Composites Optimization - FSTOSZ
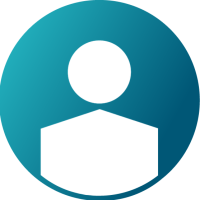

Hi,
I am currently working on a composites optimization for the Formula Student Competition. Thanks to great tutorials for creating my model, I am now using the FSTOSZ output for my first optimization.
When I open my new .fem file (which was created after my fstosz), I have 92 plies in total, and the most of it is under 0.05mm thick....
As far as I know, I have to reshape every plies, but what about thicknesses ?
I tried to enter a TMANUF value (0.4mm for each carbon fiber ply), but I still observe that my plies are <0.05mm thick.
For information, my laminate is the following :
- 4 plies of 0.4mm carbon fiber (90,-45,45,0 orientation)
- 1 ply of 20mm aramid honeycomb
- 4 plies of 0.4mm carbon fiber (90,-45,45,0 orientation) --> Symmetric
What am I supposed to do to complete the process of composites optimization ?
Thanks for enlightening me.
Best Regards,
Nicolas RICHTER
Answers
-
Hi Nicolas,
You will get the correct thickness from size optimization. Free size is good to take ply pattern and thickness estimation.
Free size optimizes element orientation thickness continuously, so the thickness of each ply varies across geometry. Then FSTOSZ just simplify the model by dividing the continuous distribuition into 4 (default) ply shapes with a certain median thickness.
You cant base your results from free-size, it's just to get an idea on where to put material so you should start with a little bit higher thickness in the plies. This in order to have sufficient orientation thickness where it is needed.
The Size optimization will optimize ply thickness, so you can use TMANUF in order to get a multiple of this number as ply thickness.
Hope it helps.
Best regards,
Gonçalo
0 -
Altair Forum User said:
I tried to enter a TMANUF
TMANUF has no role in Free size. This TMANUF will be carried forward to SIZE optimization for thickness optimization.
As @GonPer said Free size provides ply patterns.
0