polymer tear test
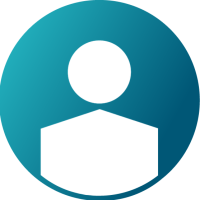

Hi,
I want to tear a polymer, so set up the model and run it.
Material is defined for particular test by MAT LAW 2.
Its running but after some time elements get deleted.
Analysis not completed and stopped.
Herewith shared the output file and deck file.
Please suggest the solution.
Answers
-
Hi Tushar,
Are all the material parameters correct?. Especially a, b and n values.
Which is the unit system you have followed for this analysis?.
0 -
Hi,
I am using HDPE and a,b, n values are correct.
Unit system: mm,msec, Mpa, N,gram
Now trying the same with MAT LAW 27 as the model is flexible type.
0 -
Hi Tushar,
LAW 27 is for brittle models, I believe. So tearing may not suite to this material model.
Can you check with LAW 34?
0 -
Hi,
MAT LAW 34 is only for solid elements and our model is flexible which almost flexible polymer(2D meshing).
So, I am using MAT LAW 27 for flexible material from the reference of following post.
Kindly suggest me the proper material law for flexible polymer.
0 -
Hi Tushar,
I was just going through the material card. LAW 27 is similar to LAW 2 with an additional space for modeling brittle failure/material damage.
0 -
In the out file it says Normal termination.
Can you share the animation file?
0 -
Hi,
I run the analysis with LAW 27 and consider the Aluminium properties from Help example as follows;
#RADIOSS STARTER
#---1----|----2----|----3----|----4----|----5----|----6----|----7----|----8----|----9----|---10----|
/BEGIN
LAW27_void Aluminum
110 0
Mg mm ms
Mg mm ms
#---1----|----2----|----3----|----4----|----5----|----6----|----7----|----8----|----9----|---10----|
/MAT/PLAS_BRIT/3
Aluminum
# Init. dens.
0.0027
# E NU
60400 0.33
# A B N SIGMAX
90.266 223.14 0.375 177
# C EPS0 ICC
0 0 0
# EPST1 EPSM1 D_MAX1 EPSF1
0.16 0.72 0.999 1
# EPST2 EPSM2 D_MAX2 EPSF2
0 0 0 0
#---1----|----2----|----3----|----4----|----5----|----6----|----7----|----8----|----9----|---10----|
#ENDDATA
/END
#---1----|----2----|----3----|----4----|----5----|----6----|----7----|----8----|----9----|---10----|
Herewith shared the output file and animation file.
Please check it and suggest whether LAW 27 is appropriate for flexible polymer or not.
0 -
I am unable to open the h3d file at my end. HV crashes as soon as I open it.
anyways, can you atleast paste a .gif image of the animation?
0 -
Hi,
There is a normal termination.
Please check the tear1.gif image.
0 -
Hi Thushar,
Can you check the material law 35 (/MAT/LAW35 ). This law is applicable only for shell and solid elements and can be used polymers, elastomers, seat cushions....etc.
0 -
Hi,
I believe MAT LAW 35 is not suitable for my requirement because it works air enclosed in material, also it works only till elastic region.
Whereas plastics generally do not have enclosed air, and show elasto-plastic behavior.
I want to simulate tear strength or tear propagation in plastic laminate.
0 -
Tushar,
Most of the material is teared and there is no load transfer happening beyond which complete tear down will be seen.
I think this is the reason analysis terminates.
If you have a stress strain curve for your model try with LAW 36 and check if you see a similar behavior.
0 -
Hi All,
In RADIOSS which material card is best to apply For a super tough, high viscosity acetal homopolymer grade with superior impact resistance - Derlin material ?
I have tried with MATL36(Full solid brick elements) and it is not working properly
Thanks,
Senthilkumar
0 -
Hi,
What kind of analysis you are trying to perform?.
For impact simulations, if interested in energy absorbtion, and evaluate risk of cracks, LAW36 is sufficient.
Or are you interested in permanent strains after unloading or creep/relaxation effects?.
Please let me know the type of analysis and objective so that we can guide you.
0 -
Hi ,
Its a high velocity dynamic analysis. When i used LAW36 the component is deforming severely and element spike was happening.
The same model was worked properly in Dyna with MATL24 card.
0 -
Hi,
/MAT/LAW36 is the equivalent material law in RADIOSS for Law24 in Dyna.
Which element formulation you are using and also for material law is it only a single curve or multiple curves with strain rate dependency?.
If possible please share the model file and h3d file through my secure dropbox link.
0 -
-
Hi,
The solid formulation seems fine.
Can you please share the model file so that we can review and can suggest the possible workarounds.
0 -
-
0