segmentation violation error
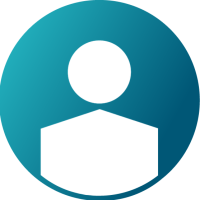

Answers
-
Hi Ramakiran,
Please share the complete starter out file. Also, please run the model checker (Tools>Model Checker>Radioss Block) so that any modelling errors can be identified.
0 -
sir i have sent you the out file in secure file drop box.
0 -
Hi Ramakiran,
This seems to be an issue with the groups in the model.
Please share the model file through the secure dropbox for debugging.
0 -
sir, i cant share it, but for spot weld contacts in the model of taurus shared in this site they have created spots contacts for every single element and single spot as shown in the attached image? cant we give contact between all spots and all elements at one shot? is that an modeling error?i mean to say like the second image
0 -
Hi Ramakiran,
Those contacts what you see in the model were created automatically by HyperMesh when spot weld was modeled. The connection between weld element and the component is established using a tied (Type 2) contact in the background and so these contacts were created.
Can you do a model checking in HyperCrash, as HyperCrash also has a good tool for checking modelling errors.
I recommend you to share the model through dropbox, and the file will be secure with us.
0 -
ok sir, i will try to debug myself today, thing is if it is hexa, contacts are being generated automatically but for spring elements its not happening, can i know how contacts will be generated automatically for spring type spots, when i use mesh dependent and ensure projection options?
0 -
Hi Ramakiran,
Please go through https://www.youtube.com/watch?v=fNc9oVVkBa8 which is a webinar series where creating connectors in RADIOSS user profile is shown.
0 -
okay, thank you sir for your endless support and guidance.
0 -
good morning sir,
I have created spots and those spots automatically created contacts, and now the problem is with rigid elements, its showing error in model check that rigids master is on element. Should we not connect one element to other element with rigids with single node to node connectivity? The modeling of 2 components with rbe2 is as shown in the image.
0 -
Hi Ramakiran,
It is not recommended to set a node of the mesh as the master node of a rigid body.
•The local system of the master node is not compatible with options imposing rotations (except boundary conditions and imposed velocities). If some elements having a rotational stiffness are connected (such as beams, some springs and shells), an incompatibility occurs.
•Depending on the flag ICoG, which is used in the rigid body definition, a lot of mass and inertia can be added locally onto the node; as well as the node can be moved to the center of mass of the rigid body.
Always we recommend to use calculate node option while creating rigids so that master node will not be in element.
This will not result in run termination, it will show only as a warning.
0 -
okay thank you sir. i will try with calculate node then.
0 -
Good evening sir, I have a problem after having welds my mass of whole vehicle increased from 2.67 to 7 tonnes after spot welds, is it valid or whats thereason for increase in mass
0 -
Hi Ramakiran,
Once the connections are created you can see that a property (Type 13 spring) is automatically created and assigned for the connections.Please check the mass of the springs in that property card. Please note that the unit system followed for that property card in default is KN,mm,ms and kg. Hence you are getting a high increase in mass.
Please change the property accordingly, that is create a separate property card with your own values, following the unit consistency.
0 -
ok thank you sir.
0 -
mass of each spring is 0.0015 kg if its default unit system of property card and about 4000 spots are present in my model gives 5 kgs 0nly right? it is correct and what about the tension stifness torsional stifness? they are 1000 kn/mm, 5000kn/mm etc. should i take them in newtons or kn , the unit system of material is mpa and im using mm mpa n ms t system
0 -
Hi Ramakiran,
You have to change the spring stiffness also, as per the unit system followed. Else the stiffness of the spring will be very less and may cause deformation.
Since you are following T, mm,s you can keep all stiffness 1e5 so that a high stiff connection will be created.
0 -
yes sir, i have converted this file from nastran profile to radioss what are the default unit systems for materials after conversion? i gave density as 7.85 e-9 following mpa system for materials but in nastran its mass is 700 kg while in radioss its showing 2700 kgs after non linear material updation
0 -
-
Hi Ramakiran,
User has to follow a specific unit consistency. Normally many follow Tonnes, mm and sec.
The unit consistency normally followed is attached along.
Do you have any /SURF set in the model?. Also, check the interface id 22 in the model. Please do a model check.
0 -
ya then its fine fine i am following the same and yes i have surface set, ive checked the interface 22 its fine with slave and master and also it is interface between spot and element which are automatically created
0