How to Choose Main-and-Secondary-Surface in OptiStruct
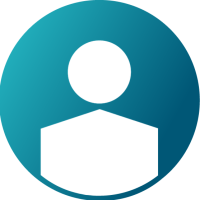

How to Choose Main-and-Secondary-Surface in OptiStruct
In addition to achieving convergence, effective contact detection is the most critical point in contact problems. A lot of experience is needed to cover all possible situations. Not everything is published. Therefore, only a few basic ideas can be outlined here.
The main surface will orient the search for creating the contact pair according to its normal in most cases, whereas the secondary surface will play that role for the S2S CONSLI contact pair in LGDISP analysis.
When choosing the main and secondary sides it must be avoided that non-detectable penetrations occur, so the choice of main-secondary surfaces is very important when creating contact pairs.
Please refer to our documentation to learn more about contact and all settings in the link below.
https://help.altair.com/hwsolvers/os/topics/solvers/os/contact_os_c.htm?zoom_highlight=contact
Basic rules for selecting the main surface
- The surface with the coarser mesh becomes the main (the wrong choice is shown):
Figure 1 Wrong main-secondary direction in case of non-equal mesh size
Although this effect is more sensitive for N2S contact, this rule is recommended for S2S as well.
- The larger surface becomes the main
Figure 2 Correct and wrong main-secondary definition for the larger surface
- The concave, less curved, or flat surface becomes the main
Figure 3 Wrong main-secondary definition in case of plane-convex contact
- The surface with the higher order elements becomes the main because it can show a nearly smooth surface
Figure 4 Contact with elements of higher order shape functions
- The surface of the stiffer material becomes the main.
This rule is particularly effective when both surfaces have the same element size. Otherwise, finer mesh should be secondary instead.
OptiStruct writes a text file that provides information for nodal linear stiffness for penalty calculation in the .out file. This is helpful when defining the main-secondary surface, specifically in case of convergence issues. Try switching main-secondary surfaces for <w> contact pairs.
Figure 5 Summary of reference nodal stiffness for penalty calculation from the .out file
Symmetric contact
Sometimes, these rules can contradict each other. In such instances with N2S being used, symmetric contact is recommended, wherein the contact definition is duplicated while interchanging the roles of the primary and secondary surfaces. OptiStruct offers a convenient switch for this purpose. It is possible that, in certain scenarios, both main and secondary contact surfaces may partially close at the same location, or perhaps only one of them does. OptiStruct contact algorithm effectively manages this situation, ensuring that no redundant contact forces are exerted. Without this precaution, the stress distribution within the underlying elements could become inaccurate.
The pictures below show symmetric contact results using N2S and S2S.
Figure 6 Contact Force results for N2S Symmetric (left) and Unsymmetric contact swapping M-S (right)
Figure 7 Contact force results for S2S Symmetric (left) and Unsymmetric contact swapping M-S (right)
In the pictures above, the left cube is finer mesh with steel material, right is coarser with rubber material (MATHE). The following statements can be noticed from the results:
- For N2S convergence and accuracy are strongly dependent on the Main-Secondary choice.
- For S2S convergence and accuracy are not so dependent on the Main-Secondary choice as per N2S.
- Symmetric contact here is recommended for N2S since some rules contradict each other (e.g., fine mesh rule and stiff material rule).
- OptiStruct doesn’t duplicate double contact forces for symmetric contact.