Composite Optimization with different carbon fabrics
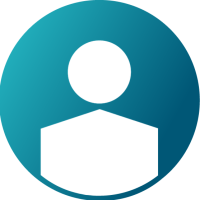

Hi all,
I am Federico and I am trying some Free Size composite optimization simulations. I have seen from the tutorial in the website that the optimization is carried always with the same material (generally UD fabric) with different orientations. If a core has to be considered i have noticed that its orientation is set to 180°. Why this?
I tried to run a simulation considering different fabrics : a UD fabric and a +/-45 Biaxial fabric. I cannot replace the biaxial using +/-45 UD in the model since the carbonfibre types are different (I am considering a high modulus UD and a high strength biaxial fabric).
I tried to run my simulation with both fabrics but the results are questionable. Is it possible to use more fabrics or is it only possible to use a single one with different orientations?
Thanks
Answers
-
Hi Fede_Guru,
What is the tutorial you were reffering to? I am not sure why it was set to 180° (it will be 0° again).
Regarding Bi-directional ply.. Fabric is considered as 1 single ply while its bi-directional nature is incorporated in the material properties. If E1 and E2 are equal in material card then the ply is a bi-directional fabric and the reference material orientation is the longitudinal direction (or Major direction/load direction).
0 -
Altair Forum User said:
Hi Fede_Guru,
What is the tutorial you were reffering to? I am not sure why it was set to 180° (it will be 0° again).
Regarding Bi-directional ply.. Fabric is considered as 1 single ply while its bi-directional nature is incorporated in the material properties. If E1 and E2 are equal in material card then the ply is a bi-directional fabric and the reference material orientation is the longitudinal direction (or Major direction/load direction).
Here at pag 7 you can see what I am talking about:
I just ask other two quick questions:
-what is the difference between PLYMANN defined in the design variable and TMANUF defined in the size panel? Both of them should mean that a ply can only be manufacture within a certain thickness, so why are they defined twice?
- this is off topic.. I noticed that if I apply loads and b.c. on a geometrical entity like a mesh, and then delete the mesh or remesh, the loads and bc are gone as well..Is there a way to fix it?
0 -
Hi,
TMANUF is what you give in the PLY based modelling. but PLYMAN can be used for both ply based and zone based.
When you re-mesh you can anchor the nodes which has BCs and loads. This will not move or recreate node at that locations.
0 -
Altair Forum User said:
Hi,
TMANUF is what you give in the PLY based modelling. but PLYMAN can be used for both ply based and zone based.
When you re-mesh you can anchor the nodes which has BCs and loads. This will not move or recreate node at that locations.
Actually in my optimization PLYMAN seems to have no effect as the thickness varies continuosly - only when I add TMANUF the thickness is discretized, so I still do not understand the difference.
How is it possible to anchor nodes?
I also have a doubt on the optimization results. For each ply bundle four shapes are generated, but I don't understand what these are. It means that for each bundle there are 4 thicknesses and the bundle thickness is the sum of these 4 layers?
0 -
Hi Fede,
Anchor nodes during meshing?
Yes, each bundle thickness is the sum of the each ply.
0