Joule Heating Coupled Electrothermal Analysis on a Tungsten Filament with OptiStruct
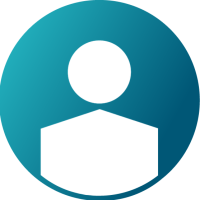

OptiStruct supports electrical analysis, as well as Joule heating with thermal analysis. An example of the Joule heating effect is shown for a tungsten filament to illustrate an application of steady-state coupled electrothermal analysis.
Theory
To model Joule heating, a steady-state electrical conduction subcase (SSEC) is set up which calculates the unknown currents based on the applied voltage (electric potential).
The finite element equation solved to calculate the electrical response in a structure is based on the electrical conductivity of the material, the applied load, and electric potential.
This is derived from Ohm’s Law, which predicts that the electric potential difference is related to the current and electrical resistance:
Joule’s Law relates the power generated by an electrical conductor to its applied current and resistance.
To apply the Joule heating effect, a heat transfer subcase must reference the electrical subcase with the JOULE field. The percentage of electrical energy that is converted to thermal energy for Joule heating is defined on the JHFRAC field. In the heat transfer subcase, the unknown temperatures are determined by the fixed temperature boundary conditions and the thermal loading generated by the Joule heating. In the simple case where the Joule heating is the only thermal load and there is no assumed free convection this equation is solved for the temperatures:
2-way coupling between the electrical and thermal subcases is necessary because the electrical resistivity is temperature dependent. In this case, the electrical analysis determines the amount of power used for joule heating, and the thermal analysis determines the material properties for the electrical analysis since these are temperature dependent. The diagram below illustrates the subcase setup for a 2-way coupled analysis with steady-state electrical and heat transfer subcase definitions (ELEC and HEAT).
An iterative solution determines the final temperature profile since multiple iterations to solve the coupled electrical and thermal subcases are required.
model Setup
To demonstrate Joule heating analysis with OptiStruct, an example of a tungsten filament is shown. Tungsten has been widely used in heating and lighting applications such as incandescent light bulbs because it has a high melting point and modulus. It gives off light in a spectrum from infrared to white as the temperature increases.
SI units are assumed, and the various electrical and thermal units for this example are shown.
Physical quantity | Example model units |
Electrical Resistivity | ohm-m |
Electrical Potential | V |
Current Density | A/m2 |
Thermal Conductivity | W/(m*K) |
Temperature | K |
Electrical/Heat Power | W |
Joule Loss Density | W/m3 |
In the model, a hexahedral mesh is used to model the filament. The mesh is shown below. In the steady-state electrical conduction subcase, an enforced voltage is applied by fixing one end of the cross-section of the filament at 0 V and the other end at 0.3 V. This enforces an electric potential difference across the filament, simulating the flow of current.
The MAT1EC card is used to specify the electrical resistivity of tungsten. At 300° K, this is assumed to be 5.65E-8 ohm-meters. This is inversely set in the electrical conductivity matrix in the finite element solution. A scale factor to account for the temperature-dependence of the electrical resistivity is defined using a TABLEM1 table referenced on a MATT1EC card in the temperature range from 273 to 3000° K.
For the heat transfer analysis, fixed temperature boundary conditions are defined on the end cross-section for the filament at 300° K:
The MAT4 card is used to specify the thermal conductivity for tungsten. A thermal conductivity of 197 W/(m*K) is used. In the coupled electrothermal heat transfer analysis, the JOULE field is called in the heat transfer subcase to apply the thermal loading to the model based on electrical power.
For coupled analysis, the electrical analysis solves for the electrical potential in the structure, and the power is used for the thermal analysis. As the temperature is updated, the electrical resistivity changes, and therefore a 2-way coupling is necessary to solve this problem for the final voltage and temperature distribution.
results
The base results of a coupled electrothermal analysis are the voltage and temperature profiles. The electrical results also include current density and joule loss density.
Electric Potential (V):
Electrical potential is the voltage in the system.
Current Density (A/m2):
Current density is the current flowing through a particular cross-sectional area.
Joule loss density (W/m3):
Joule loss density is the electrical power per volume lost to heat generation by the Joule effect.
Final temperature profile:
The final temperature profile from heat transfer analysis shows the effects of Joule heating. The temperature at the center of the filament is approximately 1800° K.
conclusion
OptiStruct can be used to model electrothermal analysis for heating applications. The model file tungsten_filament_joule_heating.fem is attached. For more information about Electrical Analysis with OptiStruct, see the OptiStruct User’s Guide:
https://2022.help.altair.com/2022.1/hwsolvers/os/topics/solvers/os/electrical_analysis_r.htm#reference_wnm_j1b_krb