Combining AI and simulation for efficient bulk solids handling optimization
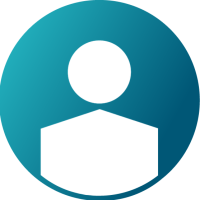

1. Introduction
The rapid virtual optimization of industrial processes is at the core of the Industry 4.0 paradigm but it requires the development of computationally efficient methodologies that go beyond a purely simulation driven approach to include machine learning based reduced-order modelling. This is particularly true in the context of industrial bulk solids handling processes, where the computational expense of high-fidelity simulations is significant.
In this work we present an efficient virtual optimization methodology for industrial bulk handling processes, which combines high-fidelity numerical modelling in EDEM with statistical and machine learning methods in HyperStudy, Activate and romAI to significantly reduce the computational expense of optimization relative to a purely simulation driven approach.
The validity of the methodology is demonstrated through a case study on bin blending which is a fundamental unit operation in a wide range of manufacturing processes in the pharmaceutical, food and chemical industries. The trial-and-error optimization of bin blending systems through physical prototyping is time consuming and expensive, making virtual optimization a significantly more cost-effective option.
2. Methodology
2.1 Overview
The proposed methodology is conceptualized in Figure 1.
Altair HyperStudy is employed for the automatic generation of a statistically efficient dataset of EDEM simulations and the machine learning algorithms in romAI are leveraged for the generation of a dynamic reduced-order model of the system, which relates process operational parameters to Key Performance Indicators (KPIs). An optimization algorithm in Altair Activate is then used to operate on the reduced-order model to rapidly identify the optimal operational parameter values.
Figure 1 A conceptual representation of the proposed optimization methodology
2.2 High-fidelity modelling with Altair EDEM
EDEM is Altair’s market leading discrete element modelling software, which can be used for the high-fidelity simulation of industrial bulk solids handling processes.
In this case study, EDEM is used to simulate the generic bin blending process shown below.
Due to the complex mechanics of bulk solids handling processes, such high-fidelity modelling is a computationally expensive but essential first step in relating operational parameters to KPIs.
In this case, the blender operational parameters include the rotational velocity , the angle of twist and the mass in the system, as described in Figure 2.
Figure 2 Blender operational parameter space
The KPI of interest is the time evolution of the mixture uniformity as quantified by the Segregation Index in Equation 1, where Cij is the number of contacts between particle types i and j.
The segregation index is inversely proportional to mixture uniformity and should decrease with mixing time as shown in Figure 3.
Figure 3 Example result for the time evolution of the Segregation Index in an EDEM bin blender model
2.3 Dataset generation using HyperStudy
The generation of a reduced-order model using machine learning methods requires training data from several EDEM simulation runs with varying operational parameters. These can be run in a statistically efficient configuration and Altair’s design exploration suite HyperStudy is used for this purpose.
In this work we use HyperStudy’s Design of Experiments (DoE) feature to generate and run a data set of EDEM simulations according to the three factor - three level Taguchi design described in Table 1. This design represents only one third of the corresponding full factorial design and is therefore three times cheaper to run.
The resulting data set is used for the generation of the romAI reduced-order model as discussed next.
Table 1 EDEM simulation runs in a 3x3 Taguchi DoE
2.4 Reduced order modelling with romAI
Altair’s romAI is a novel application, which combines Artificial Intelligence and systems modeling techniques to generate reusable continuous dynamic models from existing data.
Dynamic romAI models are computationally efficient models that constitute a state-space representation of dynamic systems. They can be thought of as Reduced Order Models (ROMs) with respect to the responses of interest in the system.
Due to their high computational efficiency, romAI models can be used to speed-up system design and optimization or serve as components of Digital Twins in real-time and control applications.
In the context of this work the romAI model is conceptually illustrated in Figure 4 and takes the blender operational parameters as inputs and the segregation index as both an output and a state.
Figure 4 A conceptual representation of the romAI dynamic model developed in this work
A key feature of romAI is it’s simple and intuitive workflow, which can be executed in Activate and is demonstrated below. It involves a data preparation step, where data can be imported from a comma delimited file and filtered using a smoothing algorithm to reduce stochastic effects, a model generation step where the model parameters are defined and the model is trained on the provided data, and an analysis step where the model accuracy can be evaluated using standard metrics and testing data.
The testing data in this work is obtained from an EDEM simulation using random values of the operational parameters within the domain. This data is used to evaluate the predictive accuracy of the romAI model. The parameter values of the test simulation are summarized in Table 2 and the results are shown Figure 5.
Table 2 Operational parameters of the test simulation
Figure 5 Comparison of test simulation result and romAI prediction
An excellent quantitative agreement can be observed between the simulation and romAI results, demonstrating the ability of the romAI model to predict the evolution of the segregation index for an unfamiliar combination of blender operational parameters. Furthermore, it can be observed that the romAI model is able to accurately predict the segregation index beyond the time range contained in the training data. This eliminates the need to simulate the long mixing times needed to reach the final state of the mixture, leading to further reduction in computational expense.
The evaluation of the final mixture uniformity for a given set of operational parameters using the romAI model is highly computationally efficient and enables the near-real time optimization of the bin blending process using the built-in optimizer of Activate as discussed next.
2.5 Parameter optimization in Activate
Activate is an Altair integration platform for comprehensive system-of-systems simulation. Its block-based modeling environment enables users to easily integrate and operate on a wide range of systems including romAI dynamic models. In this work we connect our romAI model to Activate’s gradient descent based optimizer in order to rapidly identify the optimal blender operational parameter set. The workflow is demonstrated below.
A total of fifty parameter combinations are evaluated in seconds to identify the optimal operation with respect to the final mixture uniformity. This is several orders of magnitude faster than the equivalent purely EDEM based approach.
The model prediction for the optimal parameter set is verified against the EDEM simulation results and an excellent agreement can be observed as shown in Figure 6, demonstrating the validity of the approach.
Figure 6 Verification of the optimal parameter set - romAI prediction vs EDEM simulation result
3. Conclusions
The Altair portfolio of tools enables the efficient virtual optimization of bulk handling processes via a hybrid methodology that combines high-fidelity modelling in EDEM with statistical and machine learning methods in HyperStudy, Activate and romAI.
The use of the methodology can result in several orders of magnitude reduction in computational expense relative to a purely simulation-based approach, as demonstrated in this case study on bin blending.
This high degree of computational efficiency makes the virtual optimization of bulk handling processes practical both in the context of design and real-time operation.
For more information, please visit the Altair product pages at:
Altair EDEM – https://www.altair.com/edem/
Altair HyperStudy – https://www.altair.com/hyperstudy/
Altair Activate - https://www.altair.com/activate-applications/
romAI - https://www.altair.com/ai-powered-design/