Radioss - Fabric
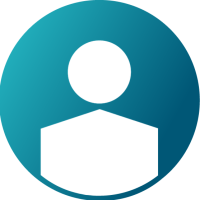

Hi everyone,
could someone help me with composites simulation?
I'd like to understand the difference between material law 25 and 58 to make the better choice for my simulation: in attach the data sheet of the material.
If someone have theoretical and pratical (tutorial) material could shear it?
Many thanks in advance
Marta
Answers
-
Hi,
LAW 25 comes in two forms. One with Tsai Wu and the other with CRASURV. This law is more suitable for modelling structures made of composites (uni and Bi)
LAW 58 is a general Hyperelastic orthotropic fabric model. This is suitable for modeling airbag modelling.
0 -
Hi Marta,
material law 25 is used to model a cured composite laminate and is usually simulated with shell formulation (bending stiffness).
Material law 19 and 58 are used to model fabrics (airbag, seatbelt or composites forming ) and is usually simulated with membrane formulation (no bending stiffness).
Attached is a sample Radioss solver deck with the mentioned material laws and properties (units are N, mm, s, MPa).
0 -
Thanks a lot for your replay, but I have some doubts about this topic.
I'll try to explain my problem.
I have to simulate a component made of thermoplastic composite: glass fiber Twill 50/50 fabric, thickness 1 mm composed by two ply.
Based on material characterization I have to do the curve fitting; consider, for exemple, traction test: I simulated the lab test with Radioss Block, I defined the material using law 25, I defined ply (assigning that material) and laminate. To the sample I have to assign a material and I choose the only one I have. Than, I compared Radoss and test stress-strain curve: the two are too different so I modify E11, E22 and Yield values to obtain a virtual curve similar to the real.
Is procedure right? If so, what is the importance of ply and laminate if I assigne the same material to single ply and to whole sample?
Thanks
0 -
You can calibrate the material with Hyperstudy- please refer to tutorial HS-4200
There is even a video of the procedure and a PDF.
what is the importance of ply and laminate if I assigne the same material to single ply and to whole sample?
It is very important to assign plies corresponding to laminate layup of the test sample: orientation, thickness and stacking sequence.
0 -
Altair Forum User said:
Thanks a lot for your replay, but I have some doubts about this topic.
I'll try to explain my problem.
I have to simulate a component made of thermoplastic composite: glass fiber Twill 50/50 fabric, thickness 1 mm composed by two ply.
Based on material characterization I have to do the curve fitting; consider, for exemple, traction test: I simulated the lab test with Radioss Block, I defined the material using law 25, I defined ply (assigning that material) and laminate. To the sample I have to assign a material and I choose the only one I have. Than, I compared Radoss and test stress-strain curve: the two are too different so I modify E11, E22 and Yield values to obtain a virtual curve similar to the real.
Is procedure right? If so, what is the importance of ply and laminate if I assigne the same material to single ply and to whole sample?
Thanks
The procedure is correct but lengthy... As @Ivan suggested you can follow as the HS tutorial.
A laminate can have plies with the same material or different materials. The characteristics of a laminate vary with ply orientation, thickness, material and the way the plies are stacked.
0 -
Thanks a lot for your active assistance! I'm grateful for all of this!
0