Fricional contact analysis
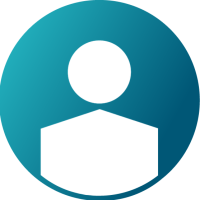

I am trying to simulate an autofrettage process with the optistruct solver but i am not able to get any plausible results.
In theory the process and simulation should be quite easy. We have two parts: a swage and a tube.
The swage (which has a slightly bigger outer diameter than the tube) is pressed through the tube which results into contact with friction and plastic deformation in the tube.
I meshed both the swage and the tube (only one quarter of each and conditions for symmetry to reduce the calculation time), defined all the boundary conditions like constraints and the load (forced displacement of the swage) but somehow the contact condition doesn't work at all.
I read several tutorials and have tried different combinations of contact-surfaces or set-entities which were linked by a contact interface. I tried the preset contact types like slide/freeze/stick as well as a contact property with MU1/MU2 coefficients.
When I use slide or freeze (images below) I get extremely high deformations and it looks like the points where the first contact occurs don't separate anymore, In addition to that I don't understand how they can already be in contact at that point since the contact should occur later when the bigger diameter hits the edge of the tube. Displacement scale factor is always set to 1.0.
When I use the contact property (pcont) the calculation takes forever and I don't get any results (no convergence). I already tried to increase the number of iterations up to 50 and NINC up to 25.
I would really appreciate any helpful advice or maybe someone with experience could check my model file.
<?xml version="1.0" encoding="UTF-8"?>
<?xml version="1.0" encoding="UTF-8"?>
<?xml version="1.0" encoding="UTF-8"?>
<?xml version="1.0" encoding="UTF-8"?>
<?xml version="1.0" encoding="UTF-8"?>
Answers
-
-
Hi,
Can you share the modified model?
Why not use pressure instead of stempel?
0