Setting a contact between two parts (Formula Hubs FEA)
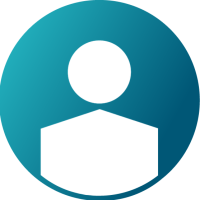

Hi,
I am a new user of Altair Hyperworks and using it for FEA for our university Formula Student team.
When trying to do the analysis for the rear hubs, I couldn't get sensible results and I think that is because I haven't connected two components, which are the hub itself and steel inserts.
<?xml version="1.0" encoding="UTF-8"?>
I have tried looking for some tutorials or instructions, but couldn't find anything that was helpful for me. So how do I set the contact?
Also my second question is about applying the forces. For example when applying the torque the way I am doing it is taking all the nodes on the surfaces and connecting them to a dependent RBE2 in the centre and then applying the torque to that single node.
<?xml version="1.0" encoding="UTF-8"?>
Does this make sense or does it create additional stiffness and RBE3 should be used or is there any other way that I should be using for applying the forces?
Thanks a lot,
Justas
Answers
-
HI Justas,
I suggest the starting point to be the detailed discussion on contacts in the HyperWorks student guide - http://www.altairuniversity.com/free-study-guide-book/
Tutorials like - OS-1365: NLSTAT Analysis of Solid Blocks in Contact
If your model has solid elements, then using a rigid element is the only way to apply torque, (this is a good way to apply forces as well) this is discussed in page 272 of the guide. and the boundary conditions and loads chapter can help you.
As to the question about the choice between RBE2 and RBE 3, see page 283 - 'Imposing Boundary Conditions (Constraints And Forces) By Means Of RBE2 And RBE3. What Are The Differences?'
0