Wet Granulation in EDEM
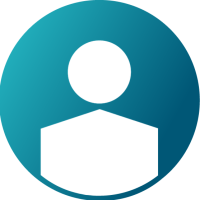

Wet granulation is the process through which particulate matter, usually in the shape of powder, changes into granules by agglomerating its elements into clusters of bigger sizes. It is a common process in different industries such as pharma, foods and chemical.
Typically, the process starts with a vessel where dry powder is stirred by an impeller and coated with a liquid, which creates an interparticle attractive force that granulates. Controlling the process and final size of the granules is of high interest as any defects would mean the processed batch being discarded.
Granulation is a phenomena occurring at micro scale level and it is necessary to represent real particle size in order to capture it accurately, which typically means it is not possible to model with the currently available hardware if practical computational times are desired.
However, Altair® EDEMTM offers the possibility to look at granulation indirectly to allow users to make informed operational decisions in mostly 2 ways:
- Evaluate granulation time and final size distribution through the methodology proposed in: “Nakamura, H., Fujii, H. and Watano, S. (2013) ‘Scale-up of high shear mixer-granulator based on discrete element analysis’, Powder Technology. Elsevier B.V., 236, pp. 149–156. doi: 10.1016/j.powtec.2012.03.009” Which is also the only experimentally validated approach to granulation
- Optimize granulation operational parameters with a liquid migration model that shows liquid dispersion in the equipment
More details on the first approach can be found in the referenced publication. Regarding the second option, the key aspects to take into account would be:
Step 1 – Materials
In general, materials should be calibrated or use existing material models:
If a liquid migration model is used as specified above, it is necessary to perform material calibration at different particle liquid contents. To be able to change the behavior of the powder as it increases its liquid content is necessary to capture the dispersion of the coating amongst the bulk and the overall flow within the vessel. A good starting point is to calibrate using the Angle of Repose but targeting a few responses, 4 for example, obtained at different liquid contents.
Step 2 – CAD
EDEM supports many file types such as STL, STEP, IGES. Geometries are imported to EDEM via the Creator > Geometries > Import Geometry section. You can choose either the default mesh which is optimised to capture the geometry shape while minimising the mesh elements, or choose a manual mesh size. You may want to manually select the mesh if your analysis includes wear as the wear is plotted per triangular mesh element.
Step 3 – Introduce Material
Typically, a powder conditioning cycle takes place to ensure the starting condition inside the vessel is uniform. This usually consists in operating the impeller at a lower speed than the process one for a short time. In EDEM it is recommended to introduce the powder particles by rainfall with a dynamic factory to place the powder material stationary at the bottom of the vessel.
If a liquid migration model is used, the model will require a spray factory to create the liquid added to the powder. To reproduce the system as accurately as possible, it is important to reproduce the real position of the spray nozzle. Utilizing EDEM´s spray factory, the span angle of the spray can be reproduce alongside the spraying rate.
Step 4 – Assign Kinematics
For granulating equipment, the necessary kinematics tend to be rotation motions. The impeller would require the user to define a rotating axis and speed but the same will be necessary if a chopper exists in the system.
Step 5 – Running the simulation
It is typically recommended to run EDEM models utilizing 1 or several GPU devices to have the model results as quickly as possible. This recommendation is specially relevant for powder applications that last for a relatively long time, as the granulation cases can take around 1 minute before any behavioral trends can be observed. Always estimate simulation time when choosing particle size, shape and shear modulus.
Step 6 – Analyzing results
Once the simulation is finished it is straight forward to visualize the velocities, mixing trends of the powder and torques required by the rotating parts to operate at that rate. If a liquid migration model has been used, it is also easy to observe the evolution of the liquid spreading over time by coloring the particles depending on their liquid content.
In general, the quality of the final granules is related to the uniformity of the liquid dispersion. However, it can be difficult to understand liquid dispersion within the system with visual analysis only. In EDEM, such an attribute can be observed by postprocessing the coefficient of variance of the liquid within the system. This is achieved by covering the volume occupied by the powder within the vessel with bins utilizing the grid bins selection option. The liquid content in each bin can either be postprocessed in EDEMPy or exported in csv format to then calculate the coefficient of variance using the standard deviation of the liquid content in each bin. The typical outcome of this analysis would be a graph showing the progression of the coefficient of variance over time, which facilitates the comparison of operations with different process parameters.
More details about the aforementioned Liquid Migration Model (EDEM API) can be found in this post:
More are outlined in our EDEM Tutorials:
Learn more about EDEMPy:
See how EDEM can be coupled to Altair MotionSolve: