Parameterizing an EDEM-AcuSolve model in HyperStudy
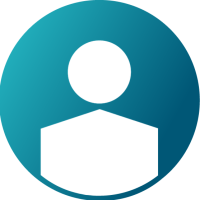
Altair® EDEM™ is used to model storage and conveying of materials, mixing, segregation, breakage. With heavy equipment EDEM is used for tool ground interaction, material flow optimization and durability analysis. For more information about the wide range of EDEM applications you can see examples here:
In this post we are focussing on the design and operation of equipment that handles particle-fluid flows. Particle-fluid flows can be virtually optimized using parameterized using EDEM-AcuSolve coupled models where the model parameterization is conducted in Altair HyperStudy using the EDEM-HyperStudy connector and HyperStudy's file editing functionality.
The fully configured model and all other requisite files for this example can be downloaded here:
This article details the parameterization workflow using the windshifter shown below as an example.
Case 1: Wind Speed at 15m/s Particle velocity | Case 2: Wind Speed at 5m/s Particle velocity |
Fluid velocity | Fluid velocity |
The HyperWorks CFD tutorial for Particle Separation in a Windshifter details the set-up of the 2-waycoupled EDEM-AcuSolve model.
Once you have the coupled simulation set up, export it as windshifter.inp by selecting File > Export > Solver Deck.
Next, create a new study in HyperStudy, where the following steps will be performed:
- Parameterization of the CFD solver deck (.inp file)
- Parameterization of the EDEM deck
- Automation of coupled simulation execution and data extraction
1. Parameterization of the AcuSolve model
- In HyperStudy, add a Parameterized File model in the definition of the HyperStudy Setup
- Add the windshifter.inp as the resource and scroll down to the Simple Boundary Condition Section. Next, highlight the average_velocity value and create a new variable called inlet_variable, setting its bounds and nominal value.
- Make sure to change the solve input file to be windshifter.inp and click on Import Variables
2. Parameterization of the EDEM model
- Update the EDEM simulation's total time to be 0s
- This example uses a singular material in the simulation with the settings below, as opposed to the two materials defined in the coupling tutorial
![]() | ![]() |
- In the Simulator tab under data save, click on Setup Simulator Queries. Add two queries for particle mass flow rate for each sensor. Make sure to enable the option for "Omit Header Info". Any other simulation attributes can be added here for analysis. This allows for EDEM data extraction into a .csv, while the simulation is running.
- Add two Mass Flow Sensors with the settings below in the Analyst tab by selecting Setup Selections
![]() | ![]() |
![]() |
- Add an EDEM model to HyperStudy, selecting the .dem deck as its resource
- EDEM model parameters can be included in the study clicking the import button of the EDEM model and selecting from the parameters tree as shown below.
3. Automation of coupled simulation execution and data generation
- In order to automate the execution of the coupled simulation, copying the parameterized windshifter.inp and EDEM files into a combined folder is necessary
- Go to the Test Model tab in HyperStudy and press on Run Definition. This should create two folder (m_1 and m_2) in the study's setup_1_def folder, under the approaches folder
- Go back to Define Models and add an Operator as your third model
- Register a new Solver under Solver Execution Script. Click on Add Solver Script > Other Application and point to the acusolve_edem.bat, which comes with the files attached. Rename it as EDEM_AcuSolve
- Make sure to edit the acusolve_edem.bat file to call the correct directory path for you acuRun.bat and edem.exe in lines 5 and 8, respectively
- If you are using Linux, the EDEM_AcuSolve operator must point to acusolve_edem.sh instead. Again, make sure to change the path for acuRun and EDEM accordingly.
- In the Operator's Solver Input Arguments add ${dirname m_3.file_3}
- In the Define Models tab, select Model Resources
- Right click on the Parameterized File model > Add Output File, and select the windshifter.inp
- Right click on the EDEM model > Add Output File, and select all EDEM deck files (.dem, .dfg, .efd, .ess, .ptf)
- Right click on the EDEM model > Add Output Folder, and select the EDEM deck _data folder
- Right click on the Operator model > Add Link Resource, and select all the output files available
- Right click on the Operator model > Add Input file, and select the Acusim.cnf and MESH.DIR files
- Your model resources should look like this:
- Under the Test Model tab, select Run Definition. Select Show in Study Directory. The run_00001/m_3 should have all requisite simulation files as well as the result files in .csv format
- To extract the simulation data, under Define Output Responses, select the Data Sources tab
- Add two Data Sources, selecting mass_flow_up.csv and mass_flow_down.csv. Select Read Simulation for the tool and under Components delete the TIME component and select Q1: Average Particle Mass Flow Rate instead. Do this for each .csv file
- Under the Define Output Responses tab, add two Output Responses. Under each response, define the expression to be mean(ds_1) and mean(ds_2). This will calculates the average mass flow through each sensor, based on the .csv data sources
- Particle behaviour results can be viewed in EDEM and the flow results can be visualised in HyperWorks CFD
- To add a DoE, right click on the explorer window and add a DoE, taking the definition from the setup. To learn more about DoE's and HyperStudy, visit the the HyperStudy documentation
All requisite files for this example can be downloaded here.
To see a how-to video on this topic, click here.
To learn about coupling EDEM and AcuSolve watch the Introduction to AcuSolve Computational Fluid Dynamics - EDEM coupling webinar