model as 2D elements.
Problem : - At first, my 3D components are in contact (if it had been a 3D mesh, I would have liked to have a continuous mesh)
- When I do the midsurface for each sheet, they have a gap; which is normal but which I wonder about : I suppose I should not translate my midsurfaces, however contact is not detected and I would like to use continuous meshing instead of interface option.
Since you are providing thickness to components translation is not at all required and it is obvious that you see gap when you mesh with 2D elements,
There could be several reasons for contact not being detected between components. At first point check the normals of the elements. If normals are fine the problem must lie in contact definition.
0 -
Hi Rahul, Thank you for your quick answer !
1. I have always applied a little gap in the interface (~0.5 mm) as to prevent errors, as I got errors in interfaces due to gap_min = 0. But you tell me this gap_min of interface (I use INTER TYPE7) is used in 2D to define the thickness ? It seems weird to me, as the thickness is already defined in the propoerty (/PROP/SHELL) ...
Unfortunately I can't share the files, but maybe you can help me out without them. My question is on the thickness : were in the solver is it taken into account ? I will try the gap_min in interface but I am suprised I have to indicate it there if I already indicated the thickness in the shell propoerty.
2. I can't share my model this time either but I have done a simplified model that explains what I am working on : I have a thin box comprised of several thin layers. If I go with a 3D model I can do continuous meshing. Using Midsurface though, I have gaps :
- how do I indicate thickness for contact ?
- is there a way to keep continuous mesh in midsurface meshing ?
Thanks<?xml version="1.0" encoding="UTF-8"?>
0 -
Hi Prakash,
Thank you for your answer.
- How do I check if my normals are fine ?
- So you say as Rahul that I have to define my contact with a gap_min of thickness/2 ?
0 -
Hello again,
I come back to you because I launched my simulation and have one problem :
I input thickness = 3 in properties and Gap_min = 1.5 in INTER/7 for a 2D-modeled sheet under impact. However I get one warning per interface (3 interfaces) in the starter :
WARNING ID : 94
** WARNING IN INTERFACE GAP
DESCRIPTION :
-- INTERFACE ID : 706
-- INTERFACE TITLE : Interface_Silicone_Structure
INPUT GAP 1.500000000000
HOWEVER GAP IS RECOMMENDED TO BE LESS THAN 0.9999999992549
POSSIBLE IMPACT NUMBER: 0 (<= 1 *NSN)I ran the simulation anyway but my impactor (a hammer) starts to impact the component, before going through completely, without any contact. It is as if something went wrong and interface was deleted... I checked my energy balance, and it stays negative.
Do you have an idea of what the problem is ?
Thank you in advance,
Alice
0 -
Hi Alice,
This message is especially important in case of a self-impacting interface. This warning message means that at least one element on the master side has a side length less than twice the GAP and there is a risk of over stiffening.If the interface is not self-impacting, you can ignore this warning and the model behavior will be correct. I recommend you to go through the Help Menu on the Warning ID 94.
Please try recreating the interface and run the analysis. If the issue persist, please share the model file.
0 -
Hi George, Thank you very much for your quick reply. I will check all you said and come back to you for further questions.
I do not have a self-impacting surface though, so I think.
0 -
Hi George,
I checked my surface a little further. Unfortunately I have no right on sharing my model (even in your dropbox), due to confidential reasons. I will try to explain everything clearly though.
I have a hammer impacting a component. Between these two, a silicone sheet aims at diminishing the impact (plays role of damping). I think I found what goes wrong, but I do not know why and how to solve the problem (see attached file) : one element becomes very large as simulations goes on. And the surrounding elements self-impact the others... Note that the meshing of this silicone sheet is QUAD and of length less than half the interface gap, which causes the warning, and the interface ignorance.
Thank you in advance,
Alice
0 -
Hi again,
I might do something wrong : My silicone sheet has dimensions 10x10x3 mm so maybe I should not model it with shell elements... I would like though, because I do not care about the silicone's mechanical behavior. Please tell me what to do best :
- keep current thin shell elements
- thick shell elements
- 3D elements (heavy calculus already ...)
- spring elements ??
- other solution
Thank you in advance,
Alice
0 -
Hi Alice,
As a workaround try increasing the thickness of the silicon sheet and review the results. Also, check the material properties of the silicon plate.
Can you record the animation and send across so that we can understand the behavior better.
0 -
Hi George,
Thanks for your answer
Please find attached a video of the simulation. It seems that everything is okay until t=0.75s. Then the hammer goes through without noticing the interface.
Altair Forum User said:As a workaround try increasing the thickness of the silicon sheet and results.
I don't understand why I should increase thickness ? Shouldn't I decrease it ?
Altair Forum User said:Also, check the material properties of the silicon plate.
My material is the following :
/MAT/OGDEN/205
SILICONE
# Init.dens
0.000923
# Poisson sigma_cut Bulk_func_ID Fscale M Iform
0.48 0 0 0 0
#N parameters: mu_i
0.0287 0.0286
#Blank Card#N parameters: alpha_i
2 2
#Blank Card
It is the typical material used for rubbers.
Thank you in advance for your help,
Alice
0 -
Hi Alice,
This seems bit strange. But commenting without the model file is tough. If we were able to go through the file we can suggest the workarounds for it.
But I doubt on the material parameters. In the Help Menu for /MAT/OGDEN we have a sample material card for rubber material. Please go through the material parameters in Help Menu and ensure the parameters are correct.
If possible, please share the file through secure dropbox which will be safe.
0 -
Hi George,
I will try several material parameters, including the example's ones. This was actually my model for creating OGDEN material law.
One simulation is already running. I will update you on changes.
Thank you,
Alice
0 -
Hi again,
Simulations are running. Meanwhile I was searching a bit more about silicone representation. I wonder about several things:
1. In the example you sent the screenshot of we have :
mu1 = 0.002009
mu2 = 1.27E-6
alpha1 = 2
alpha2 = -2
However, in the comments section, it says, (mu1,alpha1) and (mu2,alpha2) should each be 'greater than zero' (see picture). How should I understand that if (mu2,alpha2) does not seem greater than zero ? The values I input in my file (see above question) come from literature, tis is why both my alpha_i are positive.
2. what is sigma_cut ?
0 -
Hi Alice,
When modeling low-density foams, it is important to consider potential failure under tensile loading. Tensile cut-off stress (sigma_cut) is to input a limiting stress which essentially models a elastic-perfectly plastic behavior in tension.
I recommend you to refer about Ogden and Mooney-Rivlin model in RADIOSS Theory Manual where the formulation is explained. And many open sources on this material model are available in the web.
0 -
Okay thank you for this explanation. I already looked for it in the theory manual and literature but sgma_cut is not explicited there... So is it maximal stress or yield stress ? This is not clear to me.
0 -
Hi Alice,
Sigma_cut is the tensile cut-off stress,that is we are limiting the tensile stress to remain at a cut off value.
0 -
okay I see, this is not a physical stress so. Thank you!
I shared a simplified model in your dropbox. It is not the real component, but is a good representation of what I am working on.
Thank you in advance for helping me out on this
0