Modelling a Bulk Solids Mixer Drivetrain with EDEM, MotionSolve, PSIM and Activate
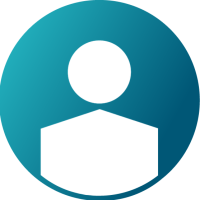
Bulk solids mixing is a fundamental operation in a wide range of industries with continuous mixing gaining popularity due its higher efficiency relative to batch mixing. Ensuring the reliable operation of continuous bulk solids mixers is key but the complex dynamic loading on the mixer drivetrain and the need for uninterrupted operation over long periods of time pose design challenges. At the same time, the traditional design approach, which is heavily reliant on physical prototyping, is time consuming and expensive. Virtual prototyping via a digital twin allows engineers to design faster and at a fraction of the cost.
All requisite files for the example can be downloaded here:
A digital twin of a bulk solids mixer that includes the equipment geometry, electric drivetrain and bulk material can be developed using EDEM, MotionSolve, PSIM and Activate.
A mixing simulation using the digital twin is shown in the below video and reveals the complex force chains that develop in the bulk solid. An overview of the digital twin components is shown in Figure 1 where:
-
- EDEM simulates the complex dynamic behaviour of the bulk material
- MotionSolve is used to build a multibody dynamics model of the mixer shaft, including the mixer shaft inertia
- PSIM is employed to model the power electronics system, including the motor, inverter, control loop, and other electric components
- Activate is used to orchestrate and connect all simulation tools together
Figure 1 - Overview of Mixer Digital Twin
The digital twin reveals the complex behaviour of the system that results from the interaction of the electric drivetrain and the particle induced forces on the shaft as shown in Figure 2.
Figure 2 - Complex Dynamic Loading on the Mixer Shaft, the Motor Torque, and Shaft Speed
The set-up in this example is split into five different parts:
- 3D modelling the CAD geometry
- Modelling the bulk solids material with EDEM
- Creating a multibody dynamics model for the mixer shaft with MotionSolve
- Modelling the power electronics with PSIM
- Coupling all simulation tools together with Activate
1. CAD Modelling
- Create the 3D model of the mixer shaft and casing shown in Figure 3, using Altair CAD tools like Inspire or Inspire Studio,
- For further details visit the Inspire Tutorials or Inspire Studio Tutorials
- Save each part of the CAD as an .STL file. CAD files for the mixer geometries are provided in the attached .zip file.
Figure 3 - Mixer Shaft and Shell CAD Model in Inspire
2. EDEM:
To simulate the bulk solid mixing process using EDEM:
- Import the mixer casing CAD geometry into EDEM and define the equipment material properties for it
- In the Simulator tab, select Geometries > Add Geometry > Cylinder, with the settings specified in Figure 4
![]() | ![]() | ![]() |
Figure 4 - Hopper Geometry Specifications
- Utilise the powders database to define a bulk solids to be processed inside the continuous mixer. For the sake of this tutorial only one material type is defined.
- Create a copy of the cylinder geometry with closed ends, making sure to set it to a virtual type and add a factory. Right click on the factory and select change factory type to change it to a static factory, as shown in Figure 5
- For an introduction to EDEM, visit the EDEM eLearning Introduction
- For further information on the optimisation and analysis of bulk solids mixing in EDEM, visit this tutorial
![]() | ![]() |
![]() |
Figure 5 - Factory Definition for Segregated Particle Generation
3. MotionSolve:
Inside MotionView (MotionSolve’s preprocessor), implement the following steps for the multibody model of the mixer:
- Define solver variables for the magnitude of the applied torque as well as the shaft’s rotational speed, as shown in Figure 6
Figure 6 - Solver Variables Definition
- Extract the rotational speed of the mixer shaft by defining its expression to be `WX({sys_GenericContiniousMixer.Part_1.cm.idstring})`. This will be fed into the PSIM model
- Import the mixer shaft geometry and define a revolute joint (under Add > Constraint), as shown in Figure 7
Figure 7 - Revolute Joint Definition
- Assign the torque coming from the PSIM model to the shaft, by giving Tx the value of Torque_out (under Add > Force Entity) using sv_3.VARVAL(), as shown in Figure 8
Figure 8 - Torque, Tx, Definition
- Group the torque and the rotational speed into ControlInput and SystemOutput solver arrays, respectively. These will be used as input and output connections in Activate
- Create an EDEM subsystem under the Assembly tab, as shown in Figure 9
Figure 9 - EDEM Subsystem in MotionView
- Import the mixer shaft geometry into EDEM via MotionView, by enabling the coupling server, as shown in Figure 10. For more information on this step and on coupling EDEM and MotionSolve in general, see this tutorial
Figure 10 - Enabled EDEM Coupling Server
4. PSIM:
To introduce power electronics simulation and implement control on the mixer shaft rotational speed:
- Add a motor controller, motor, inverter, and other components in PSIM, as shown in Figure 11 (all files are attached)
- For an introduction to PSIM watch the Getting Started with PSIM video
- For further details on designing electric drivetrains with PSIM see this article and/or this webinar.
Figure 11 - PSIM Control Loop
5. Activate:
To connect all simulation tools in Activate:
- Add PSIM and MotionSolve blocks, under Palettes > Activate > CoSimulation and select the proper input files for each, as shown in Figure 12
Figure 12 - MotionView and PSIM Input Settings
- Create a target speed block and connect it to the rpm_ref input for PSIM, then connect the output of the MotionSolve to the remaining input (shaft_speed_in) of the PSIM block, as shown in Figure 13
Figure 13 - Activate Control Loop
To run the simulation:
- Enable coupling mode in EDEM, as shown in Figure 9
- You can set the total simulation time under Simulation Setup in Activate, and press the Start button to start the simulation, as shown in Figure 14
Figure 14 - Final Time Settings in Activate
- Matching timesteps in EDEM-MotionView-Activate-PSIM will produce the highest-fidelity simulation, with the disadvantage of increased processing time. It may be possible to increase some of the timestep in order to speed up the simulation, but this may effect the results. Table 1 below shows the timestep settings for all tools.
Table 1 - Simulation Timesteps
Activate | EDEM |
MotionSolve | MotionSolve-EDEM Coupling |
PSIM |
Conclusions:
A digital twin of a bulk solids mixer that includes the mixer geometry, electric drivetrain and bulk solid can be generated by coupling EDEM, MotionSolve, PSIM and Activate. The digital twin enables rapid virtual prototyping of designs, reducing time and costs.
Further links:
Learn how to optimize the mixer shaft design and operation in this article:
Combining Machine Learning and Simulation for Continuous Mixing Optimization