Fatigue Analysis Load time history
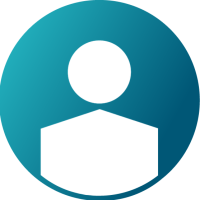

I have performed fatigue analysis with different load time histories. I am confused with the result obtained. I have attached my results and query in a word file.
Please help.
Answers
-
0
-
Altair Forum User said:
Hello Sir,
The load magnitude is same in both the cases is 1.0
The Load amplitude is not same.
In case 1 for 2.5 seconds the load varies as 0 1 0 1 0 1
But in case 2 for 2.5 seconds the load varies as 0 1 1 0 1 1
How many seconds of load time history is required for optimal result as i have mentioned in my query it hugely affects the life results.
0 -
Question1: · Why the fatigue life varies drastically with the number of seconds of load time history imported into the fatigue analysis?
Answer: The number of cycles is repeated and that is why life is reduced as you increase the repetitions.
Question 2: · The loading in CASE 2 is more frequent but the fatigue life results are higher than CASE 1. what is the reason behind this scenario?
Answer: Again, the number of cycles in case 2, I think is less than case 1. You can confirm this by using RNFLOW which will output fatigue and damage
0 -
Altair Forum User said:
Question1: · Why the fatigue life varies drastically with the number of seconds of load time history imported into the fatigue analysis?
Answer: The number of cycles is repeated and that is why life is reduced as you increase the repetitions.
Question 2: · The loading in CASE 2 is more frequent but the fatigue life results are higher than CASE 1. what is the reason behind this scenario?
Answer: Again, the number of cycles in case 2, I think is less than case 1. You can confirm this by using RNFLOW which will output fatigue and damage
Thank You Sir for your suggestion i have performed fatigue analysis with no repetition of load cycles but obtained conflicting results. I have attached the results and query in a word file. It will be a great help if you have a look and comment on it.
0 -
Can you share the RNFLOW file for case 1 and case 2, please?
0 -
Sir i am not able to follow. Can you hint which is the RNFLOW file and how to get it.
0 -
Goto Global output request and RNFLOW. This should write a .rf file in the working directory.
0 -
Please share RNFLOW for both cases and both data sets.
0 -
Sir currently i dont have all RNFLOW files
I have to run analysis again for each case to get the file.
I tried for 1 case i have a .rnf file in the directory. It is more than 60 Mb. Can you hint how to open this file. So that i can check myself.
Can you please answer the third query on how much load time history i should import for both cases.
0 -
0
-
-
Sir i have attached 2 .rnf files
1 for Case 1, 1 cycle 0 1 0
another is case 2 , 1 cycle 0 1 1 0
Please comments on the load time history query.
0 -
Hello,I have a query regarding TABFAT card definition. I am unable to import the load time history with 0.5 sec time interval. Optistruct is automatically assuming 1 sec time interval.
I have attached the load time history details in a word file. I will be obliged if you take a look and comment on how to take the time data with 0.5 sec interval.0 -
Hi @Soumya Sanket Mishra Is it possible to share all related files?
0 -
Altair Forum User said:
Thank You Sir for your suggestion i have performed fatigue analysis with no repetition of load cycles but obtained conflicting results. I have attached the results and query in a word file. It will be a great help if you have a look and comment on it.
Case 1 is 1 cycle which is straight forward, Case 2 is also considered as a cycle (from 0 to 0) and that is why there result is same in both the cases.
0 -
Hello,
In fatigue analysis which stress averaging method should be used,
As there is a huge difference in fatigue life results for none and simple averaging method.
0 -
Unaveraged results are preferred over average method results. From a design point of view, it is safer and recommended.
0 -
Hello,
Thank You Sir for clarification on stress averaging.
I have performed a fatigue analysis with
Maximum static stress = 616.88 MPa
I got min life = 5397
But the Ultimate Tensile Strength of the material given as input = 586 MPa
My question is the component should fail at UTS but even though stress is higher i.e. 616.88 MPa the fatigue life is more than 5000 cycles, shouldn't the life be closer to 0 cycles.
0