Additive Manufacturing with Draw Constraint
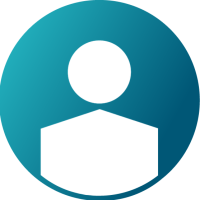
Hi,
As you know, one of the most important issue in additive manufacturing is "Enclosed Voids" due to trapped powder and supports.
I think these issue can be prevented in a topology optimized design with split draw constraint.
My overall question is what should be the draw directions in a design which will be manufactured with SLM? i was applying the directions accordingly build orientation but i'm not sure it is correct or not.
I would be very appreciated if you reply my question and i can read papers you will recommend.
Answers
-
Hi Baturalp,
The split draw constraint you mention is originally designed for the metal casting process. As such it is not designed to produce an optimized shape tailed to powder bed additive manufacturing, but for casting with a parting plane. That isn't to say you can't use it to come up with some concepts. You just may find that you'd have a lot of overhanging regions if you used it, requiring more support structure.
For metal powder bed additive manufacturing, we have the overhang angle constraint in OptiStruct, which can be used with reference to the build plane to reduce the amount of support structures. Minimum and maximum size member control can also be modified, as well as considering the topology optimized design without the manufacturing constraints.
As topology optimization is concept-level, certain changes will need to be made in the final design after the optimization stage (such as adding holes for powder removal if necessary).
Thanks,
Rob
0