Time step smaller than DT/INT/DEL
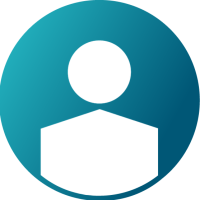

Hello,
I am doing a study inflating an airbag with a particular shape and there are a lot of contacts between surfaces, that I modeled with interface type 7. I have some troubles because there are some nodes that pass through master surfaces (even if the interface is activated) but then the contact is applied and the nodes can not pass through, creating high contact forces and reducing the time step. I wanted to use the control card DT/INT/DEL to delete the interface in those nodes, I fixed Tscale to 0.9 and Tmin to 1.0 e-4. When I run radioss, time step reduces up to 5e-5, some nodes are deleted but not those that passed through surfaces and have high contact forces. Any idea about how can I deactivate interfaces in nodes where the contact force is higher than a fixed value?
Thank you
Answers
-
Hi,
Please check the contacts for any penetrations. The normal value for contact energy is 0% to 5% of the total energy.
Check the Gapmin value and also check the contact stiffness. Try with Inacti=5 and strongly recommended to verify that there are no initial penetrations.
An example (Example 4) is also available in our Help Menu. The model files are attached for reference
0 -
Hi,
you should define type 11 line interface in addition to type 7 (or just type 19 which is a combination of type 7 and 11) in order to avoid nodes passing through master surfaces.
Radioss user guide describes:
Interface type 7 does not deal with edge to edge impact. When the mesh is fine enough, edge to edge penetration is often followed by a node to shell contact. The main problem with edge to edge impact is the locking situations. If there is a change of load after edge penetration, locking is unavoidable since a node to surface contact is detected. This usually leads to high penetration; therefore, the analysis comes to a standstill as time step is reduced. If locking occurs, the use of interface type 11 in this area is necessary to solve the problem.
0