Importing STEP - Save to Geom in Database, or not
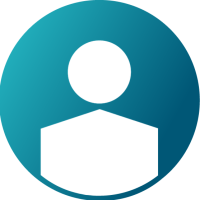
Can someone shed light on 'Save Geom in Database', or not?
I've had weird things happen when Checking this box, with zillions of apparent faces being imported rather than solids. But then it didn't repeat. Next time just the solid bodies.
Which database? The model.slb file or a database somewhere else.
It does not appear I should ever need to check that box, based on successful imports.
Answers
-
Hello Darad,
Saving geometry (only parasolid) into database has many advantages starting from Altair SimLab 2019.3.
We are implementing more and more CAD operations which will be available only on Parasolid mesh imported with 'Save database' option.For example, you can use options like REMOVE HOLE and REMOVE DETAILS to defeature the CAD geometry even before meshing.
You can use the MOVE tool to drag a CAD face, change a radius or a thickness.
You can use BOOLEAN operations to join the cad bodies before meshing (very important feature).
You can use 'fill hole' to fill a missing CAD face.
The disadvantage is that there must be a cad conversion into parasolid, and there is always a small risk that something goes wrong.
0 -
I tried the Boolean of bodies on a more complex model. The Boolean worked to connect bodies. After 2D Mesh, Unmerge failed. Any possibilities?
I did like the 2D mesh for boolean 'connected' bodies. Last year, I struggled with clean mesh transitions between bodies, as I had varied element size too much between bodies.
If the mesh size was doubled, transitioning from body to body moving away from stress-of-interest, the interface mesh was very clean after Remesh, i.e. transitioning from 2:1 mesh density.
Darryl
0 -
What I would really like is ability to Create CAD Welds, i.e. fillet, groove, fill-in weld prepped parts with welds. The current weld via modifying mesh doesn't work for me. Seems Simlab would need a Sketch-i-Pace feature to create precise weld profiles, and ability to extrude (vs polygon from existing vertices).
The only tools that works for me is old NX I-DEAS 6.1, via its Master Modeler for reconstructing often bad STEP geometry from scratch, glossing over weld preps of zero interest, and creating all sorts of solid welded to evaluate stress. And leveraging its History Tree for creating bodies in a modular fashion, and integrating such features into the Tree. Easy to modify and update features via the Tree.
Its Join Partition feature is/was so powerful -- like no other tool, not even newest SimCenter 3D. Join Partition allows Extruding a new part feature up to and beyond one or more faces. The resulting volume stops at those faces. Really superb feature. Else, one would need to create such weld volume face-by-face. Hence, until I-DEAS stops working totally, I will use this tool to reconstruct complex assembly-like models, i.e. single part, with both simple and complex weld shapes.
For solid welds, I often create an offset profile along an edge of a body to be welded, e.g. 0.5' wide. Extrude this profile 0.5' as a new part. Round any corner edges as desired. Chamfer the part 0.5: Voila! You have a clean fillet weld, that can be integrated into the structure body. Sometimes, I've created the 0.5' wide profile along a snaking path, in and about lots of corners. Round corner edges. Chamfer 0.5'. Done. So easy. No one else here uses this techniques (they use HM). I'm an I-DEAS dinosaur for a tools with an early death in 2020s.
Perhaps, something like this could be implemented for Simlab CAD weld creation. and likewise for bevel/groove on weld prepped parts.
0