Topography optimisation of a single ply in a 2 ply composite laminate
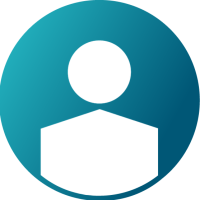

Attached are 2 Hypermesh models. The Aim is to minimize mass. I have used 2 composite plies to model the structure. 2 PCOMPG properties have been assigned to the plies respectively. Only 1 out of these 2 plies needs to be optimized topographically to obtain stiffener patterns. The other ply must continue to remain in its original shape
In the “volume_feasible.hm” file , I have minimized volume as the objective. The optimization run gives a feasible design. However, when I check the results, there is no change in the shape of the ply and no bead patterns are obtained. Next, I changed the objective to minimize mass just to see if I get the desired result. Again, I obtain a feasible design but there is no change in the shape of the ply and no bead patterns are obtained. In this model, no contact has been defined between the plies.
In the “stick_contact.hm” file, I’ve defined a stick contact between the two plies and run the optimization. Here again, I obtain a feasible design but there are no bead patterns obtained in the result.
if anyone has tried a similar problem before please help me out.
Answers
-
Hi Kushgen,
I did not open your .hm files but I can tell you something from what I've read in your post.
Minimizing volume or mass is the same thing because Mass=vol*rho, unless you are using materials with different density's, rho. I don't know if the program will acount for the volume increase or not because of the gap between plies but I think you get the idea.
If you ask to minimize any of then it will just try to implement the structure which gives the less volume and that's not really what you are looking for because in a topography optimization, the design variables will make the area of surface increase, which in a ply is constant related with the volume/mass.
Unless you have some displacement or something as constraint that will have to stiff the structure it will always be that result.
My sugestion, try minimizing compliance with a massfrac, volfrac, volume or mass constraint to see if you get some results.
Best regards,
Gonçalo
0 -
Hi Kushgen,
What is your objective?
You have a buckling design constraint of lower bound of 1. Can you explain why you have chosen 1 for buckling?
Also, topography may or may not reduce the mass of the design. So you may have to re-think about your design objective.
0 -
Hi Prakash,
My objective is explained very well in the question I posted. I'm trying to optimise a structure for minimum mass while meeting the constraints.
A minimum buckling constraint of 1 ensures your structure doesn't buckle under the applied loads. Topography may or may not reduce the mass, that's right. I want the minimum possible mass that meets my requirements
Thanks,
Kushal.
0 -
Hello Gonçalo ,
Minimizing volume and mass are the same things, I agree with this. I tried to minimise volume because minimising the mass didn't give me an optimised design, so it was a workaround you can say.
Kushal.
0 -
Hi Kushal,
Sorry for a late reply. I lost the question in the stream of questions on forum.
So, Can you increase the buckling constraint value say to 1.128 and check if you can see any bead patterns.
0 -
Hi Prakash,
Increasing the buckling constraint to a value greater than 1 will be detrimental to my objective of reducing the mass. To meet the increased buckling constraint values, more material will be added to the structure. And there is no guarantee that bead patterns will be observed. I've not tried increasing the buckling constraint value though.
Kushal.
0