Oil Particels going trough Wall, Usage of SPH Method in SimLab
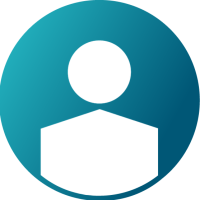
Hello Everyone!
I am using the nFX Tools in SimLab 2019.3 to create a simulation environment with SPH Particels.
What i want to realise:
I just have a cup filled with Oil. It is open on both sides and surrounded by Air and i want the Oil to run out of the cup downwards. To close the system there is a cover around the air volume.
I have defined three Materials, the two Fluids Air and Oil, and a Wall Material. The Material specalizsations can be seen in the attachment.
I created the three different sorts of Particels in three steps. First i sealed the cup to create the Oil Particels inside the cup and the Air Particels. Then i opened the cup again and created the Container Particels as Wall. Finally i have put these three together.
To realise that the Oil runs out of the cup downwards i have created a Domain 'Body Force'.
The problem now is, that during the simulation with nanoFluidX some Oil particels are getting through the Wall Material of the Cup but i Have no idea why. In the video attatched i have visualised the Velocity and the Oil (grey). The cup is not visualized there. These particels are like shooted out of the cup.
I have also attatched an STL Model oft the cup and the cover. They are one model.
Does anyone have an idea what the problem is or what i am doing wrong?
Thanks a lot!/emoticons/default_smile.png' srcset='/emoticons/smile@2x.png 2x' title=':)' width='20' />
<?xml version="1.0" encoding="UTF-8"?>
Answers
-
Hi Linux34,
There could be many reasons why would this occur, but material definition is most likely not related to the problem.
For us to be able to provide better help, the log file of the simulation and the .cfg input file would be beneficial. Could you please share those here?
Thanks,
M
0 -
Hey Stanicm,
thanks for your reply!
Here are the .cfg input file and the log file.
thankful regards
L
0 -
So, looking at your log and .cfg - I cannot really see anything wrong. The only thing that strikes me is that your reference velocity (ref_vel) is 0.1 m/s, which could be a tad-bit too low, but I assume that a draining fluid could accelerate to faster than that under free fall. Try setting the speed to 0.5 m/s and see what happens.
Additionally to the above conservative measure, you can try to ramp up the gravity a bit more slowly by setting the:
t_damp_bodyforce_end 0.1 ; (instead of 0.01)
in the domain parameters. That might help stabilize things a bit.
Finally, as a last resort, for these quasi-hydro-static type of problems, using the RIEMANN interaction scheme would probably be beneficial as it is more diffusive and would certainly smooth things out.
In order to do so, you need to set in the simulation parameters:
adhesionmodel true
freesurface true
transportvelocity false
surften_model ADAMI
energy_transport false
viscTempCoupling false
dt_factor 1.0
maxitsteps 1000000000
operationMode NORMAL
interactionscheme RIEMANN
MLS_thres 0.97
APD_coeff 0.001
RM_freq_rho_reinit 20
RM_rho_filtering INSTANT
damping_type LINEAR
and in the phase parameters for oil/air:
phase
{
name Oil
type FLUID
rho_0 842.0
dyn_visc 0.0463
surf_ten 0.03
print_info true
print_phase true
rho_compr 0.005
rm_beta 3.0
rm_rho_theta 1.e7
}
phase
{
name Air
type FLUID
rho_0 1.2
dyn_visc 1.800000E-5
surf_ten 0.03
print_info true
print_phase true
rho_compr 0.005
rm_beta 3.0
rm_rho_theta 1.1
}The run will definitely be slower with these conservative settings, but you should get quality results, assuming sufficient resolution and no flaws on the geometry side.
Hope this helps.
0 -
I will try these things out.
Thanks for your help!
0