The Impact of Simulation on Everyday Foam Products
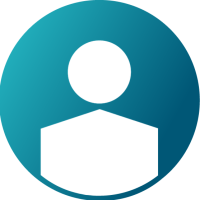

From ideation to production, simulation-driven design has been guiding the way engineers and designers approach product development. With applications in both the industrial and consumer goods sector, simulation-based design for manufacturing (SDfM) processes have impacted the way many of the products around us have been constructed.
Polyurethane (PU) foam is used in a broad array of industries including automotive, electronics, transportation, furniture, packaging, and healthcare. Due to their lightweight, sustainable nature, adaptable strength per unit weight, insulation characteristics, and low energy requirements for production, polyurethane foams are an attractive and cost-efficient solution for engineers looking to add cushioning, sound dampening, or thermal insulation to their products.
Because of the range of different materials that can be combined to produce polyfoam, many manufacturers are able to create foaming products depending on their specific needs, from flexible molded foam components to rigid foam panels. The array of material compositions, however, present challenges to product designers who must understand how the foam will fill during manufacturing, and how it will perform under loads and stresses. Products using PU foam can also be susceptible to common manufacturing defects caused by foam shrinkage and porosity.
Altair Inspire PolyFoam™ is a modern, integrated approach to polyurethane foaming simulation. Manufacturers can efficiently explore designs and optimize molded foam parts early in the development process to reduce scrap and tooling rework costs. With the ability to inject multiple foams into the same mold simultaneously, Inspire PolyFoam allows for quick and accurate simulation of different foam compositions. Companies such as Samsung and Haier have been using Inspire PolyFoam’s solutions to improve their production processes for refrigerator insulation. With a dedicated history of providing polyurethane foaming simulation to major OEM’s in both the automotive and consumer goods industries, Altair provides a streamlined approach to every step of simulation.
Rapid Simulation with a Five-step Workflow
An efficient workflow is critical to the foaming simulation process, ensuring that foam product designs can be validated faster and with fewer design iterations, which significantly reduces costly mold trials. With Inspire PolyFoam’s five-step workflow for process development, ideal part design, material usage, and manufacturing processes can be determined before the physical production of a foam part begins.
Polyfoam is frequently used for automotive interiors like vehicle seat cushions, headrests, frame insulation, and steering wheels. To demonstrate Altair’s experience with polyurethane foaming simulation in this industry, this example shows the five-step workflow process for a vehicle seat using Inspire PolyFoam.
1. Create or Import Geometry
To begin, either import a 3D design from existing CAD geometry for the foaming part or create a customized mold within the Inspire software. Designing a mold for a seat cushion requires that a pouring basin be created for the foam to be injected into. Optimizing the basin is a crucial step to ensure that the liquid will flow correctly into the mold.
2. Define Nozzle
In this step, users can define nozzle sizes, foam injection directions, and material-flow start and end times for the simulation. In addition, test and optimize different nozzle travel paths for releasing the foaming chemicals into the seat cushion mold. In a case where a vehicle seat cushion requires a different type of foam on the sides of the cushion as compared to the center, users can utilize the multi-foam injection feature in Inspire PolyFoam. By implementing this technology before production, manufacturers can proactively find solutions for problems found during the pouring, filling, and expansion processes. For uniform simulation testing across solvers, import pre-existing nozzle paths and positions from an existing file to compare simulation results from previous trials.
3. Designate and Create Components
When simulating the injection of the vehicle seat cushion, Velcro was applied to the base of the mold to avoid foam part movement. Materials, inserts, and guiders can be applied to reinforce certain mold regions as needed. Incorporating tooling into the foaming simulation process ensures that during injection, any unnecessary movement that could disrupt the foaming is avoided.
4. Determine Process Parameters
Before the foam pouring is simulated, select criteria such as gravity tilt pouring parameters, foam part temperature, and mold and foam materials. Polyurethane foam in the future will be made available within the Altair Material Data Center, a cloud-based single master materials database for browsing and comparing simulation materials. For further customization of simulation trials, companies can securely add their own proprietary materials to the Inspire PolyFoam database.
5. Run Simulation and Analyze Results
After running the simulation, utilize PolyFoam’s analysis tools to easily detect common manufacturing problems in the injection and foaming process like air traps, porosity, weld lines and turn-up. Inspire allows users to gain an early understanding of their design, whether it is a part level inspection, or for a complex foaming assembly. In this example, elements such as temperature and pressure changes, load responses, and filling time were analyzed in order to optimize the overall foam pouring process for the vehicle seat cushion.
Working with Altair Inspire™
Altair Inspire offers a comprehensive set of solutions to develop innovative, manufacturable products faster from the initial part design and understanding the entire molding process, to efficiently analyzing and optimizing the performance of complex parts. With no solver-specific knowledge required to navigate simulation tools, Inspire enables production teams to rapidly analyze and modify geometries, reduce cycle times and manufacturing defects, and make informed design decisions early in the production process.
Learn More: https://www.altair.com/inspire-applications/