Topology optmization & static analysis fails
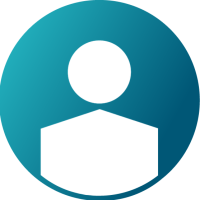

Hi guys, since I need a quick concept structure, I've decided to do the analysis and optimization with inspire.
Well, i do have a small solid which is loaded by a simple force and supported (don't evaluate the support, it's like 'anything' for the test run). I have created a design space and the forces and supports are located on 'non-design' parts.
Every time I try to do a topology optimization, it fails and the following message pops up: 'Optimization Error 157'. The parts from the tutorials do work...
I need an urgent help and thank you in advance for your answers
You will find the file in sthe attachment
Answers
-
Hello,
Your setup looks good and work for analysis as well as optimization. Check below images. Which version of Inspire you are using? Make sure you have read/access to documents folder (default run directory). Send me a message with your contact details, we can chat over a webmeeting.
0 -
Hi Jaideep,
I've installed inspire 2017 yesterday in the company and I'm currently working on my workstation there. I'll send you a pm. Tnx!
Best regards
0 -
Hello Jaideep,
one last thing. In aviation, there are the flight maneuver loads in up-, down-, fwd-, back- and side-direction (x,y,z). Let’s assume that the loads in up- and down-direction are just two loads with the same magnitude but in the opposite directions (force_up=150N in y-direction and force_down=N in negative y-direction). How can I get a result in topology optimization with both load cases considered for the optimized shape? In my calculations, I always get an empty design space which looks like the load cases cancel each other out.
Regards
0 -
Hi Mouse-T,
I guess Jaideep already discussed this question with you in pm - but to allow our other users to gain Inspire experience I'd like to answer also public:
Any topology optimization with Inspire take respect to the internal stresses, caused by external forces. If you have two loadcases with exactly mirrored resulting forces, there will be no difference for the optimization as both loadcases will cause exactly the same optimal design approach. Loadcases are equal weighted.
In case you have to expect nonlinear behaviour (part/assembly behave different on tension and compression), you may have to check your final design for buckling and activate the option 'sliding with seperation' during analysis. If there is a dramatic difference in the model/system behaviour, you could activate this option for optimization too.
Regards
Felix
0