What's New in Inspire Extrude 2022
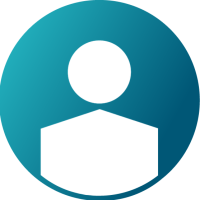

Metal Extrusion
Inspire Extrude 2022 has now been released, and includes the following new features and enhancements:
Heat Transfer Subcase in Coupled OptiStruct Analysis
Inspire Extrude supports coupled analysis with the OptiStruct solver. When the pressure in the extrusion simulation reaches the specified convergence tolerance, the solver writes the loads on the contact surfaces between the workpiece and the tool. These loads are used by OptiStruct to perform the tool stress analysis and compute tool deformation. The modulus of the tool varies significantly with temperature. To consider this, the coupled solution has been enhanced to perform a heat transfer step subcase before performing the stress analysis. To enable this, the solver writes temperature on the tool contact surfaces in addition to pressure. This new feature increases the accuracy of the stress analysis solution. (IEXT-2656)
Advanced Tool Heat Transfer Analysis
You can now perform advanced tool heat transfer analysis using the HyperXtrude solver itself for both profile nose cone and full-cycle analysis. With this new feature, you can access the tool thermal management system supported by the solver. In future releases, all the solver options will be made available to users. (IEXT-2030)
Mandrel Offset
The recommended procedure is to flush the mandrel and remove the offset before creating the mesh. This is accurate and also will result in good quality mesh in the welding chamber region. The solver also supports the scenario where the user can mesh the model with the mandrel offset intact and not flush it at the CAD/mesh. The solver will account for this in the computation by the specified value of the mandrel offset. This helps save time in correcting and updating the geometry. In this release, Inspire will support the specification of mandrel offset in the GUI. This option is shown in Advanced Bearing Parameters and should be specified only for the bearing curves on the mandrel. (IEXT-2375)
Reorient the Model After Simulation
Inspire orients the model such that the profile comes in the positive Z direction. In this release, an option to reorient the model to the original configuration has been implemented. This is mainly intended for bearing optimization analysis to get the optimized bearing curves in the original configuration. This feature will work only if you have set up the model in version 2022. (IEXT-2045)
Improvements to Choke Angle Computation
The solver uses bearing reference surfaces to compute the choke angle in the bearing region. An additional mechanism has been implemented to suppress the noise in the choke angle due to geometric inaccuracies in the underlying reference surface. This improves the choke angle estimations from the bearing reference surface.
Quenching
Improvements to Heat Transfer Computations in Immersion Quenching
The solver uses more accurate heat transfer correlations to model the phases of the cooling curve for Immersion Quench. Additional parameters have been added to modulate the cooling curve. The solver also accounts for the effect of subcooling on the critical heat flux.
Natural Convection HTC on Free Surfaces Outside the Quench Zone
The solver automatically computes the heat transfer inside the quench zone. Inspire users can now specify the natural convection heat transfer coefficient used for the regions of the profile that are outside the quench zone. In the previous release, a default value was used by the solver.
The full release notes are available at: