Different material models
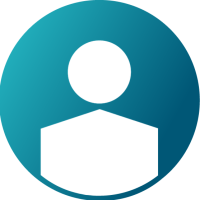

Hey,
at the moment I try to model bite force between two teeth. For on tissue - which is called periodontal ligament - i try to include viscoelastic behavior. I already simulated it with linear elastic behavior and it worked perfect. If i try different viscoelastic models, it doesn't work at all. (Problems with negative mass)
I think it is because i modeled it as just one layer in contact with two different surfaces (look at the attached model) and therefore I have a really high deformation in my elements. Is it possible?
I want to use Hypermesh to remesh my model (a finer model) and equivalence the surfaces. How is it possible?
Thanks for your help!
Best,
Max
Find more posts tagged with
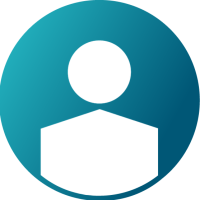

Hey,
thanks for your help.
If i use the option /DT/BRICK/CST i got this problem:
MESSAGE ID : 73** ERROR IN ENGINE INPUT DECK CARD : DTERROR TERMINATION
and i already use the Ismstr =2 in my model.
My problem is now my model with my imposed velocities works fine and i got results, if i double the the way (same imposed velocities a second time) i got a MASS ERROR how could this happened?
Thank you very much.
Best,
Max
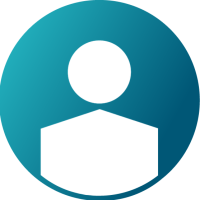

Hi Max,
When Ismstr=2 is applied /DT/BRICK/CST should be used in engine file for switching to small strain.
Mass error shows the added mass to meet the time step control requirements. Did you impose any time step in the model (/DT/NODA/CST) ?
Using /ANIM/NODA/DMAS in the engine file user can analyse the mass variation in HyperView.
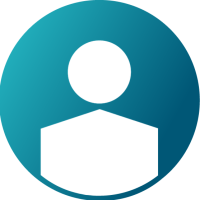

Thanks for your help. I solved it /emoticons/default_wink.png' srcset='/emoticons/wink@2x.png 2x' title=';)' width='20' />
Hi Max,
I think you are facing zero or negative volume error termination during the run. This NEGATIVE VOLUME error happens when solid elements are very deformed and their characteristic length goes to 0. For large strain formulation the time step of an element goes to 0 when the element is compressed. Use Ismstr =2 in the solid property and in RADIOSS Engine file use the option/DT/BRICK/CST which will set the time step value tmin at which the solid elements will switch to small strain.This means that the solid elements using Ismstr =2 will use large strain formulation while their time step remains greater than tmin, and will then switch to small strain formulation.
to search for free edges and combine them with a matching edge within the cleanup tolerance.
Equivalence subpanel can be accessed from the edge edit panel. This option is used to search for free edges and combine them with a matching edge within the cleanup tolerance, and thereby the topology can be refined to achieve a better mesh.
You can also go through the HM-2030: Refining Topology to Achieve a Quality Mesh tutorial in Help Menu where these options are covered.