Suspension Rocker
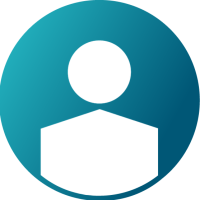

Good Afternoon Everyone,
I have a bit of a noob question for y'all; I'm trying to optimize a bell-crank for a racecar suspension and am struggling to properly constrain it. I have tried a few iterations, the first with a force being applied to one side of the bell-crank (input from push rod), with the opposite side (shock connection) fixed. I then applied a rotational constraint to the pivot point which doesn't really make sense if the shock connection is fixed. While this does output a model, it doesn't appear to be correct. I have attached a picture showing what I currently have from this iteration. If I apply a force on each side, I get a displacement error.
If someone could shed some light on what constraint to use for the shock side of the bell-crank or even point me to some documentation on this, I would greatly appreciate it.
Thanks,
Boost
Answers
-
Hi Boost,
glad you found your way here!
Your model seems to be constraint correctly - to get better results, you may reduce the 'min. Thickness' constraint in optimization explorer, and run a 'max. Stiffness' optimization first. These results can be analysed to get the factor of safefy you can achieve with a specific mass and 'min. Thickness'. The factor or safety from your reanalysis (based on your optimization result) now can be taken into account for the 'min. Mass' optimization - which may provides you with nicer design approaches.
Feel free to share your file with us if you would like to get a more detailed answer.
Hope this helps!
Regards
Felix
BTW.: There are some nice tutorials and online trainings availible also: http://www.solidthinking.com/SupportTutorials.aspx?category=Support&item=Tutorials
0